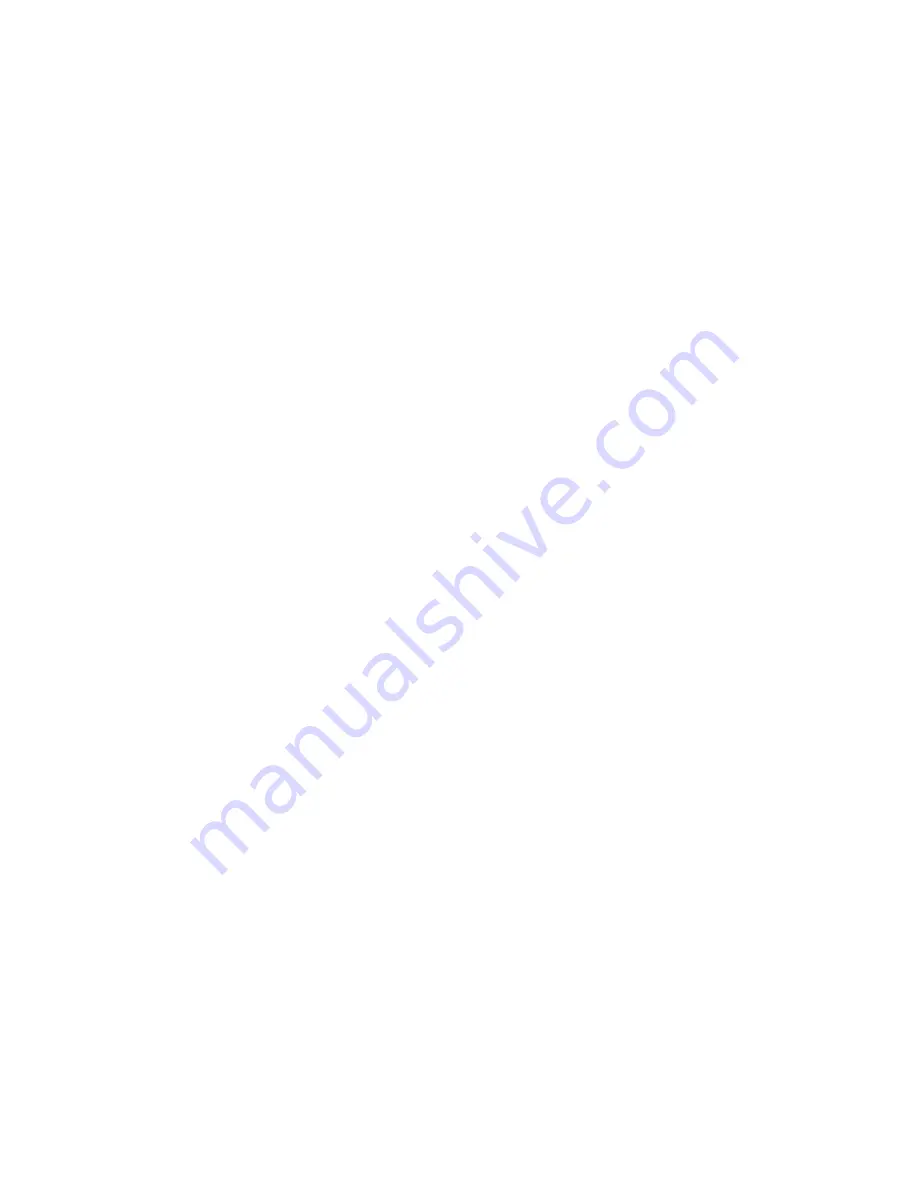
3-15
HYDRAULIC SYSTEM
The IC-200 hydraulic system consists of 2 subsystems, driven by a double pump with a single
inlet port. The 29 GPM (110 L/min) vane pump supplies the hydrostatic steering function and
the boom and outrigger functions. The hoist and brake booster are powered by the 34 GPM
(129 L/min) vane pump.
The boom, outriggers, hoist and opt ional front winch are controlled by one valve assembly.
The 29 GPM (110 L/min) pump flow enters the steering flow control valve first and then flows
into the left-hand section of the control valve assembly supplying the swing, telescope, boom
and outrigger sections. The flow from the 32 GPM (129 L/min) pump enters the brake booster
flow control valve first and all but 4 GPM (15 L/min) is directed to the inlet section to the left of
the hoist valve. Adjustment procedures for the crane hydraulic functions are given on page 3-
21 through 3-23. The schematic of the hydraulic system is shown on the next page.
STEERING SYSTEM
The steering system is shown in the schematic on the next page. The IC-200 steering system
is a load-sensing, demand-type system that takes only as much flow as is needed when steer-
ing and directs the excess flow to the control valve for boom and outrigger functions. The pri-
ority flow-control valve is in the line between the 29 GPM (110 L/min) pump section and con-
trol valve.
Oil from the 29 GPM (110 L/min) section of the pump goes into the priority valve at port "P."
When no st eering is r equired, the entire flow goes through the priority valve and leaves
through port "EF" to the crane valve. The crane operating speed is not affected, since there is
no loss of volume passing through the priority valve.
When the steering wheel is turned, the load-sensing line signals the priority valve to divert the
required amount of oil to the steering control unit to meet the steering system requirements.
The excess oil, not required for steering, flows to the crane control valve as usual. Since the
amount of oil r equired for steering is usually a sm all portion of the pump output, the crane
control valve is always operational while the unit is being steered. Crane operation speed is
reduced such a slight amount it is usually not noticed.
The steering control unit is non-load reactive. This means that bumps, curbs, and obstacles
cannot change the steering angle and are not felt in the steering wheel. It also means that the
wheels do not recenter when the steering wheel is r eleased. T he steering wheel must be
turned back to center at the end of a turn. The steering system pressure was set at 1800 PSI
(124 bar) at the factory, and this should not need adjustment.
The three steering modes are selected by a switch on the dashboard, which activates the au-
tomatic alignment system. Electronic proximity sensors and logic controls delay the switching
of the steering mode until the wheels are centered. The proximity sensors should be cleaned
periodically with a rag to prevent dirt buildup from blocking their operation.
Содержание IC-200-2H
Страница 6: ...1 2 IC 200 2H DIMENSIONS Courtesy of Crane Market...
Страница 7: ...1 3 IC 200 3H DIMENSIONS Courtesy of Crane Market...
Страница 8: ...1 4 IC 200 H TURNING DIMENSIONS Courtesy of Crane Market...
Страница 18: ...Courtesy of Crane Market...
Страница 32: ...2 14 Courtesy of Crane Market...
Страница 33: ...2 15 Courtesy of Crane Market...
Страница 53: ...3 9 IC 200 LUBRICATION CHART Courtesy of Crane Market...
Страница 60: ...3 16 Courtesy of Crane Market...
Страница 61: ...3 17 Courtesy of Crane Market...
Страница 69: ...3 25 IC 200 3 BOOM CHAIN ADJUSTMENT Courtesy of Crane Market...
Страница 74: ...Powered by TCPDF www tcpdf org Courtesy of Crane Market...