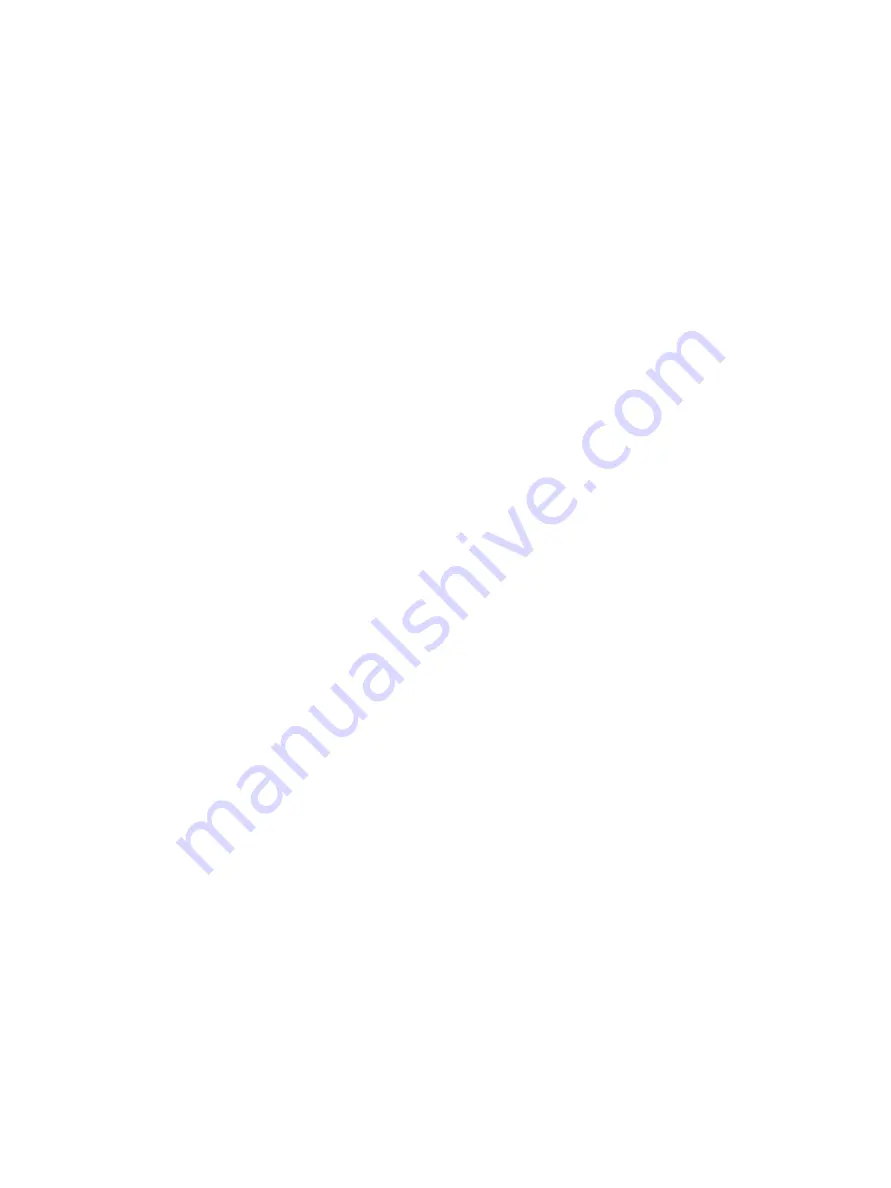
Consolidated 2700 Series Safety Valve Instruction Manual
| 15
© 2022 Baker Hughes Company. All rights reserved.
All face surfaces that require gaskets, to seal pressure,
should be inspected for cleanliness, or any defects that
can cause leakage. Burrs, mashed serrations, uneven
surfaces, etc., are all possible leakage-producing
defects. Proper gasket sizes and pressure ratings
should be checked prior to starting valve installation.
It is of utmost importance that the gaskets used be
dimensionally correct for the specific flange, and that
they fully clear the valve inlet and outlet openings.
Gaskets, flange facings, and bolting should meet the
service requirements for the pressure and temperature
involved. Other valve installation considerations
include:
1. Install the inlet gasket, if required, on the header
mounting flange. Check for cleanliness, surface
alignment condition, gasket condition, etc. When
possible, inlet studs on the mounting flange
should be used to guide the valve on the header
mounting flange. Inlet studs should be lubricated
with the appropriate lubricant.
2. When installing flanged valves, the flange bolts
must be pulled down evenly to prevent body
distortion, misalignment, and leakage.
3. With valve in position, screw on the stud nuts
until all nuts are finger tight. An initial torque shall
be placed, in turn, on each stud nut. Increase
the torque progressively until the final torque is
applied. Upon completion, recheck each stud
nut’s torque. Required torque will vary with bolting
material and gaskets used. See your company
engineering or specification department for details
on torquing sequence and torque values. As an
extra precaution, the gap between the two mating
flanges should be checked during the torquing
process to ensure that the flanges are being
pulled together evenly. A final inspection and
review should be made to ensure that all of the
requirements for bolting the valve inlet have been
implemented.
4. The outlet piping may now be installed. A
complete inspection of components and their
cleanliness is to be made prior to further work.
Studs are to be lubricated with an appropriate
lubricant.
5. Install the outlet gasket, studs and nuts. Stud
nuts are to be pulled down finger tight. An initial
value of torque is to be applied. The additional
procedures outlined, in Step 3 should also be
followed.
After being assured that the valve is properly installed,
the drainage piping from the valve body-bowl is to be
connected. This line also must be flexible, so it will not
create stress on the valve under operating conditions.
Prior to completing the installation, a visual check
should be made to ensure that the valve lifting lever
has room and is free to operate.
At the time of installation, an inspection of the valve
should be made to confirm that all adjustment
components (i.e., ring pins, cap, etc.) are properly
locked and sealed, as required by the ASME Code.
For operational hydrostatic tests at the valve inlet, that
do not exceed valve set pressure, the valve should be
gagged. Refer to the final “Field Testing” portion of this
manual for proper techniques. Ensure that the gag is
removed upon completion of the inlet hydrostatic test.
Prior to startup of the unit on steam, the sections of
this manual that specify requirements for set pressure
testing should be reviewed. For conditions where the
valve is subjected to high steam pressures (i.e., those
exceeding normal operating conditions), preparations
should be made to gag the valves. These preparations
should then be cleared with the boiler manufacturer
and Baker Hughes. Refer to Section XIV. B.3 of this
manual for the proper gagging techniques.
The safety valve should be tested with full steam
pressure to ensure that the safety valve installation
has been properly accomplished. In some cases
this is not practical, thus the use of Consolidated
Hydroset
™
Test Device or
EVT
™
software, should be
considered. For valves being tested for set pressure
by using a Consolidated Hydroset Test Device or
EVT software, only the set pressure is being verified.
Other factors such as blowdown, lift, reaction force,
proper discharge stack sizes and effects of thermal
expansion cannot be determined, using these setting
devices. Full flow steam testing is recommended at
initial start-up to adjust blowdown and verify proper
XI. Recommended Installation Practices (Cont.)