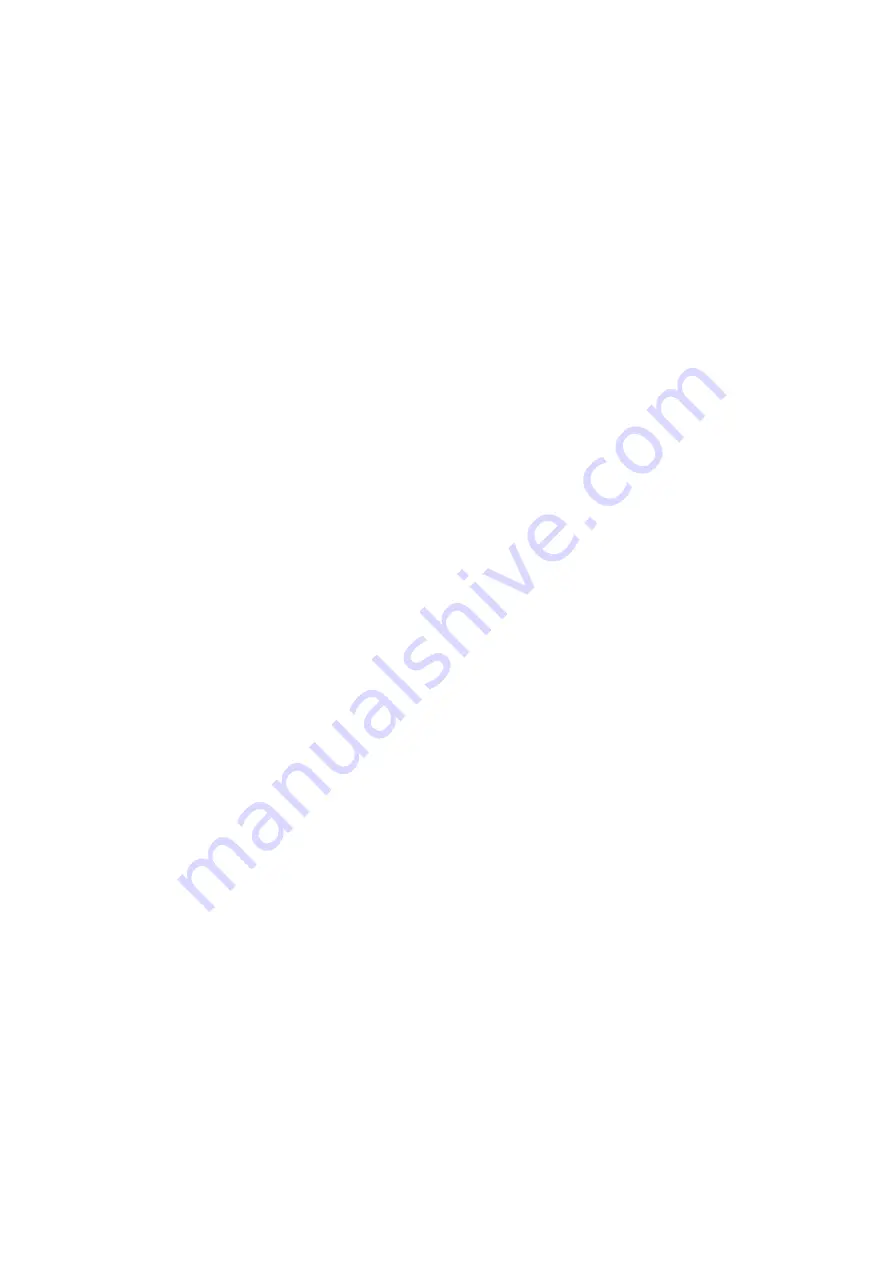
47
Installation and Operation Manual
X-DPT-Profibus-Interface-eng
PN 541-C-068-AAG
November, 2008
A.1
Global control commands
The Profibus standard provides the possibility to issue global command to one or
more slave devices. These commands are pre-defined bit mapped commands in
the global command data byte, and both the Smart Mass Flow Meter and Con-
troller models will support two of these commands.
Sending a global command involves the use of the global station address, number
127 as well as the group address, set at parameterization. Both devices will
support the fail- safe option as well as the sync/unsync option. Both will not
support the freeze/unfreeze option. Refer to EN 50170, part 3, section 8.3.7:
Control commands to DP-slave
for a detailed description of this command and
the features.
A.2
Fail-safe option
Both device types will support the fail-safe option. This feature allows a global
clearing of output data by a Clear-data command, which may be send by the
master to all or to a selected group of devices if a network failure is detected by
the master. If bit 1 = Clear-data is set in the global command data byte, the
device will enter the fail-safe mode, i.e. it will accept the next data exchange
request messages if they have no data bytes. The device behaviour to this
must pre-programmed. A device will leave the fail-safe mode if a data exchange
request is received with valid data bytes or if a global control command is
received with bit 1 in the data byte cleared.
The failsafe parameter applies to Smart Mass Flow Controller only. Through
this parameter the user can select the type of failsafe of the MFC in case of
bus failure or a global ‘Clear’ command. The failsafe state determines how the
MFC is acting if in previous described situations no setpoint value is coming
through anymore. Per default the unit is using selection 1 and internally reset
its setpoint value to zero and makes the valve powerless. The latter means that
a mechanical normally closed valve closes and a mechanical normally open
valve opens. This is identical to the situation when the MFC looses it power
supply.
In the last two selections the valve can be forced in a position in spite of the
mechanical construction.
The first option, ‘no effect’, means that the MFC is continuing controlling flow
using the last setpoint which was sent over the profibus network or, in case of
setpoint source is set to analogue, continues flowing the analogue setpoint
value.
A Smart Mass Flow Meter will simply accept the no-data messages with no
special change in behaviour, i.e. it will continue to accept (empty) data ex-
change requests and it will continue to respond with measurement data. This
does not depend on whether any of the parameters in the request message
has been enabled or not.
A.3
Sync/unsync option
In addition both device model types will support the sync/unsync option. This
feature allows a global, synchronized processing of the latest entered output
data. If the Sync bit is set in the global command data byte, the device will still
accept data exchange request message with valid data bytes, but they will not
be processed internally. A succeeding message with non-zero contents will
overwrite the previous entered data, but the data is still not processed. Upon
reception of a global control command with the Unsync bit set, the last entered
values will be processed. The sync/unsync cycle applies only to the data bytes
entered through the data exchange request message, i.e. disabled parameters
are not effected.
Appendix A PROFIBUS-DP message services