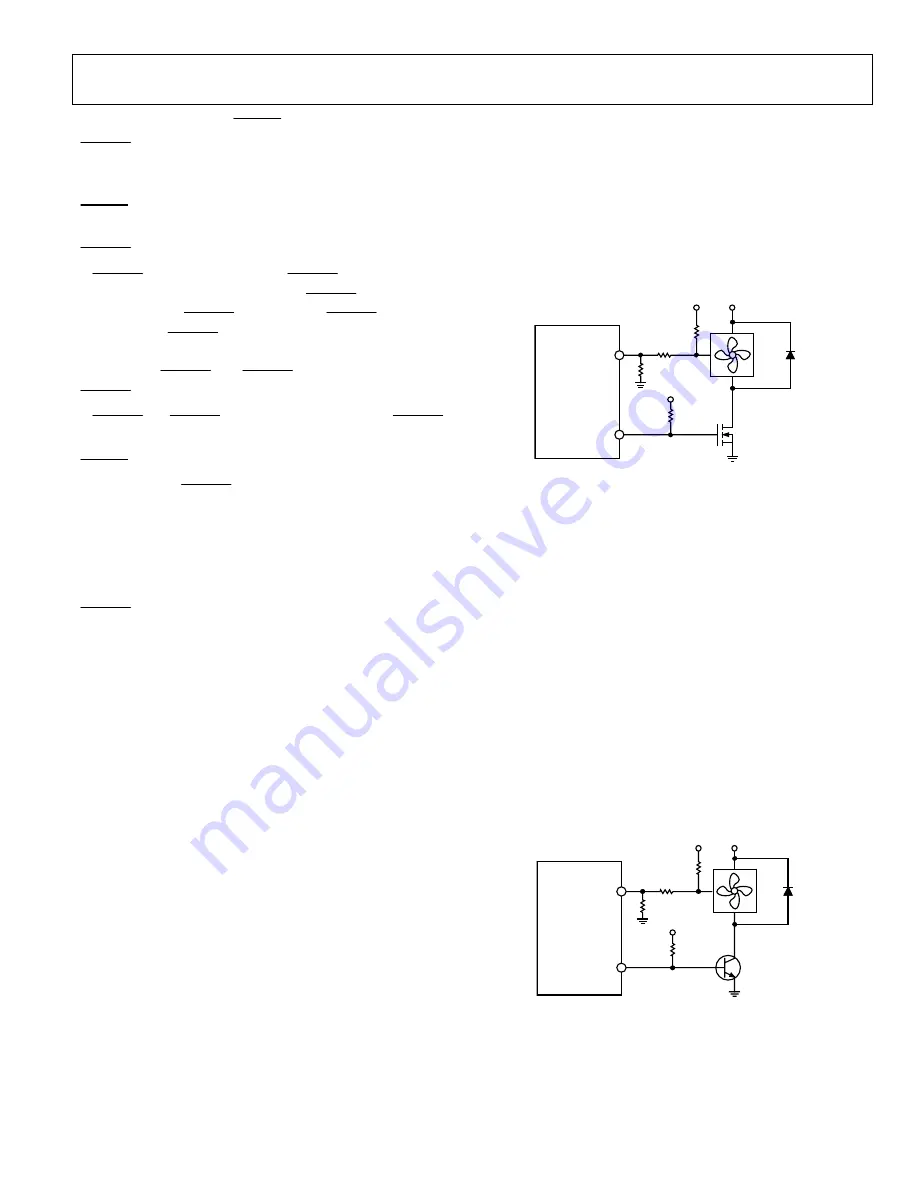
ADT7476
Rev. B | Page 31 of 72
Enabling and Disabling THERM on Individual Channels
THERM can be enabled/disabled for individual or combina-
tions of temperature channels using Bits [7:5] of Configuration
Register 5 (0x7C).
THERM Hysteresis
Setting Bit 0 of Configuration Register 7 (0x11) disables
THERM hysteresis.
