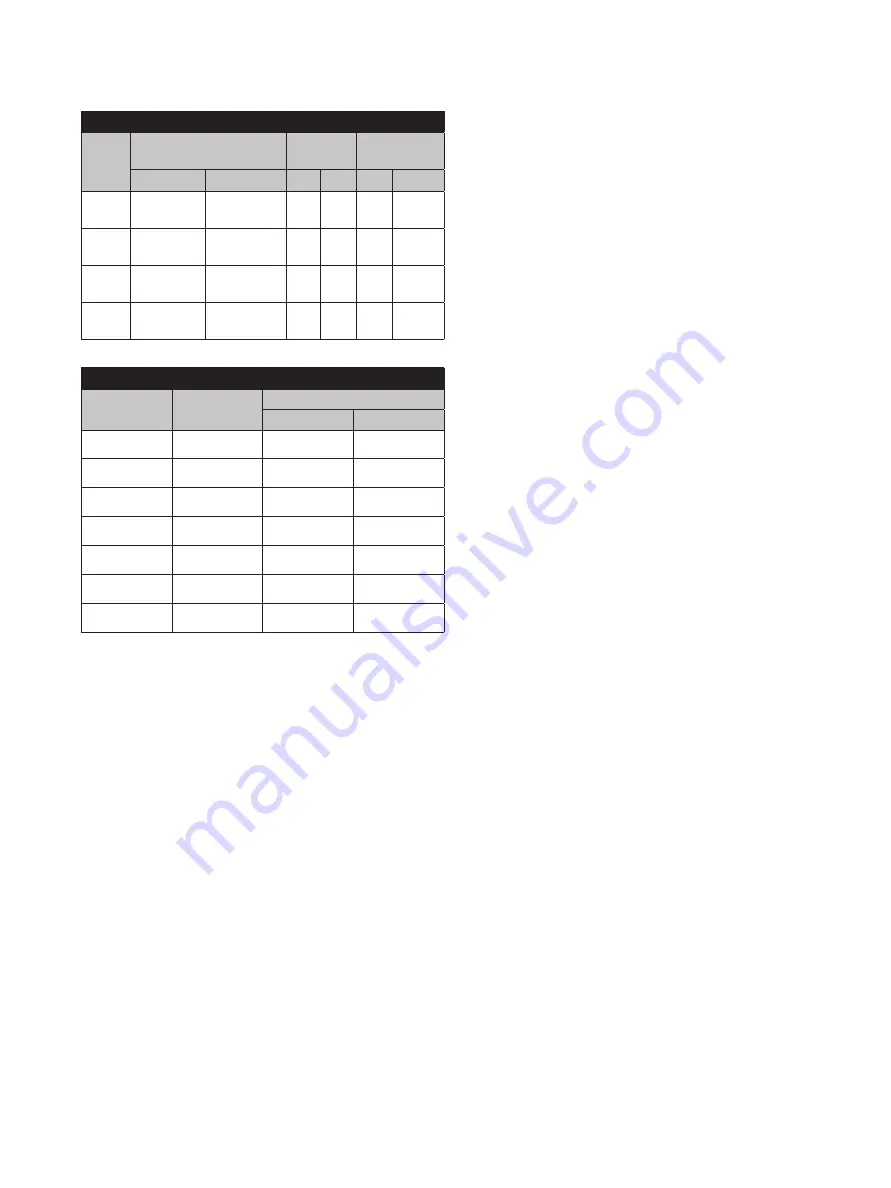
Consolidated 2700 Series Safety Valve Instruction Manual
| 21
© 2022 Baker Hughes Company. All rights reserved.
.05 mm) rock. The disc collar must then be
lowered two additional notches from this initial
position and secured with a stainless steel
cotter pin (see Figure 13).
Note: Failure to provide the recommended
disc rock at assembly will result in a
leaking valve.
g. The desired band width for Consolidated
Series 2700 Safety Valves is shown in Table
3. In addition, the finished machined size of
the spindle nose radius, and the flat diameter
for each orifice size, are also shown in this
Table. If the required bearing band cannot
be obtained by hand grinding, then this
radius should be checked and remachined if
necessary.
h. If the band extends too high on the radius it
will be difficult to rock the disc, and the disc
may lock up under pressure. If the band is too
narrow, the spindle may indent the disc and
again the rock will be lost.
i. When the bearing area is re-established, clean
both surfaces. Then apply lubricant to the
spherical surface of the spindle tip, and work
it into the surfaces by rotating the disc on the
spindle.
7. Guide
Inspect the guide inside diameter for egging, and
ensure the inside surface is smooth. The threads
on the outside must be in good condition to
ensure the upper ring will adjust, even when the
valve is hot. If serious galling is present, the guide
should be replaced.
a. Clearance — The maximum clearance
between the disc holder and guide should be in
accordance with Table 4.
8. Disc Holder
The surface on the end of the disc holder closest
to the disc must be free from steam erosion.
The two small holes must be open to ensure the
passage of steam to the chamber above the disc.
Make sure the outside diameter is not egg shaped
and the surface is smooth. If any small indication
of galling is present, polish the high spots with
an emery cloth. If serious or large-scale galling is
present, the disc holder should be replaced.
9. Disc
Inspect the disc seat for steam cuts, nicks, or
other damage. If the seat step measures less than
dimensions specified in Table 5, this indicates that
the thermal lip has been lapped to the minimum
thickness.
Do not machine any
Thermodisc
™
; however,
a disc that is not below minimum relief can be
lapped to remove minor damage.
a. To Lap Disc Seat
(i) The above lapping method is also used on
the disc seat. When lapping the disc seat,
the disc should be held stationary, but not
rigidly, and the lap moved as above. Use
care not to strike the cone of the disc, as
this would cause the seat to be high on the
inside.
Table 3: Disc to Spindle Lapping Information
Orifice
Nose Radius
Flat
Diameter
Bearing
Band Width
in.
mm
in. mm in.
mm
1
.277
+
-
.000
.004
7.04
+
-
0.00
0.10
.125 3.18 .125 3.18
2
.377
+
-
.000
.004
9.58
+
-
0.00
0.10
.313 7.95 .125 3.18
3, 5,
4, 6
.495
+
-
.000
.005
12.57
+
-
0.00
0.13
.250 6.35 .219 5.56
Q
.582
+
-
.000
.005
14.78
+
-
0.00
0.13
.250 6.35 .281 7.14
Table 4: Allowable Guide / Disc Holder Clearance
Orifice
Temp. Class
Maximum Clearance
in.
mm
#1
B
.005
0.13
D
.008
0.20
#2
B
.008
0.20
D
.012
0.30
#3
B
.010
0.25
D
.015
0.38
#5
B
.011
0.28
D
.017
0.43
#4
B
.012
0.30
D
.018
0.46
#6
B
.016
0.41
D
.016
0.41
#Q
B
.025
0.64
D
.025
0.64
XIII. Inspection and Part Replacement (Cont.)