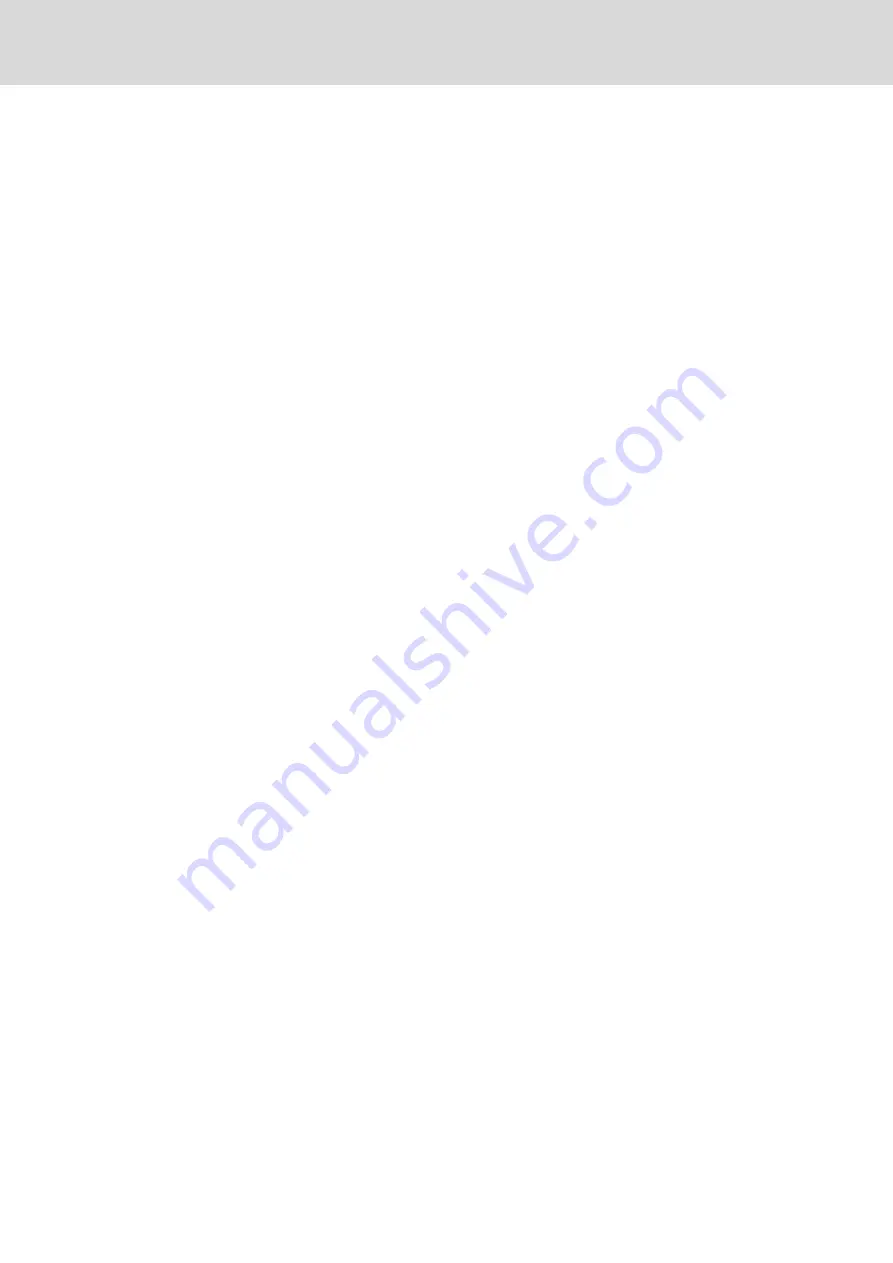
Dangerous movements! Danger to life, risk of injury, serious injury or property
damage!
A risk assessment must be prepared for the installation or machine, with its
specific conditions, in which the components of the electric drive and control
system are installed.