If THERM hysteresis is enabled and THERM is disabled (Bit 2
of Configuration Register 4, 0x7D), the THERM pin does not
assert low when a THERM event occurs. If THERM hysteresis
is disabled and THERM is disabled (Bit 2 of Configuration
Register 4, 0x7D) and assuming that the appropriate pin is
configured as THERM), the THERM pin asserts low when a
THERM event occurs.
If THERM and THERM hysteresis are both enabled, the THERM
output asserts as expected.
THERM Operation in Manual Mode
In manual mode, THERM events do not cause fans to go to full
speed, unless Bit 3 of Configuration Register 6 (0x10) is set to 1.
Additionally, Bit 3 of Configuration Register 4 (0x7D) can be
used to select PWM speed on a THERM event (100% or maxi-
mum PWM).
Bit 2 in Configuration Register 4 (0x7D) can be set to disable
THERM events from affecting the fans.
FAN DRIVE USING PWM CONTROL
The ADT7476 uses pulse-width modulation (PWM) to control
fan speed. This relies on varying the duty cycle (or on/off ratio)
of a square wave applied to the fan to vary the fan speed. The
external circuitry required to drive a fan using PWM control is
extremely simple. For 4-wire fans, the PWM drive might need
only a pull-up resistor. In many cases, the 4-wire fan PWM
input has a built-in pull-up resistor.
The ADT7476 PWM frequency can be set to a selection of low
frequencies or a single high PWM frequency. The low frequency
options are used for 3-wire fans, while the high frequency option
is usually used with 4-wire fans.
For 3-wire fans, a single N-channel MOSFET is the only drive
device required. The specifications of the MOSFET depend on
the maximum current required by the fan being driven and the
input capacitance of the FET. Because a 10 kΩ (or greater) resis-
tor must be used as a PWM pull-up, an FET with large input
capacitance can cause the PWM output to become distorted
and adversely affect the fan control range. This is a requirement
only when using high frequency PWM mode.
Typical notebook fans draw a nominal 170 mA, so SOT devices
can be used where board space is a concern. In desktops, fans
typically draw 250 mA to 300 mA each. If several fans are
driven in parallel from a single PWM output or drive larger
server fans, the MOSFET must handle the higher current
requirements. The only other stipulation is that the MOSFET
should have a gate voltage drive, V
GS
< 3.3 V, for direct inter-
facing to the PWM output pin. The MOSFET should also have a
low on resistance to ensure that there is not a significant voltage
drop across the FET, which would reduce the voltage applied
across the fan and, therefore, the maximum operating speed of
the fan.
Figure 35 shows how to drive a 3-wire fan using PWM control.
05
38
2-
03
6
ADT7476
TACH
PWM
12V
FAN
Q1
NDT3055L
TACH
3.3V
12V
12V
10k
Ω
4.7k
Ω
10k
Ω
10k
Ω
1N4148
Figure 35. Driving a 3-Wire Fan Using an N-Channel MOSFET
Figure 35 uses a 10 kΩ pull-up resistor for the TACH signal.
This assumes that the TACH signal is an open-collector from
the fan. In all cases, the TACH signal from the fan must be kept
below 3.6 V maximum to prevent damage to the ADT7476.
Figure 36 shows a fan drive circuit using an NPN transistor
such as a general-purpose MMBT2222. While these devices are
inexpensive, they tend to have much lower current handling
capabilities and higher on resistance than MOSFETs. When
choosing a transistor, care should be taken to ensure that it
meets the fan’s current requirements. Ensure that the base
resistor is chosen so that the transistor is saturated when the fan
is powered on.
Because in 4-wire fans the fan drive circuitry is not switched on
or off, as with previous PWM driven/powered fans, the internal
drive circuit is always on and uses the PWM input as a signal
instead of a power supply. This enables the internal fan drive
circuit to perform better than 3-wire fans, especially for high
frequency applications.
0
538
2-
0
37
ADT7476
TACH
TACH
PWM
12V
FAN
Q1
MMBT2222
3.3V
12V
12V
470
Ω
4.7k
Ω
10k
Ω
10k
Ω
1N4148
Figure 36. Driving a 3-Wire Fan Using an NPN Transistor
www.BDTIC.com/ADI