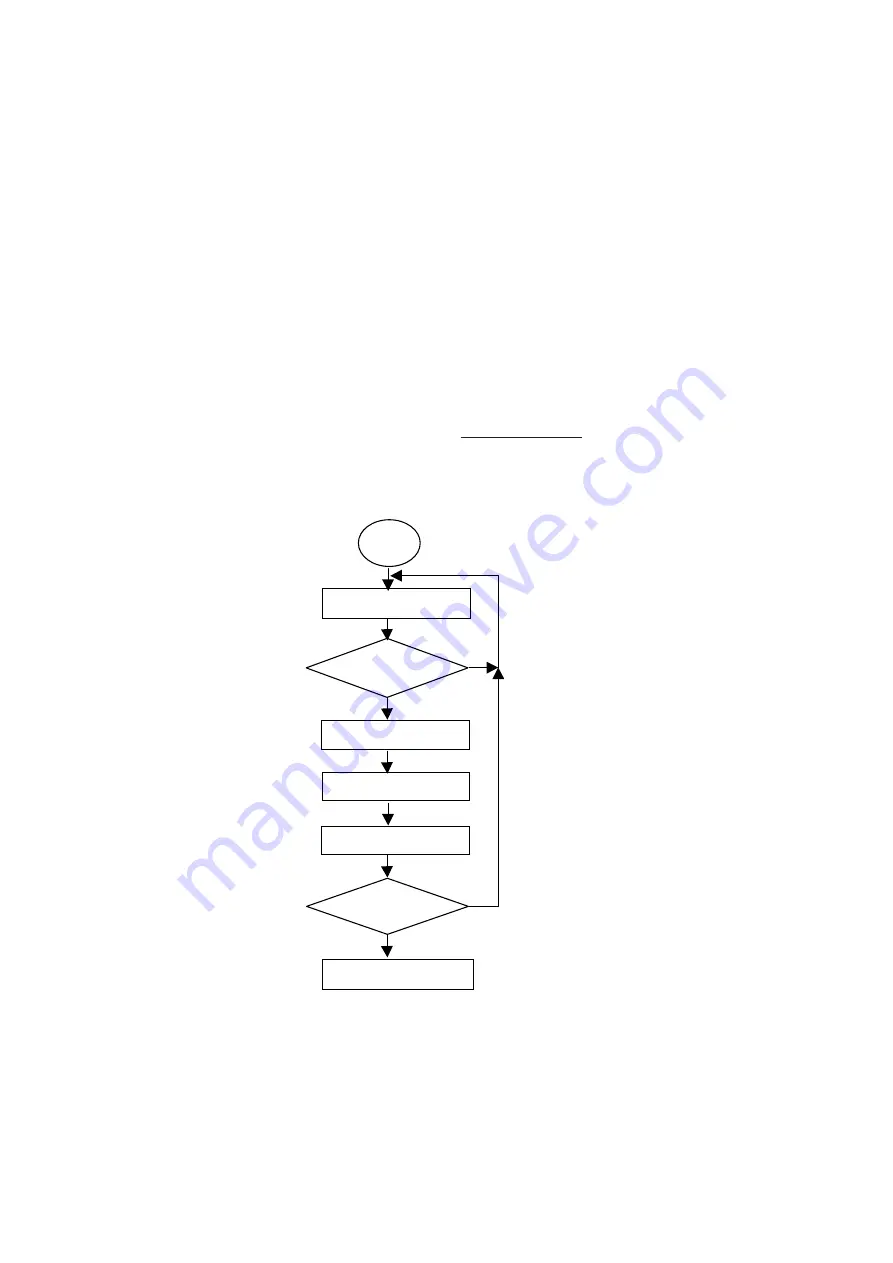
23
Installation and Operation Manual
X-DPT-Profibus-Interface-eng
PN 541-C-068-AAG
November, 2008
4
Slave configuration
4.1
INTRODUCTION
The purpose of the bus system is the fast serial linkage of the de-central
peripherals (Mass Flow Controllers - Meters) with the central Master (control-
ler). In addition to the Input/Output data also parameter data, configuration data
and diagnosis data is transferred.
Many Profibus masters (controllers) need a configuration program with which
the network structure is described, e.g. SIEMENS STEP7 for the S7 controller.
These programs require the unit master file (GSD file). These files can be
required from the manufacturer or in case of PNO certified equipment, they can
be retrieved from the www.profibus.com web site.
For the Profibus-DP network configuration of the Smart Mass Flow Controllers
/ Meters slaves the following GSD files are provided:
1. BIMF5801.GSD - Smart Mass Flow Controllers (MFC)
2. BIMF5861.GSD - Smart Mass Flow Meters (MFM)
and can be found on the www.profibus.com web site or requested at your
Brooks Sales
representative.
4.2
ILLUSTRATION OF THE PROFIBUS-DP COMMUNICATION
PROCEDURE
Power up and/or reboot of master
system
Check if slave(s) are available
If yes, continue the initialisation
procedure
Set parameters
Check configuration mode
Check diagnostic to see if slave is
OK
Go into data exchange mode
4.3
PARAMETERIZATION OF THE SLAVE (MASS FLOW
CONTROLLER)
When the system is running up, each salve receives parameters from the
master. The first 7 bytes are defined by the DIN 19245 T3 standard (bus
parameters). The following bytes are user parameters (User_Prm_Data). The
input of the parameter data takes place in different ways in the various configu-
ration programs (e.g. STEP7). In many cases, the bytes defined by the stand-
ard are read from the GSD file.
yes
no
Start
Read diagnosis
Read diagnosis (4.6)
Cyclical data transfer (4.7)
Write parameter (4.3)
Write configuration (4.4)
Fault ?
Diagnosis
OK?