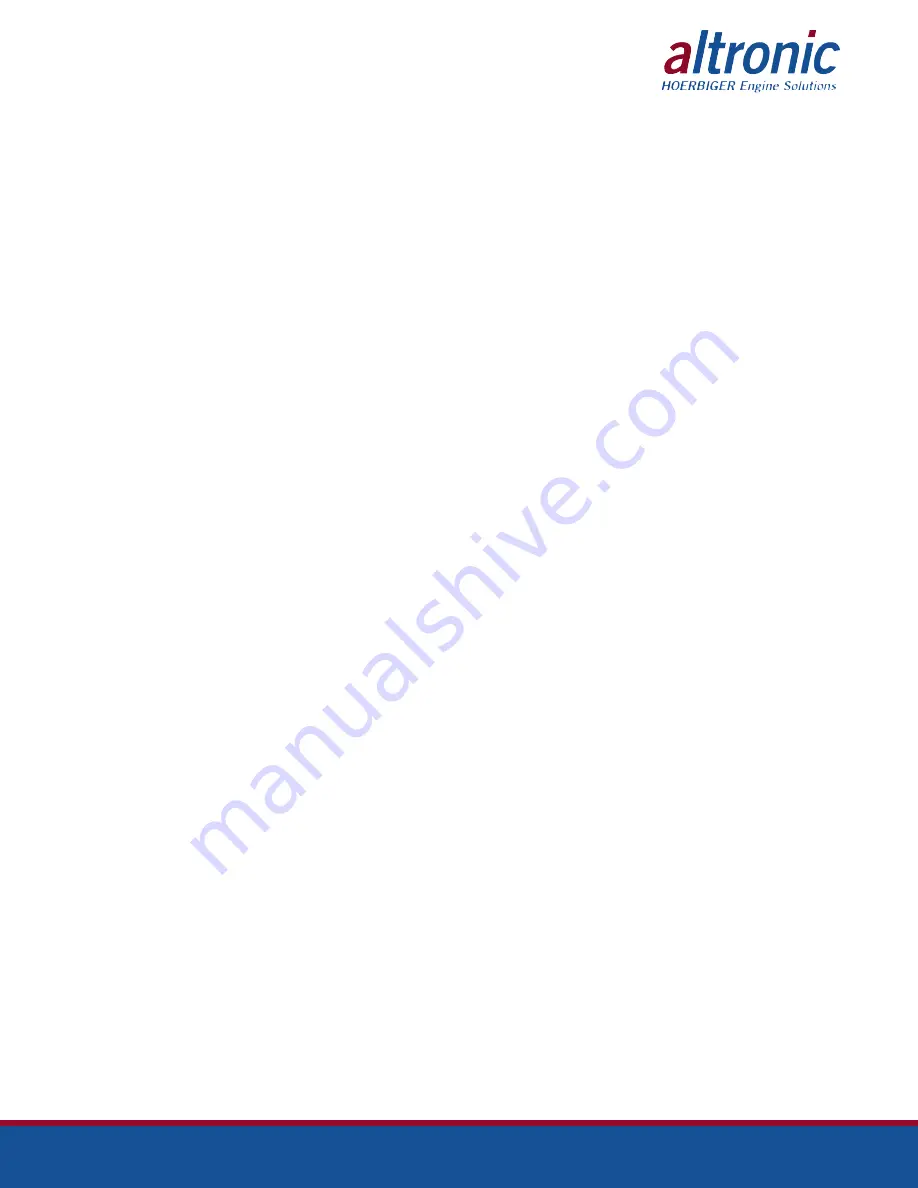
DE-3000+ IOI 8-15
All rights reserved © ALTRONIC, LLC 2015
66
GLOSSARY:
ACTUATOR
Electromagnetic devices which convert electric current
to linear or rotary motion. This motion may then be used
to control equipment directly, an electromechanical ac-
tuator, or it can be used to regulate a gas or liquid pres-
sure as in a current to pressure converter (I/P).
ANALOG INPUT
An input which accepts voltage signals between 0 and 5
volts. These signals are converted by the DE-3000+ to
engineering units and compared by the microprocessor
to user programmed safety shutdown and control set-
points.
ANALOG OUTPUT
An output which provides a current between 4-20mA to
external devices to control the compressor. These outputs
can be used to interface directly to electrical actuators or
connected to I/P transducers mechanical actuators.
CAPACITY CONTROL
The capacity control of the compressor is accomplished
by reducing the volume of gas moved per compressor
cycle. 100% capacity is the full rated volume of gas com-
pressed per machine cycle. Capacity control can be done
on both reciprocating and screw compressors using vari-
ous techniques.
COMPRESSOR CYCLE
A compressor cycle is a full rotation of the compressor drive
shaft. A turn of the screw on a screw compressor or a revo-
lution of the crankshaft on a reciprocating compressor.
CONTROL SETPOINTS
These are setpoints programmed by the user which are
within the normal operating range of the equipment and
are used to optimize the function of the equipment. Con-
trol setpoints may also be used to implement corrective
actions to prevent overstress of components or to notify
personnel of potential problems before they become se-
vere enough to cause a shutdown.
CRANK DISCONNECT
The RPM setting at which output #3 of the power supply will
be de-energized. This will de-energize the starting device.
CRANKING DELAY
The time after the auto start command before cranking
will begin. Allows for pre-lube function and starting warn-
ing to personnel. Power supply output #4 is normally en-
ergized during this time. See PRE-LUBE TIME.
CURRENT STEP LIMIT
The current step limit is a maximum value that the ana-
log output will be allowed to change from one control
cycle to another. The current step limit is used to prevent
rapid or erratic control action of the actuator even under
transient conditions or with a poorly tuned control sys-
tem. A limit of about 2mA or about 10% of the output
range is reasonable default value.
CYCLE TIME
The time taken between adjustments of the PRIMARY
CONTROL loop. The longer the cycle time selected the
less responsive the control output is to variations in the
controlled parameter. The cycle time is adjustable from
1 to 999 seconds.
DEADBAND
The controller deadband defines a user programmed value
both above and below the setpoint for which no corrective
action will be taken. Deadband is used to improve control
stability by holding the controller output constant in the
presence of “noise” or small transient errors on the input.
DIRECT ACTING
When describing control or actuator functions, direct acting
is used to identify relationships where the controller must
increase its output to cause an increase in the variable.
Содержание DE-3000+ Series
Страница 71: ...DE 3000 IOI 8 15 All rights reserved ALTRONIC LLC 2015 71 FIG 2 DE 3000 SYSTEM DIAGRAM DE 3000 ...
Страница 74: ...DE 3000 IOI 8 15 All rights reserved ALTRONIC LLC 2015 74 FIG 5 WIRING DIAGRAM PERSONAL COMPUTER ...
Страница 75: ...DE 3000 IOI 8 15 All rights reserved ALTRONIC LLC 2015 75 FIG 6 WIRING DIAGRAM SENSOR AND TRANSDUCER INPUTS ...
Страница 76: ...DE 3000 IOI 8 15 All rights reserved ALTRONIC LLC 2015 76 FIG 7 WIRING DIAGRAM CURRENT LOOP OUTPUTS ...
Страница 77: ...DE 3000 IOI 8 15 All rights reserved ALTRONIC LLC 2015 77 FIG 8 WIRING DIAGRAM DIGITAL OUTPUT SWITCHES ...