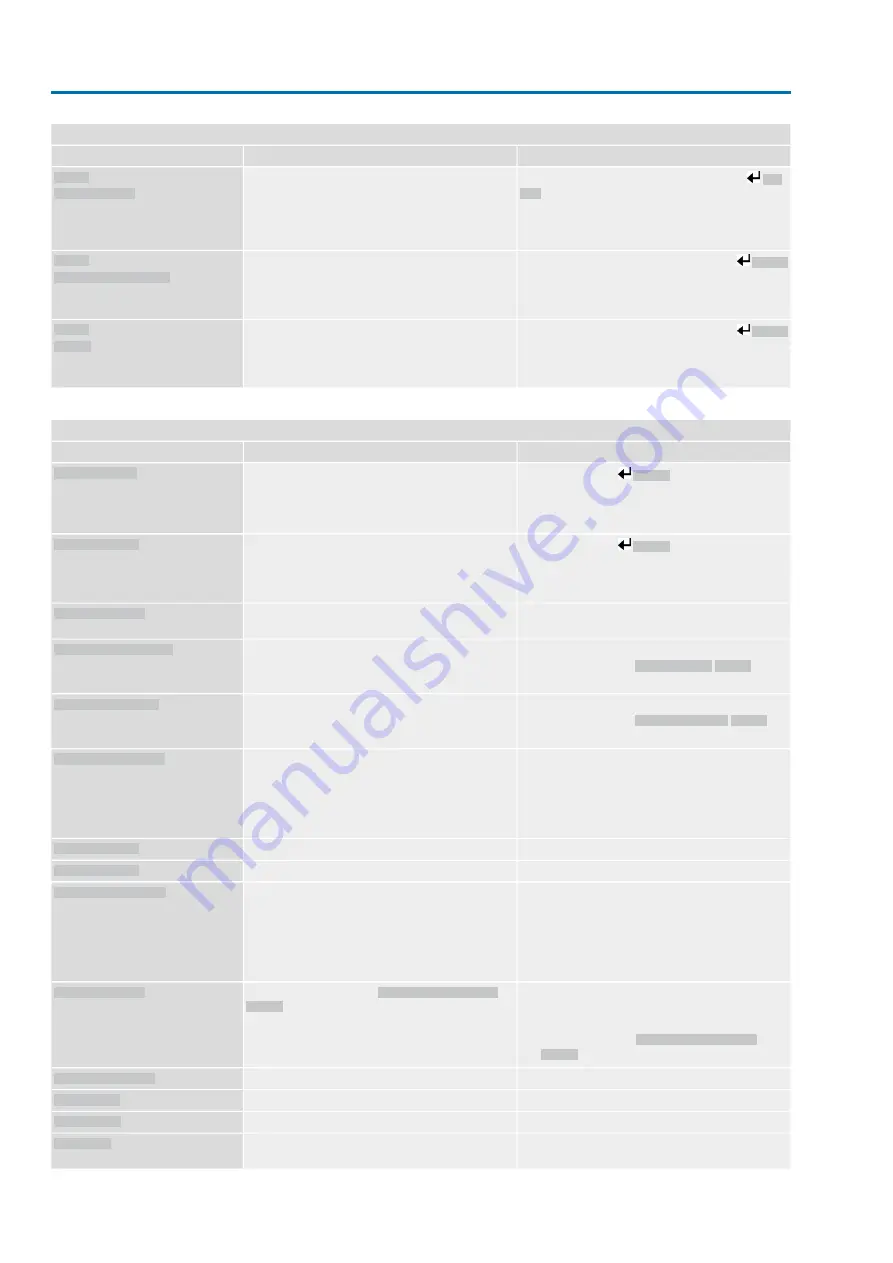
Faults and warnings via status indications in the display
Remedy
Description/cause
Indication on display
For indicated value > 0: Press push button
De-
tails
.
For details, refer to <Not ready REMOTE and
Function check> table.
Collective signal 08:
Indication according to NAMUR recommendation
NE 107
The actuator is being worked on; output signals are
temporarily invalid.
S0009
Function check
For indicated value > 0: Press push button
Details
to display a list of detailed indications.
Collective signal 09:
Indication according to NAMUR recommendation
NE 107
Recommendation to perform maintenance.
S0010
Maintenance required
For indicated value > 0: Press push button
Details
to display a list of detailed indications.
For details, refer to <Faults and Failure> table.
Collective signal 10:
Indication according to NAMUR recommendation
NE 107
Actuator function failure, output signals are invalid
S0011
Failure
Table 27:
Warnings and Out of specification
Remedy
Description/cause
Indication on display
Press push button
Details
to display a list of indi-
vidual indications.
For a description of the individual signals, refer to
Manual (Operation and setting).
Collective signal 06:
Possible cause:
Configuration setting is incorrect.
The device can still be operated with restrictions.
Config. warning
Press push button
Details
to display a list of indi-
vidual indications.
For a description of the individual signals, refer to
Manual (Operation and setting).
Collective signal 15:
Device warnings
The device can still be operated with restrictions.
Internal warning
Check 24 V DC voltage supply.
The external 24 V DC voltage supply of the controls
has exceeded the power supply limits.
24 V DC external
●
Check modulating behaviour of actuator.
●
Check parameter
Perm. run time M0356
, re-set
if required.
Warning on time max. running time/h exceeded
Wrn op.mode run time
●
Check modulating behaviour of actuator.
●
Check parameter
Permissible starts M0357
, re-
set if required.
Warning on time max. number of motor starts
(starts) exceeded
Wrn op.mode starts
Verify signals:
●
Setpoint E1
●
Actual value E2
●
Actual process value E4
●
Check connection to master.
The failure behaviour is active since all required
setpoints and actual values are incorrect.
Failure behav. active
Check wiring.
Warning: Loss of signal analogue input 1
Wrn input AIN 1
Check wiring.
Warning: Loss of signal analogue input 2
Wrn input AIN 2
Check setpoint signal.
Warning: Loss of signal setpoint position
Possible causes:
For an adjusted setpoint range of e.g. 4 – 20 mA,
the input signal is 0 (signal loss).
For a setpoint range of 0 – 20 mA , monitoring is
not possible.
Wrn setpoint position
The warning indications are automatically cleared
once a new operation command is executed.
●
Check valve.
●
Check parameter
Perm.op. time, manual
M0570
.
The set time (parameter
Perm.op. time, manual
M0570
) has been exceeded. The preset operating
time is exceeded for a complete travel from end
position OPEN to end position CLOSED.
Op. time warning
Measure/reduce ambient temperature.
Temperature within controls housing too high.
Wrn controls temp.
Set time.
Real time clock has not yet been set.
Time not set
Replace button cell.
Voltage of the RTC button cell is too low.
RTC voltage
Check actuator (PVST settings).
Partial Valve Stroke Test (PVST) could not be suc-
cessfully completed.
PVST fault
78
SAVEx 07.2 – SAVEx 16.2 / SARVEx 07.2 – SARVEx 16.2 Control unit: electronic (MWG)
Corrective action
ACVExC 01.2 Non-Intrusive Modbus RTU