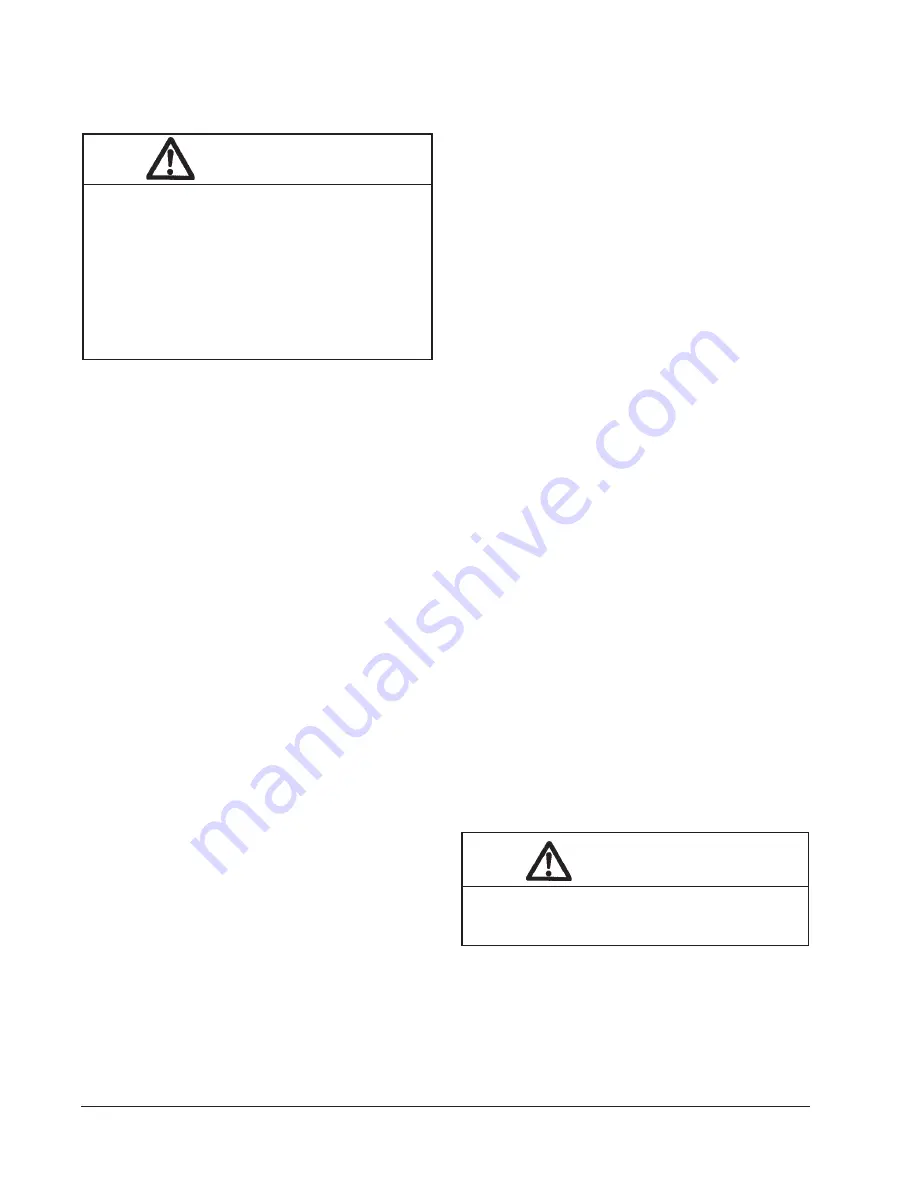
Manual 2100-479
Page
4 of 11
Leak Test
1. Remove gauge port cap from suction and liquid service
valve ports and attach manifold gauge hoses. Connect an
upright R-410A drum to center port of gauge manifold.
Open refrigerant drum valve and manifold high pressure
gauge valve to pressurize system to a positive pressure
with refrigerant vapor. Pressurize the complete system
with dry nitrogen, or CO2 until the pressure reaches 200
psig.
Do not
exceed 250 psig.
