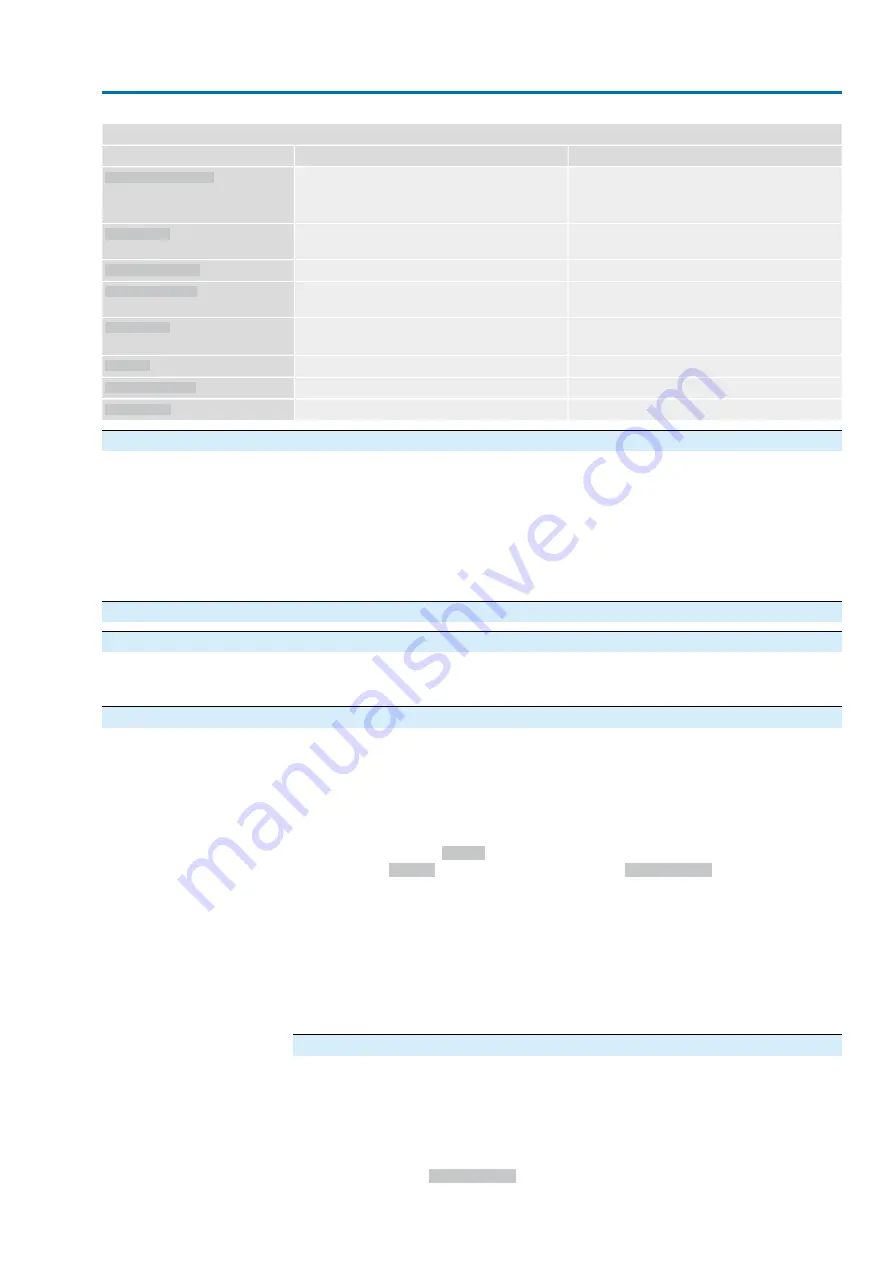
Not ready REMOTE and Function check (collective signal 04)
Remedy
Description/cause
Indication on display
●
Detect cause for EMERGENCY signal.
●
Verify failure source.
●
Apply +24 V DC at EMERGENCY input.
Operation mode EMERGENCY is active (EMER-
GENCY signal was sent).
0 V are applied at the EMERGENCY input.
EMCY behav. active
Check I/O interface.
The actuator is controlled via the I/O interface (par-
allel).
I/O interface
Start motor operation.
Manual operation is activated.
Handwheel active
Verify master configuration
Fieldbus connection available, however no process
data transmission by the master.
FailState fieldbus
Release push button STOP.
A local STOP is active.
Push button STOP of local controls is operated.
Local STOP
Check interlock signal.
An interlock is active.
Interlock
Check states of main and by-pass valve.
By-pass function is interlocked.
Interlock by-pass
Wait until PVST function is complete.
Partial Valve Stroke Test (PVST) is active.
PVST active
11.2.1.
Signal "Motor protection tripped” (via TMS device)
The “Motor protection tripped” signal (wiring diagram designation:
TMS-M
) must be
monitored:
“Motor protection tripped” = contact NC open (contact NO = closed)
If the heating system is integrated within actuator controls (wiring diagram designation:
R5 H
), check the function of the heating system with the “Motor protection tripped”
signal (
TMS-M
). For temperatures significantly exceeding –30 °C: Switch off the
power supply of the heating system!
11.3.
Fuses
11.3.1.
Fuses within the actuator controls
F5
Automatic reset fuse as short-circuit protection for external 24 V DC supply for
customer (refer to wiring diagram)
11.3.2.
Motor protection (thermal monitoring)
In order to protect against overheating and impermissibly high surface temperatures
at the actuator, PTC thermistors are embedded in the motor winding. Motor protection
trips as soon as the max. permissible winding temperature has been reached.
The actuator is switched off and the following signals are given:
●
LED 3 (motor protection trippped) on the local controls is illuminated.
●
Status indication
S0007
displays a fault.
The fault
Details
is displayed when selecting
Thermal fault
.
The motor has to cool down before operation can be resumed.
Depending on the parameter setting (motor protection behaviour), the fault signal is
either automatically reset or the fault signal has to be acknowledged.
The acknowledgement is made:
●
in selector switch position Local control (LOCAL) via push button RESET.
●
In selector switch position Remote control (REMOTE) with Reset command
via fieldbus.
Proof-test motor protection
Test correct functioning of the motor protection as described hereafter. Perform the
functional test at the latest within the framework of maintenance (refer to chapter
<Servicing and maintenance>).
The test is performed by simulating the motor protection signal via actuator controls
local controls:
Required user level:
Specialist (4)
or higher.
81
SAVEx 07.2 – SAVEx 16.2 / SARVEx 07.2 – SARVEx 16.2 Control unit: electronic (MWG)
ACVExC 01.2 Non-Intrusive Modbus RTU
Corrective action