As a result of the risk assessment, the user must provide for monitoring func‐
tions and higher-level measures on the installation side for personal safety. The
safety regulations applicable to the installation or machine must be taken into
consideration. Unintended machine movements or other malfunctions are pos‐
sible if safety devices are disabled, bypassed or not activated.
To avoid accidents, injury and/or property damage:
●
Keep free and clear of the machine’s range of motion and moving machine
parts. Prevent personnel from accidentally entering the machine’s range
of motion by using, for example:
–
Safety fences
–
Safety guards
–
Protective coverings
–
Light barriers
●
Make sure the safety fences and protective coverings are strong enough
to resist maximum possible kinetic energy.
●
Mount emergency stopping switches in the immediate reach of the oper‐
ator. Before commissioning, verify that the emergency stopping equip‐
ment works. Do not operate the machine if the emergency stopping switch
is not working.
●
Prevent unintended start-up. Isolate the drive power connection by means
of OFF switches/OFF buttons or use a safe starting lockout.
●
Make sure that the drives are brought to safe standstill before accessing
or entering the danger zone.
●
Additionally secure vertical axes against falling or dropping after switching
off the motor power by, for example,
–
mechanically securing the vertical axes,
–
adding an external braking/arrester/clamping mechanism or
–
ensuring sufficient counterbalancing of the vertical axes.
●
The standard equipment motor holding brake or an external holding brake
controlled by the drive controller is not sufficient to guarantee personal
safety!
●
Disconnect electrical power to the components of the electric drive and
control system using the master switch and secure them from reconnec‐
tion ("lock out") for:
–
Maintenance and repair work
–
Cleaning of equipment
–
Long periods of discontinued equipment use
●
Prevent the operation of high-frequency, remote control and radio equip‐
ment near components of the electric drive and control system and their
supply leads. If the use of these devices cannot be avoided, check the
machine or installation, at initial commissioning of the electric drive and
control system, for possible malfunctions when operating such high-fre‐
quency, remote control and radio equipment in its possible positions of
normal use. It might possibly be necessary to perform a special electro‐
magnetic compatibility (EMC) test.
Bosch Rexroth AG
DOK-SUPPL*-VPB*40.1***-PR02-EN-P
Rexroth IndraControl VPB 40.1 Control Cabinet PC
14/81
Safety Instructions for Electric Drives and Controls
Содержание Rexroth lndraControl VPB 40.1
Страница 1: ...Electric Drives and Controls Pneumatics Service Linear Motion and Assembly Technologies Hydraulics ...
Страница 6: ...Bosch Rexroth AG DOK SUPPL VPB 40 1 PR02 EN P Rexroth IndraControl VPB 40 1 Control Cabinet PC IV 81 ...
Страница 20: ...Bosch Rexroth AG DOK SUPPL VPB 40 1 PR02 EN P Rexroth IndraControl VPB 40 1 Control Cabinet PC 18 81 ...
Страница 48: ...Bosch Rexroth AG DOK SUPPL VPB 40 1 PR02 EN P Rexroth IndraControl VPB 40 1 Control Cabinet PC 46 81 ...
Страница 72: ...Bosch Rexroth AG DOK SUPPL VPB 40 1 PR02 EN P Rexroth IndraControl VPB 40 1 Control Cabinet PC 70 81 ...
Страница 78: ...Bosch Rexroth AG DOK SUPPL VPB 40 1 PR02 EN P Rexroth IndraControl VPB 40 1 Control Cabinet PC 76 81 ...
Страница 80: ...Bosch Rexroth AG DOK SUPPL VPB 40 1 PR02 EN P Rexroth IndraControl VPB 40 1 Control Cabinet PC 78 81 ...
Страница 83: ...Notes DOK SUPPL VPB 40 1 PR02 EN P Rexroth IndraControl VPB 40 1 Control Cabinet PC Bosch Rexroth AG 81 81 ...