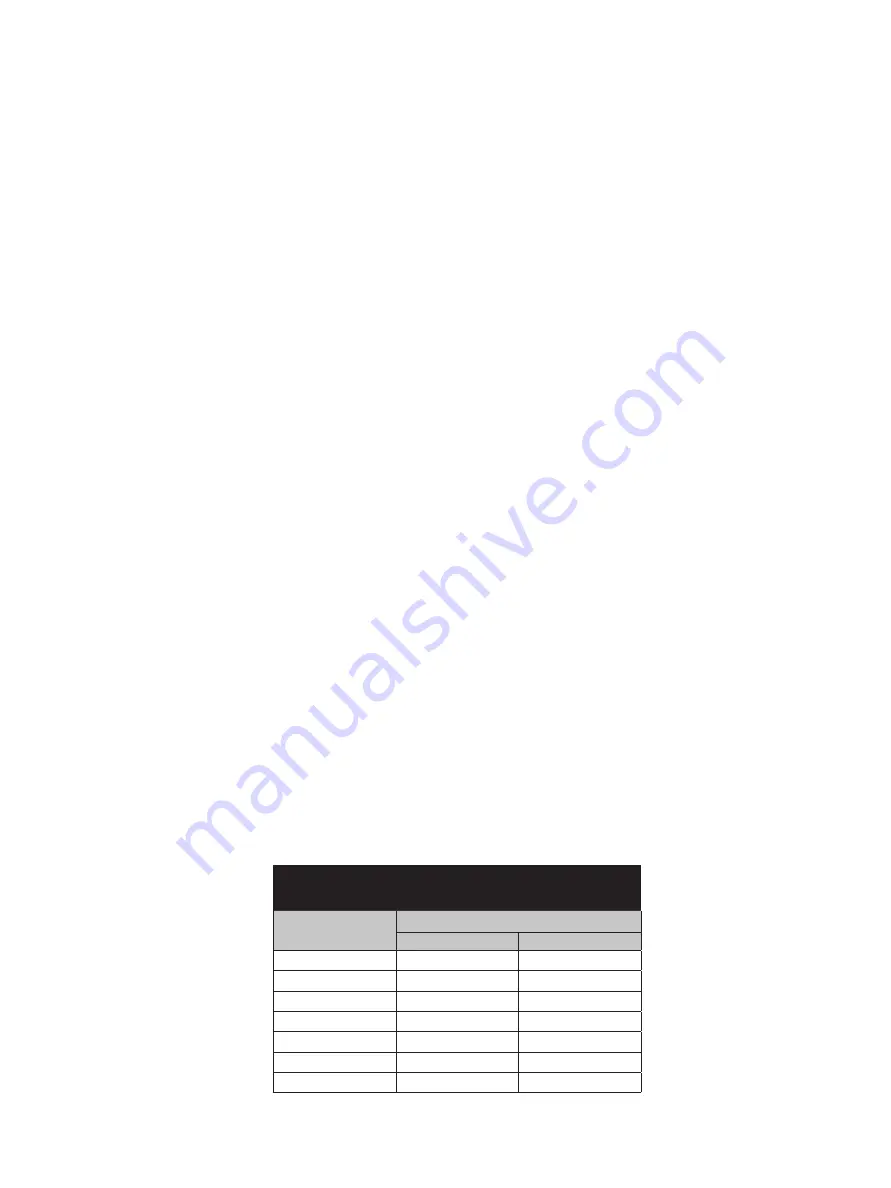
Consolidated 2700 Series Safety Valve Instruction Manual
| 23
© 2022 Baker Hughes Company. All rights reserved.
XIII. Inspection and Part Replacement (Cont.)
(ii) Lap, using an oscillating motion in various
directions, while holding the lap loosely in
the fingers and allowing the weight of the
lap to rest on the seat surface. Control the
motion of the lap to prevent either the inside
or outside edge of the lap from crossing the
bushing seat surface. If either edge touches
the seat surface, the seat can become
scratched and/or rounded.
Note:
Care should be used not to run off the
seating surface with the lap, as this will
cause the seat to become uneven.
(iii) Do not lap excessively with a ring lap
without resurfacing on a lapping plate.
Use a new ring lap, if further lapping is
required, to remove any defect in the seat.
To finish lapping the bushing seat, apply a
light coating of 1000-grit compound to the
face of the new lap and repeat the lapping
motion described previously.
(iv) Remove the ring lap and wipe the lap
surface with a clean, lint-free cloth, leaving
compound on the bushing seat. Replace
the ring lap on the seat and lap as above,
but without adding compound. Repeat this
operation until the seat has a mirror finish.
Any evidence of defects, such as gray
areas or scratches, will require a repeat of
the whole lapping procedure until a mirror
finish is attained.
(v) While the finer points of lapping and
“grinding-in” may be considered as a
mechanical art, it is not beyond the ability
of the average mechanic to produce good
seats with some practice. No effort has
been made in this manual to establish an
exact procedure to cover each and every
case, because different people can get the
same results using their own techniques.
(vi) The following precautions and hints will be
of assistance when lapping nozzle and/or
disc seats:
• Two (2) ring laps per valve
• 1A Clover Grinding Compound per
tool list
1
• 1000-grit Kwik-Ak-Shun Grinding
Compound per tool list
1
• Clean, lint free cotton rags
Note: This tool list is located on Section XV of
this manual.
d. Before lapping the nozzle and disc seat, the
leading edges (inside diameter of seats) of
both must be slightly chamfered as follows:
Use a fine-grade sandpaper to lightly break the
inner edge and outer edge of the nozzle seat
and disc seat. The purpose of this is to remove
any small metal particles or fins attached to the
sharp corner surfaces. Do not exceed .002”
(0.05 mm) chamfer for this purpose.
e. Seat bushing should be replaced if D
dimension is below the values mentioned in
Table 6.
Table 6: Seat Bushing Replacement Criteria
Orifice
D min.
in.
mm
#1
.125
3.18
#2
.203
5.16
#3
.250
6.35
#5
.313
7.95
#4
.313
7.95
#6
.500
12.70
#Q
.438
11.13