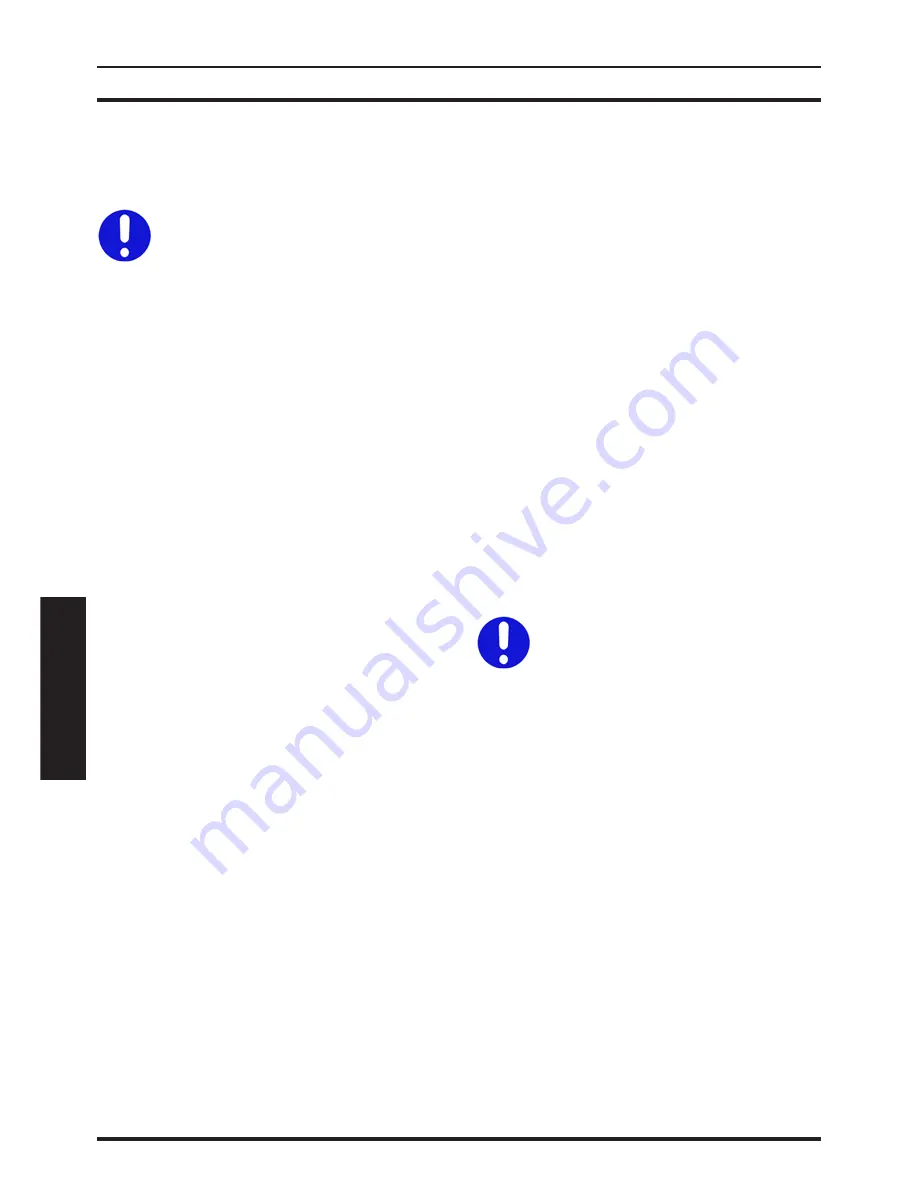
- 38 -
INST
ALLA
TION
INSTALLATION
6
INSTALLATION
6.1 Warnings
The use of gas appliances is
subject to statutory control; it is
essential to observe the current
regulations and laws in force
(see also chapter 5).
The appliance must discharge
combustion products directly
outside or into a suitable ex-
haust duct designed for this
purpose. Combustion products
must be discharged using origi-
nal flue kits only, since they are
integral parts of the boiler.
The appliance is not suitable for
receiving condensate coming
from the combustion products
evacuation system.
Before installing the boiler on an existing
c.h. system, flush it out thoroughly before
fitting the boiler.
This procedure is to remove the presence of
any residues or impurities that could com-
promise good functioning of the boiler.
After washing it is necessary to treat the
plant.
The conventional warranty does not cover
any problems deriving from failure to com-
ply with such provisions.
For Propane, the appliance must also con-
form with the requirements of the distribu-
tors and comply with current Regulations
and laws in force.
The safety relief valve and the condensate
drain must be connected to a suitable drain,
or discharge in a safe manner.
The electrical wiring must conform with cur-
rent Regulations, in particular:
• the boiler must be earthed using the cor-
rect bonding clamp;
• a fused spur isolation switch, must be in-
stalled near to the boiler that allows com-
plete disconnection in overvoltage III cat-
egory conditions.
Refer to section "Electric connection" to
page 45 in this chapter for the electrical
connections.
In no circumstances will the manufac-
turer be held responsible if the warnings
and instructions contained in this manu-
al have not been complied with.
6.2 Precautions for installation
The following prescriptions
must be respected for installa-
tion:
• The boiler must be fixed to a strong wall.
• The dimensions for the exhaust fume duct
(detailed in section "Choice of flu" to page
42) and the correct procedures for install-
ing the duct, depicted in the instruction
leaflet included with the flue kit, must be
complied with during installation.
• To allow maintenance procedures it is
necessary to leave the minimum gaps in-
dicated in Fig. 6.1.
Содержание Activ A 25S
Страница 79: ... 79 MAINTENANCE MAINTENANCE Fig 9 25 Winter ...
Страница 82: ... 82 NOTES ...
Страница 83: ......