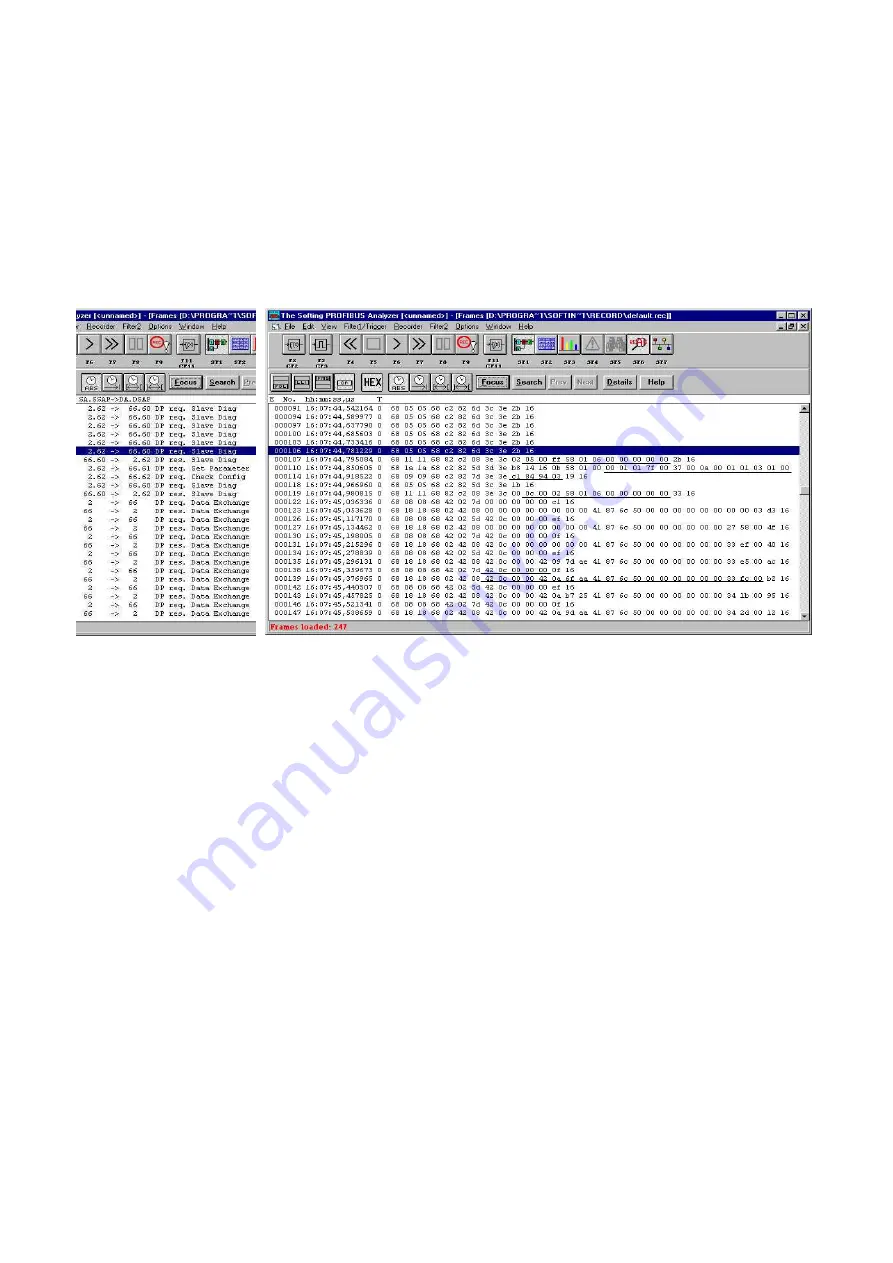
38
Installation and Operation Manual
X-DPT-Profibus-DP-Interface-eng
PN 541-C-068-AAG
November, 2008
For STEP7 (Siemens) the following routines can be used:
SFC14, DPRD_DAT, read consistent data of a standard DP slave.
SFC15, DPRW_DAT, write consistent data to a standard DP slave.
Please, consult the manufacturer of your master device for all detailed informa-
tion about consistent data exchange.
4.7
EXAMPLE OF THE PROFIBUS-DP COMMUNICATION PROCEDURE
We have just seen the description of the PROFIBUS-DP communication
procedure separate Now, by showing a bus trace of the communication proce-
dure of one MFC slave the just described items will be recognised.
1. From top, line no. 91, until the selected blue line, line no. 106, the master
(Source Address (SA) 2) requests for diagnostics of a slave (Destination
Address (DA) 66) but no response is given.
2. At line no. 107 the slave is reacting with the diagnostic message, including
the 5 manufacturing specific bytes. In this case all bytes are 00, which
indicates no alarm sources are active.
3. First is sent the Set Parameter message, line no. 110. The parameters as
described in the parameterisation message can be recognized here, see
the underlined data.
4. Next is the Check Configuration message, line no. 114. Here we can
recognise the module 3 selection of an MFC.
5. And before going into the data exchange mode, first a diagnostic message
is sent to check if the unit is still OK. On line no. 119 the unit here re-
sponse with ‘all OK’.
6. And finally the unit is in data exchange mode, starting from line 122. On
line 138 we can recognize the 5 output bytes of which the first 4 are the
floating point value of 35 (See also appendix B for more info on the floating
point value).
Next line is showing the 21 input bytes.
The data exchange mode is ongoing and will remain exchanging input and
output data as long the master is running.