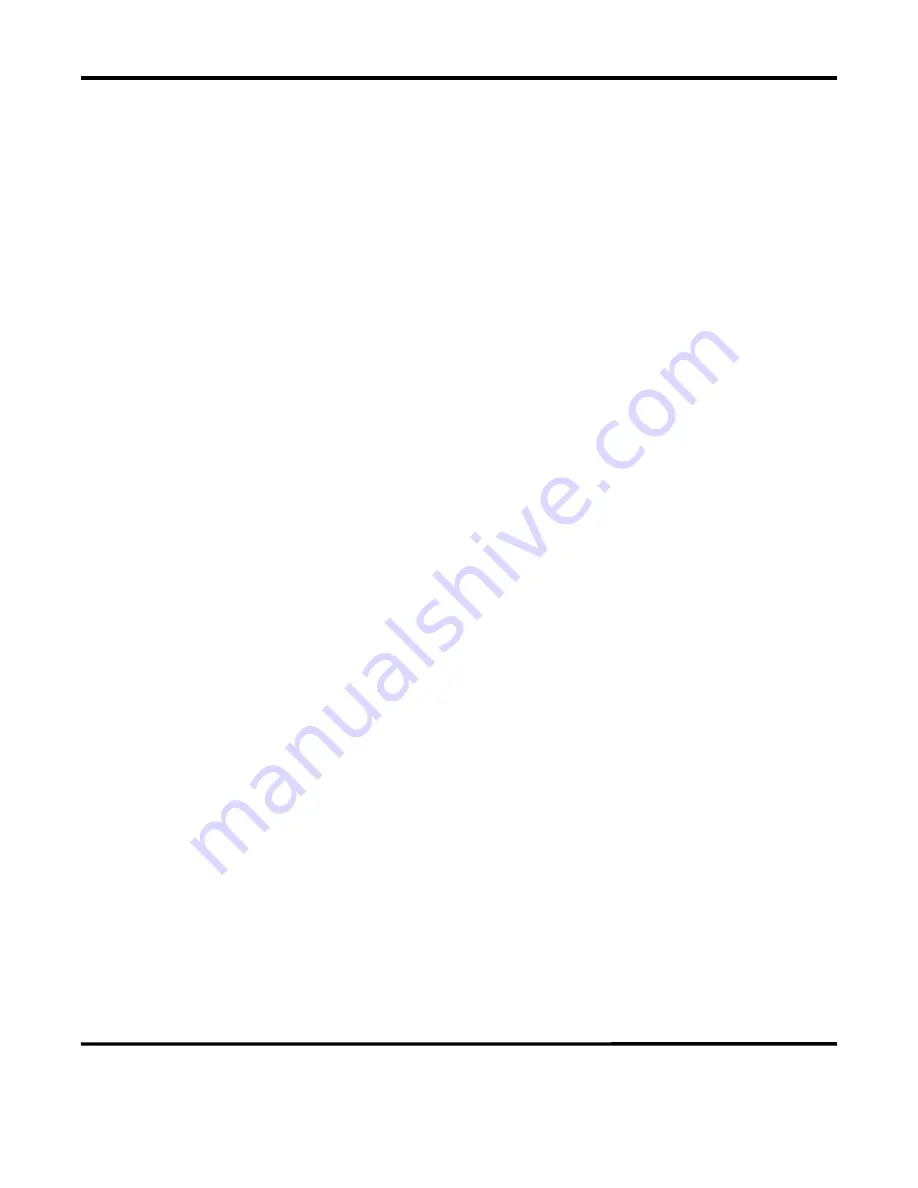
APPENDIX E: THE BASICS OF RESISTANCE WELDING
CD-A DUAL PULSE RESISTANCE WELDING POWER SUPPLY
990-430
E-5
Weld Schedule Development
Developing a weld schedule is a methodical procedure, which consists of making sample welds and
evaluating the results. The first weld should be made at low energy settings. Adjustments are then made
to each of the welding parameters
one at a time
until a successful weld is made.
1
Install the correct electrodes in the electrode holders on the Weld Head. See the preceding Table
for electrode material recommendations.
2
Use a flat electrode face for most applications. Use a "domed" face if surface oxides are a
problem. If either of the parts is a wire, the diameter of the electrode face should be equal to or
greater than the diameter of the wire. If both parts are flat, the face should be at least one-half
the diameter of the electrodes. Pencil point electrodes cause severe electrode sticking to the parts,
unexplained explosions, and increase the weld heat substantially because of the reduced
electrode-to-part contact area.
3
Use the Force Adjustment Knob on the Weld Head to set the Firing Force and adjust an Air
Actuated Weld Head
.
4
Program a weld schedule, then make your first weld. Always observe safety precautions when
welding and wear safety glasses. For a complete procedure on making welds, refer to
Operating
Instructions
.
5
Use pliers to peel the welded materials apart. A satisfactory weld will show residual material
pulled from one material to the other. Tearing of base material around the weld nugget indicates
a material failure NOT a weld failure. Excessive electrode sticking and/or "spitting" should
define a weld as unsatisfactory and indicates that too much weld current, voltage, power, or time
has been used.
6
If the parts pull apart easily or there is little or no residual material pulled, the weld is weak.
Increase the weld time in 1ms increments. Increase weld current, voltage, or power if a
satisfactory weld achieved using 10ms of weld time.
NOTE
:
Actual weld strength is a user-defined specification.
7
Polarity, as determined by the direction of weld current flow, can have a marked effect on the
weld characteristics of some material combinations. This effect occurs when welding materials
with large differences in resistivity, such as copper and nickel or when welding identical
materials with thickness ratios greater than 4 to 1. The general rule is that the more resistive
material or the thinner material should be placed against the negative (-) electrode. Polarity on
the Control can be changed by either changing the setting in the Edit mode on the RUN screen
(See polarity select in chapter 1) or by reversing the Weld Cables.
Weld Strength Testing
Destructive tests should be performed on a random basis using actual manufacturing parts. Destructive
tests made on spot welds include tension, tension-shear, peel, impact, twist, hardness, and macro-etch
tests. Fatigue tests and radiography have also been used. Of these methods torsional shear is preferred
for round wire and a 45-degree peel test for sheet stock.
Содержание CD-A Series
Страница 1: ...990 430 Rev C STORED ENERGY POWER SUPPLY CD A OPERATION MANUAL ...
Страница 46: ......
Страница 60: ......
Страница 74: ......
Страница 78: ......
Страница 88: ......
Страница 108: ...AMADA WELD TECH INC 1820 South Myrtle Ave Monrovia CA 91016 U S A TEL 1 626 303 5676 FAX 1 626 358 8048 ...