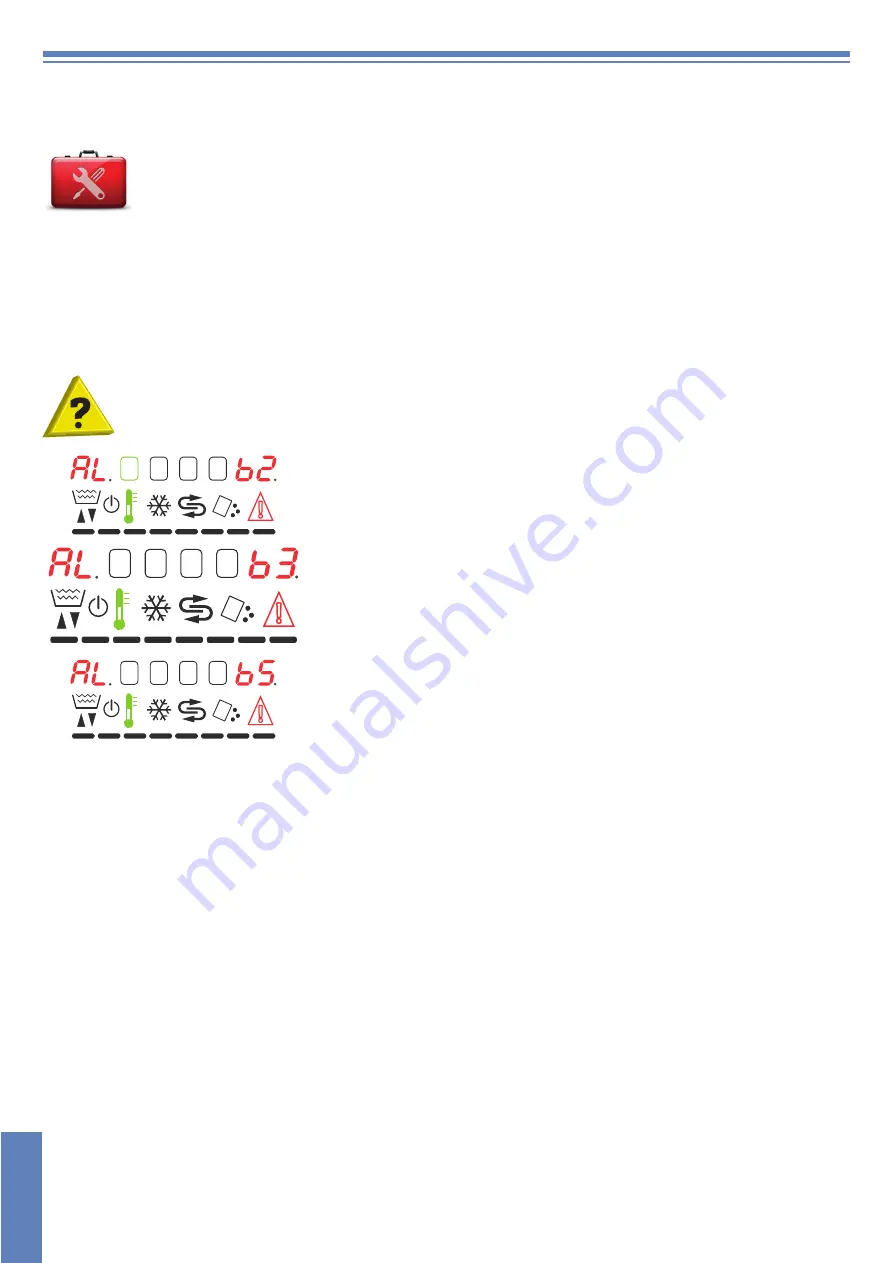
5.2 Special Maintenance
Once or twice a year have a
qualified technician
inspect the machine:
1
Clean the electrovalve filter.
2
To remove residual deposits.
3
To check the watertight of the seals for water loading and unloading connections.
4
Check the perfect state and/or wear of the components. If a component is damaged or oxidized replace it
immediately with genuine spare parts only
5
Check the efficiency of the dispensers
6
Check the efficiency of the door safety switch.
7
Tighten firmly all electrical connections.
Pay attention to do not wet the motor or any electric part.
Perform maintenance with the wall-mounted main switch turned OFF.
Every 3-4 years of machine use, double-check the tightening and the efficiency of all electrical contacts, with special
attention to the contacts of starters and relays.
Increase controls frequency if the machine is operating in heavy or intensive conditions.
6. ALARMS
Alarms will be displayed by the lighting of LEDs. according to their typology.
S
!
1
3
2
4
B2
BOILER PROBE FAILED
The circuit board does not detect the boiler sensor.
Contact Technical Service.
S
!
1
3
2
4
B3
BOILER HEATING ALARM
The factory-set boiler temperature was not achieved in the maximum foreseen
time limit.
Contact Technical Service.
S
!
1
3
2
4
B5
BOILER OVERHEATING
The water temperature in the boiler exceeded 105 °C.
Contact Technical Service.
page 20
EN