2. Close manifold high pressure gauge valve. Check all
soldered joints, including those on the evaporator coil
with an Electronic Leak Detector suitable for use with
HFC refrigerants or R-410A. If a leak is found which
requires soldering, pressure in the system must be bled
off since it is impossible to solder with unit pressurized.
Be sure all leaks are located and marked before bleeding
pressure from system.
ATTACHING MANIFOLD HOSE TO
SCHRADER VALVE
1. Remove cap from valve.
2. Make sure gauge manifold valves are closed.
3. If hose does not have an unseating pin, a number 395
Superior or equivalent unseating coupler must be used.
4. Make sure coupler is lined up straight with Schrader
valve. Screw coupler on to valve.
5. Open gauge manifold valve slightly and purge air from
hose with refrigerant.
6. Read the suction pressure on compound gauge and heat
pressure on pressure gauge.
7. To remove, push end of hose tight against end of Schrader
valve and hold in place while quickly unscrewing coupler
nut from Schrader valve.
8. Remove coupler from Schrader valve. Replace caps on
valve.
3. Close drum valve and disconnect from center port.
Release nitrogen or CO2 into the atmosphere through
suction line of gauge manifold.
4. Correct any leaks and recheck. When leaks, if any,
have been repaired, system is ready to be evacuated and
charged. Relieve all pressure from the system down to 0
psig.
5.
Change
the
���
dryer.
When
leaks,
if
any,
have
been
repaired, system is ready to be evacuated and charged.
Relieve all pressure from the system down to 0 psig.
EVACUATION
Evacuation
An
evacuation
to
500
microns
is
usually
�����
to
remove
moisture from a system using R-22 and mineral oil lubricant.
A 500 micron evacuation, however, will not separate
moisture from Polyol Ester oil (POE) in
R-410A systems.
In
addition
to
a
500
micron
evacuation,
the
liquid
line
���
dryer (R-410A compatible) must be replaced any time the
system
is
open.
When
removing
a
���
dryer
from
a
system,
do not use a torch; use a tubing cutter to avoid releasing
moisture back into the system.
Older R-22 leak detectors, as well as halide torch leak
detectors, will not detect leaks in R-410A systems. Never
use air and R-410A to leak check, as the mixture may
become
����
at
pressures
above
1
atmosphere.
A
system can be safely leak-checked by using nitrogen or a
trace gas of R-410A and nitrogen.
Remember:
Always use a pressure regulator with nitrogen
and a safety valve down stream - set at no more than 150
psig.
1. Evacuate system to less than 500 microns, using a
good vacuum pump and an accurate high vacuum
gauge. Operate the pump below 500 microns for 60
minutes and then close valve to the vacuum pump.
Allow the system to stand for 30 additional minutes to
be sure a 500 micron vacuum or less is maintained.
2. Disconnect charging line at vacuum pump and connect
to refrigerant supply. Crack the cylinder valve and purge
charging line at center on manifold. Then close cylinder
valve.
3. The system is now ready for the correct operating charge
of Refrigerant R-410A.
WARNING
At no time use the compressor to
evacuate the system or any part of it.
WARNING
As a safety measure, it is wise to detach
refrigerant hoses at the lowest pressure
readings on the system. To do this:
A. Put high pressure hose “B” on first.
(Unit should not be running.)
B. Put low pressure hose “A” on second.
(Unit should be running.)
Содержание MULTI-TEC W18AAPA
Страница 2: ......
Страница 31: ......
Страница 77: ......
Страница 80: ......
Страница 84: ...Manual 2110 1442E Page 4 of 11 FUNCTIONAL COMPONENTS SEXP 177 A 1 10 11 12 5 3 4 8 7 7 2 9 6 13 ...
Страница 99: ...Manual 2100 479 Page 6 of 11 FIGURE 1 TYPICAL AIR CONDITIONING SYSTEM COOLING CYCLE MIS 369 ...
Страница 100: ...Manual 2100 479 Page 7 of 11 FIGURE 2 TYPICAL HEAT PUMP SYSTEM COOLING CYCLE MIS 368 ...
Страница 105: ......