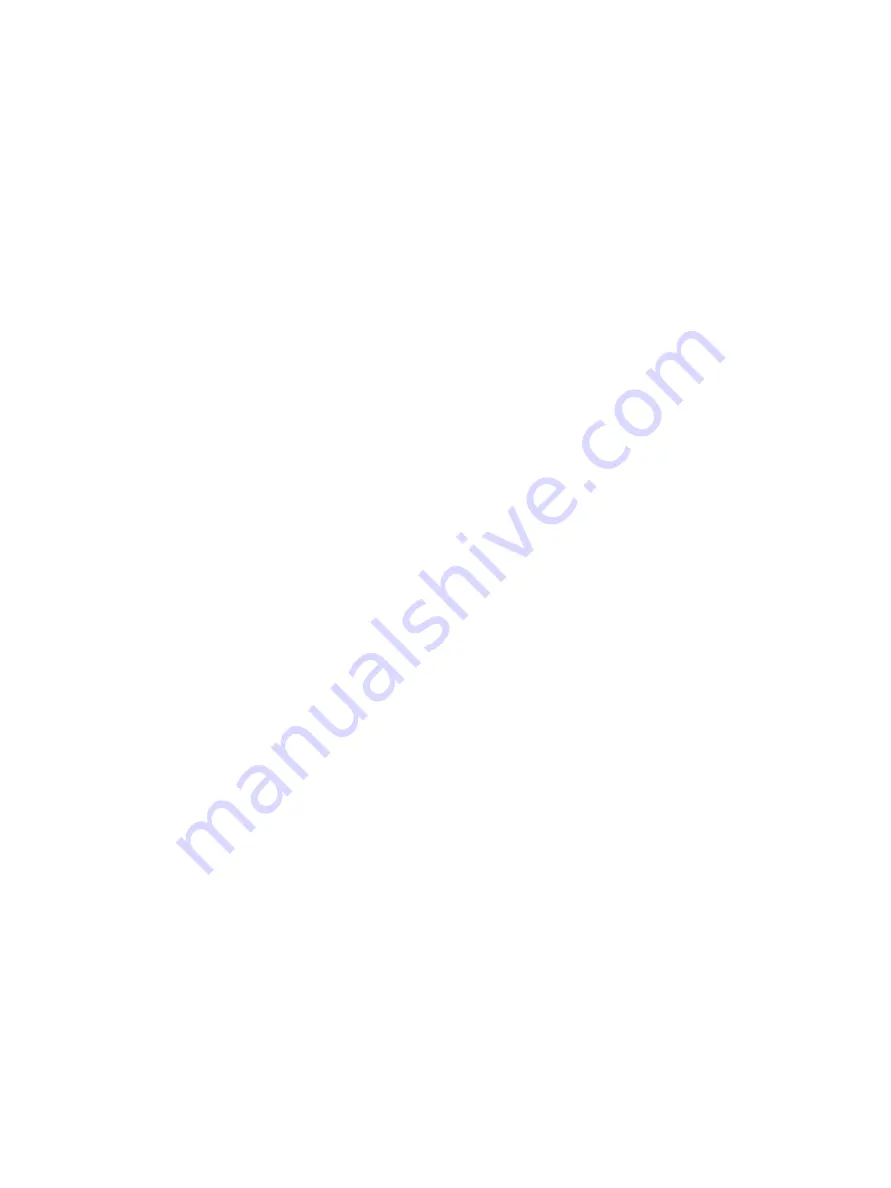
14 |
Baker Hughes
© 2022 Baker Hughes Company. All rights reserved.
For optimum performance, safety valves must be
serviced regularly and otherwise maintained. So that
servicing can be properly performed, valves should
be located in a manner that allows for easy access.
Sufficient working space should be provided around
and above the valve to permit access to adjusting
rings. If two or more valves are located close together,
the outlets should be parallel so as to offer as much
protection as possible to personnel repairing, or
working close to, the safety valve.
Because foreign material passing into and through,
a safety valve is damaging, the system on which
the valve is installed must also be inspected and
cleaned. New systems are prone to contain welding
beads, pipe scale, and other foreign materials that are
inadvertently trapped during construction, and they can
destroy the valve seating surfaces the first few times
the valve opens.
With regard to weld-end inlet valves, completely
assembled valves may be installed without
disassembly being necessary at the time of welding.
During welding, the valve neck should be insulated
to reduce thermal stresses. When stress relieving,
insulation should also be utilized to reduce thermal
stresses. In service, the valve neck should be
insulated at least to the point of the inlet neck/valve
body-bowl juncture.
Safety valves should be installed in a vertical position.
Nominal tolerance on vertical installation is plus or
minus 1 degree.
The discharge area of the outlet piping from a safety
valve should not be less than the area of the outlet
connection. Where more than one safety valve is
connected to a common outlet pipe, the area of the
pipe should not be less than the combined area of the
outlet connections to the safety valves.
All safety valve discharges should be piped so that
the effluent is discharged clear from walkways or
platforms. Ample provision for gravity drain should be
made in the discharge pipe at, or near, each safety
valve where water or condensation, may collect. Each
valve has an open gravity drain through the body,
below the level of the valve seat, and this drain should
be piped to a safe discharge area.
If a silencer is used on a safety valve, it should have
sufficient outlet area to prevent back pressure from
interfering with the proper operation and discharge
capacity of the valve. The silencer or other piping
components should be constructed so as to avoid the
possibility of creating corrosion deposit restrictions in
the steam passages.
Exhausts, drains, and vents must be installed so
that they will not impose undue stresses on the
safety valve. Any such stresses can produce body
distortion and leakage. Therefore, the following
recommendations are provided:
1. Discharge piping should not be supported by the
valve. The maximum weight on the outlet of the
valve should not exceed the weight of a flange
and short radius elbow, plus a 12-inch (304.8 mm)
straight length of standard weight thickness pipe
(with drip pan).
2. Clearance between the valve exhaust piping
and the discharge stack should be sufficient
to prevent contact when considering thermal
expansion of the header, valve, and discharge
stack. Movements due to vibration, temperature
changes, and valve reaction forces should also
be considered, to ensure adequate clearance
between the exhaust piping and the discharge
stack.
3. Flexible metal hoses are not generally
recommended, but if used to connect valve
outlets to discharge stacks, they must be of
sufficient length, and be configured/installed in
such a manner, that they will not become “solid”
in any one position. Better results are obtained
if the hoses are installed so that they will permit
movement by bending, rather than by stretching
and compressing along their length.
The yoke can be vented to the atmosphere as in
Figure 4 and 5. Precautions should be taken to vent
the yoke in such a manner that it will exhaust into a
safe area to prevent injury to personnel near the valve.
The yoke vent piping must not be connected to the
body drain piping.
Do not plug the yoke vent hole or reduce the vent hole
pipe size, (Reference Table 2), as this could lead to
valve malfunction and damage.
Precautions should be taken to prevent accumulations
of foreign material or water in the vent pipe. This vent
is a critical part of the valve system for controlling
valve blowdown and lift.
XI. Recommended Installation Practices (Cont.)