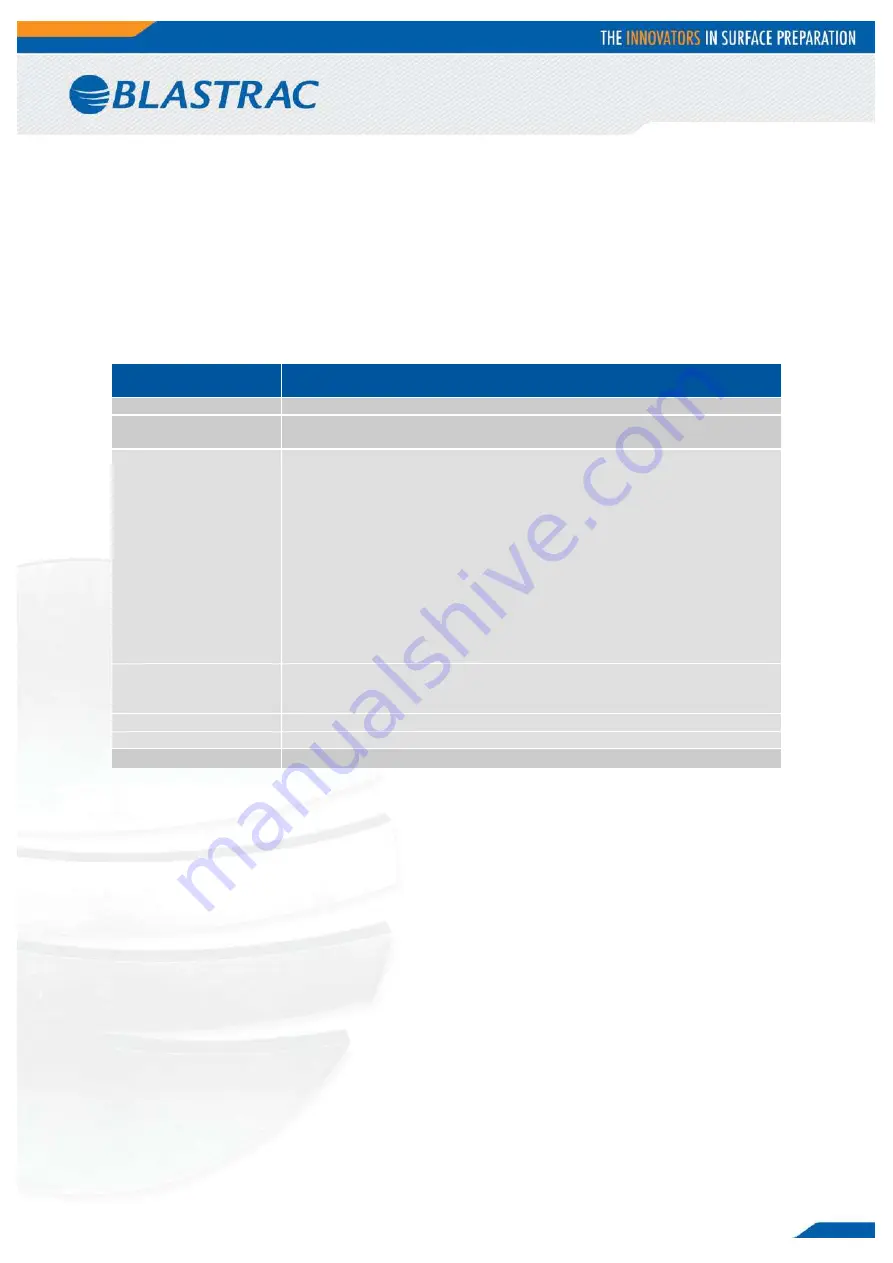
16
6. Maintenance
Pay attention to Chapter 3
"Safety"
during maintenance and repair works.
Failures due to inadequate or incorrect maintenance may generate very
high repair costs
and long standstill
periods of the machine.
Regular
maintenance therefore is imperative.
Operational safety and service life of the machine depends, among other things, on proper maintenance.
The following table shows recommendations about time, inspection and maintenance for the normal use of the
machine.
Operating hours/
time period
Inspection points, maintenance instructions
12 h after repairing
Check all accessible screw connections for tight seat.
Every 3 hour
Check the hopper, the abrasive valve and blast wheel unit for foreign
matter and large contaminants.
Daily and prior to
starting work
Check that all safety devices working adequate.
Check the abrasive valve, magnet- and rubber sealing.
Check the blastwheel, control cage and blast housing.
Check the electric connections for sediments of dirt or foreign bodies.
Check the electric motors for dirt and other contaminants.
Check all safety devices working adequate.
Clean the inside of the electrobox.
Check the function of the residual current operated device.
Check the hose connections for tightness and fixed seat.
Check all hoses on the machine for damages or leakage.
Make sure that the dust collector is fully functional.
Check the wall sensor.
Check the underpressure sensor.
Every 50 hours
Replace the valve rubbers of the abrasive valve.
Clean the filter and hose of the vacuum guard.
Replace the ventilation filter of the electrobox.
Every 250 hours
Overhaul of the abrasive valve.
Every 3 months
Inspect and clean the electrical motors.
Annually
Full overhaul and cleaning of the complete machine.
The time indications are based on uninterrupted operation. When the indicated number of working hours is not
achieved during the corresponding period, the period can be extended. However a full overhaul must be carried
out at least once a year.
However a full overhaul and a technical inspection must be carried out at least once a year, consisting of
inspection of filters for damage, air tightness of the machine and proper function of the control mechanism. This
technical inspection shall be carried out by the manufacturer or an instructed person.
Due to different working conditions it can’t be foreseen how frequently inspections for wear check’s, inspection,
maintenance and repair works ought to be carried out. Prepare a suitable inspection schedule considering your
own working conditions and experience.
Pay attention to unusual noises or strong vibrations. Check for the cause of every big change. Call a technician
if you have doubts about the cause or when a repair without a technician seems not possible without damages.
Only use genuine Blastrac spare parts.
Our specialists will be happy to assist you with more advice.
Содержание 200VMB
Страница 1: ...Original instructions in English OPERATING INSTRUCTIONS 200VMB VERSION 1 2...
Страница 22: ...22 2 Use a brass drift to tap out the side liners...
Страница 23: ...23...