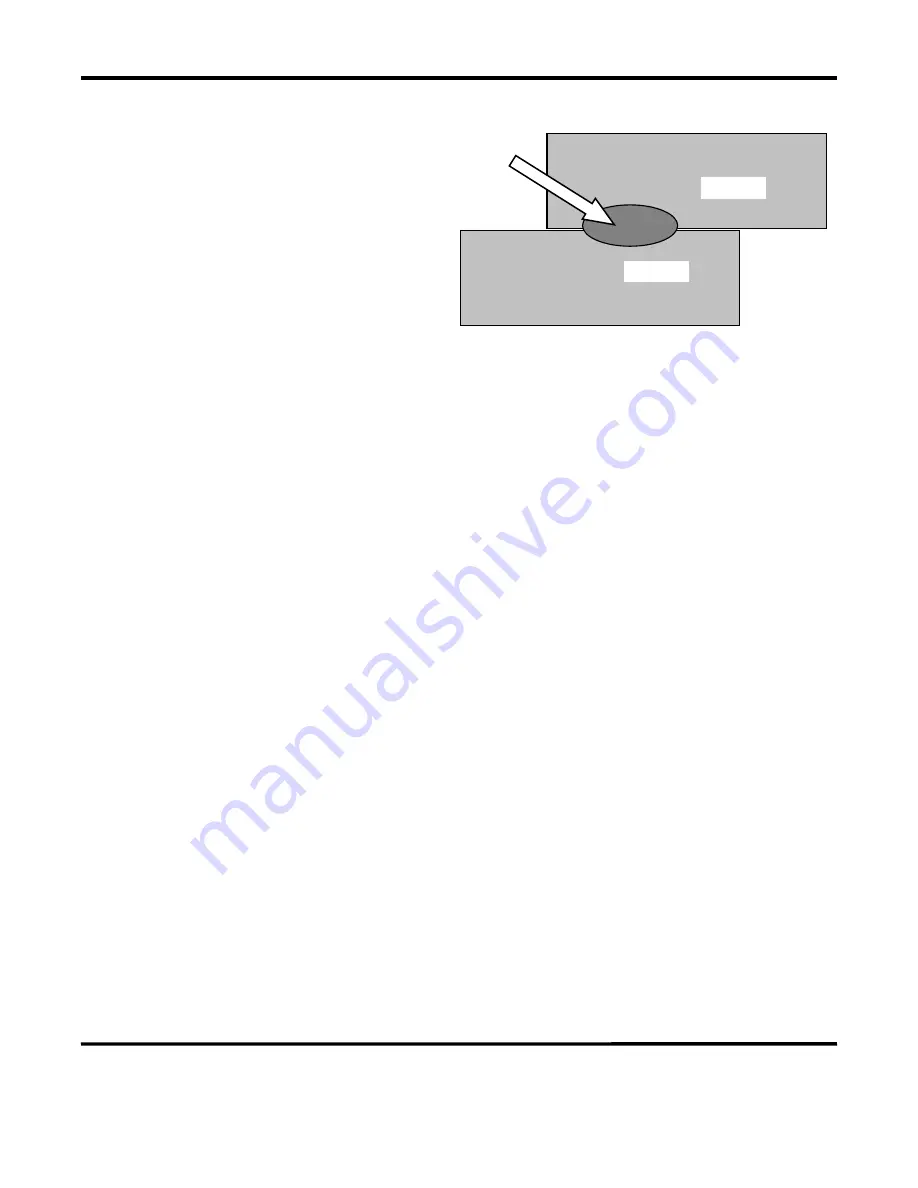
APPENDIX F: DEFINING THE OPTIMUM PROCESS
CD-A DUAL PULSE RESISTANCE WELDING POWER SUPPLY
F-2
990-430
Alloys are a mixture of two or more metals. An
alloy is normally harder, less conductive, and
more brittle than the parent metal which has
bearing on the type of joint one can expect when
resistance welding a combination of different
metals.
Metals atoms are naturally attracted to other metal
atoms even in different parent materials. Metals
and alloys will bond together once surface
contaminants such as dirt, grease, and oxides
removed. Resistance welding generates heat at
the material interface, which decomposes the dirt and grease and helps to break up the oxide film. The
resultant heat softens or melts the metal and the applied force brings the atoms on either side into close
contact to form the bond. The strength of the joint develops as it cools and a new structure is formed.
There are three main types of bonds that can be formed using the resistance welding process:
•
Solder or Braze Joint
A filler material such as a solder or braze compound is either added during the process or present
as a plating or coating. Soldered joints are typically achieved at temperatures less than 400°C
and brazed joints such as Sil-Phos materials melt at temperatures above 400°C.
•
Solid-State Joint
A solid state joint can be formed when the materials are heated to between 70-80% of their
melting point.
•
Fusion Joint
A fusion joint can be formed when both metals are heated to their melting point and their atoms
mix.
Many micro-resistance welding challenges involve joining dissimilar metals in terms of their melting
points, electrical conductivity, and hardness. A solid-state joint can be an ideal solution for these difficult
applications; there is no direct mixing of the two materials across the weld interface thus preventing the
formation of harmful alloys that could form brittle compounds that are easily fractured. Remember that
in a solid-state joint, the metals are only heated to 70-80% of their respective melting points, resulting in
less thermal stress during heating and subsequent joint cooling in comparison to a fusion weld. As there
is no real melting of the materials in a solid-state joint, there is less chance of weld splash or material
expulsion. A weld nugget can still be achieved with a solid-state joint.
Metal B
Metal A
Alloy
Содержание CD-A Series
Страница 1: ...990 430 Rev C STORED ENERGY POWER SUPPLY CD A OPERATION MANUAL ...
Страница 46: ......
Страница 60: ......
Страница 74: ......
Страница 78: ......
Страница 88: ......
Страница 108: ...AMADA WELD TECH INC 1820 South Myrtle Ave Monrovia CA 91016 U S A TEL 1 626 303 5676 FAX 1 626 358 8048 ...