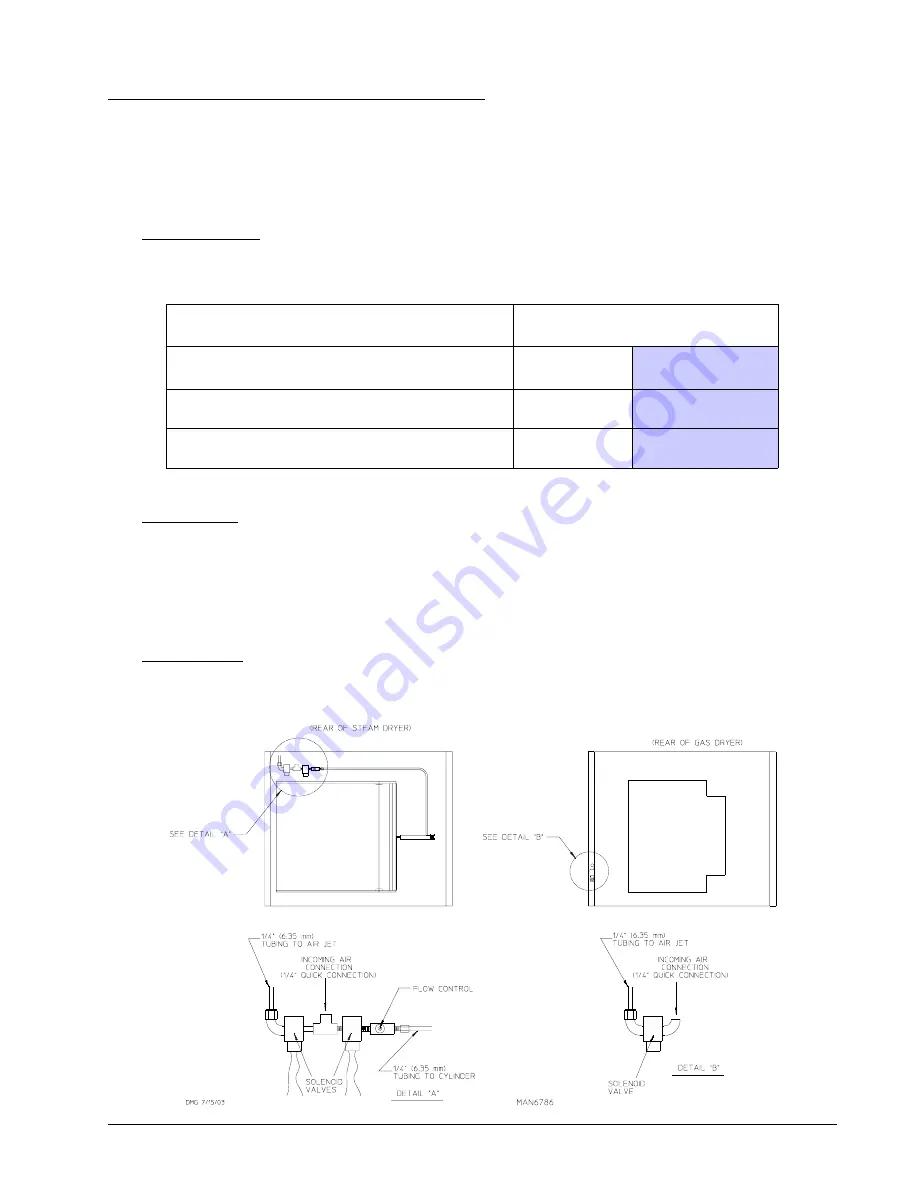
113406-1
www.amdry.com
31
K. COMPRESSED AIR REQUIREMENTS
The dryer requires an external supply of compressed air (2.5 cfh @ 80 psi [0.07 cmh @ 5.51 bar] for gas models
and 3.25 cfh @ 80 psi [0.09 cmh @ 5.51 bar] for steam models). For steam models, compressed air is necessary
for the air operated steam damper. On both the steam models as well as the gas models, compressed air is
necessary/required for blower air jet operation to clean lint from the impellor/fan (squirrel cage).
1. Air Requirements
Microprocessor Controller (Computer) Dryers:
Shaded areas are stated in metric equivalents
2. Air Regulation
No air regulation or air filtration is provided with the dryer. External regulation/filtration of 80 psi (5.51 bar)
must be
provided. It is suggested that a regulator/filter gauge arrangement be added to the compressed air
line just before the dryer connection. This is necessary to ensure that correct and clean air pressure is
achieved.
3. Air Connection
Air connection to this system is a 1/4” as per the
illustration below
.
Compressed Air Supply
Air Pressure
Normal
80 psi
5.51 bar
Minimum Supply
70 psi
4.82 bar
Maximum Supply
90 psi
6.20 bar
Содержание ML-175
Страница 54: ...ADC113406 1 01 07 05 3 ...