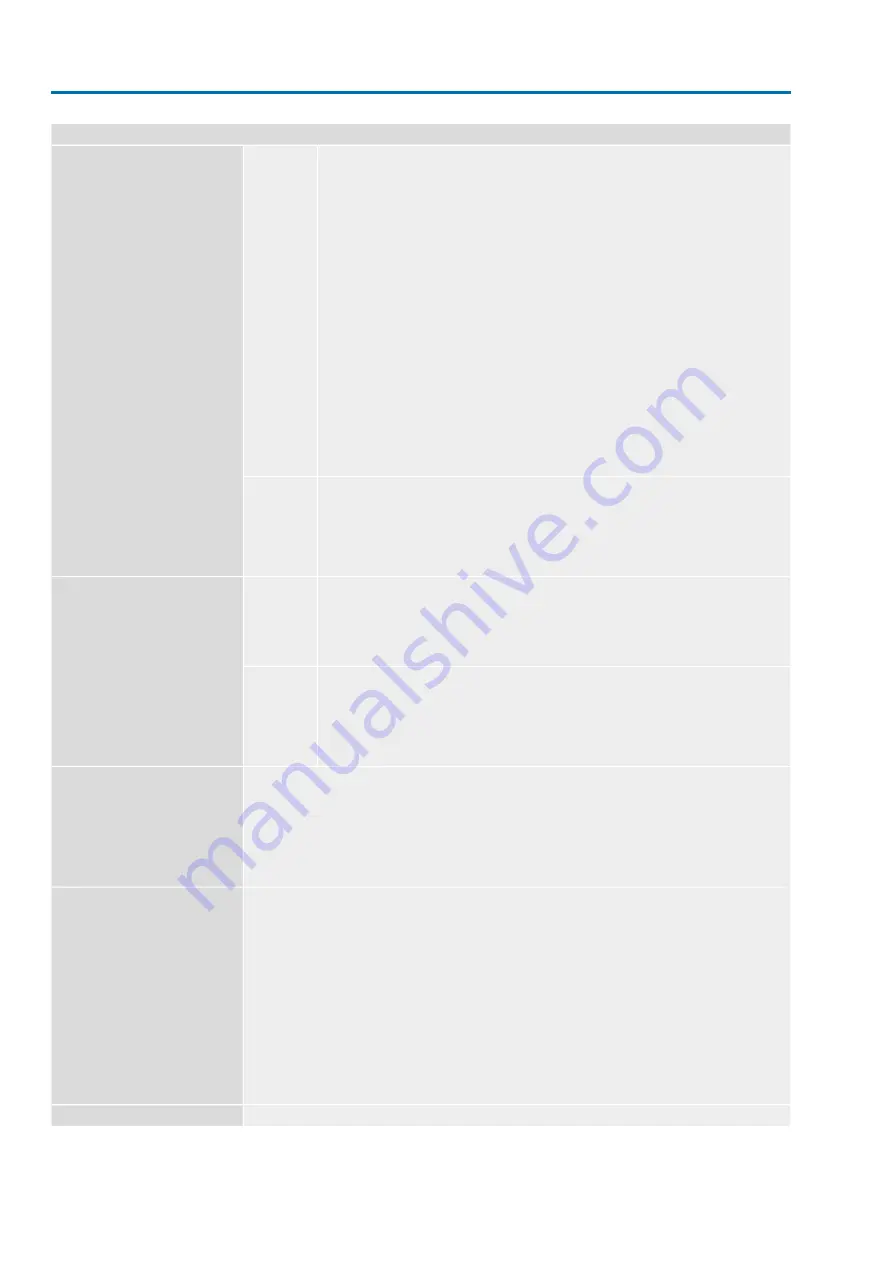
Features and functions
●
Selectable type of seating, limit or torque seating for end position OPEN and end po-
sition CLOSED
●
Torque by-pass: Adjustable duration (with adjustable peak torque during start-up time)
●
Start and end of stepping mode as well as ON and OFF times can be set individually
for directions OPEN and CLOSE, 1 to 1,800 seconds
●
Operation profile with any 8 intermediate positions: Position can be set between 0 and
100 %, reaction and signal behaviour programmable, positioning accuracy < 0.2 %,
individual speed between pivot points for OPEN and CLOSE respectively
●
Running indication blinking: can be set
●
Speed source can be selected (REMOTE, LOCAL)
●
4 internal nominal speeds can be programmed (and selected in LOCAL)
●
Nominal speed source can be selected for REMOTE (binary, analogue, fieldbus)
●
Soft start, soft stop (0.1 s – 10 s can be selected)
●
Synchronous link (synchronous operation of two actuators)
●
Positioner:
-
Position setpoint via fieldbus interface
-
Programmable behaviour on loss of signal
-
Automatic adaptation of dead band (adaptive behaviour selectable)
-
Change-over between OPEN-CLOSE control and setpoint control via fieldbus
-
Modulating duty with proportional operation (2 % – 20 %)
Standard:
Application functions
●
PID process controller: with adaptive positioner, via 0/4 – 20 mA analogue inputs for
process setpoint and actual process value
●
Automatic deblocking: Up to 5 operation trials, travel time in opposite direction can be
set
●
Static and dynamic torque recording for both rotation directions with torque measure-
ment flange as additional accessory
Options:
●
EMERGENCY operation (programmable behaviour)
-
Via additional input (option, low active) or via fieldbus interface
-
Reaction can be selected: STOP, run to end position (OPEN, CLOSED) or inter-
mediate position at defined speed
-
Torque monitoring can be by-passed during EMERGENCY operation
Standard:
Safety functions
●
Enabling local controls via Enable LOCAL digital input: Thus, actuator operation can
be enabled or disabled via push buttons on local controls.
●
Interlock for main/by-pass valve: Enabling the operation commands OPEN or CLOSE
via two digital inputs
●
PVST (Partial Valve Stroke Test): programmable to check the function of both actuator
and actuator controls: Direction, stroke, operation time, reversing time
Options:
●
Valve overload protection: adjustable, results in switching off and generates fault signal
●
Motor temperature monitoring (thermal monitoring): results in switching off and generates fault indic-
ation
●
Monitoring the heater within actuator: generates warning signal
●
Monitoring of permissible on-time and number of starts: adjustable, generates warning signal
●
Operation time monitoring: adjustable, generates warning signal
●
Phase failure monitoring: results in switching off and generates fault signal
Monitoring function
●
Electronic device ID with order and product data
●
Logging of operating data: A resettable counter and a lifetime counter each for:
-
Motor running time, number of starts, torque switch trippings in end position CLOSED, limit
switch trippings in end position CLOSED, torque switch trippings in end position OPEN, limit
switch trippings in end position OPEN, torque faults CLOSE, torque faults OPEN, motor protection
trippings
●
Time-stamped event report with history for setting, operation and faults:
-
Status signals according to NAMUR recommendation NE 107: "Failure", "Function check", "Out
of specification", "Maintenance required"
●
Torque characteristics (for version with MWG in actuator):
-
3 torque characteristics (torque-travel characteristic) for opening and closing directions can be
saved separately.
-
Torque characteristics stored can be shown on the display.
Diagnostic functions
PTC tripping device in combination with PTC thermistors within actuator motor
Motor protection evaluation
92
SAVEx 07.2 – SAVEx 16.2 / SARVEx 07.2 – SARVEx 16.2 Control unit: electronic (MWG)
Technical data
ACVExC 01.2 Non-Intrusive Modbus RTU