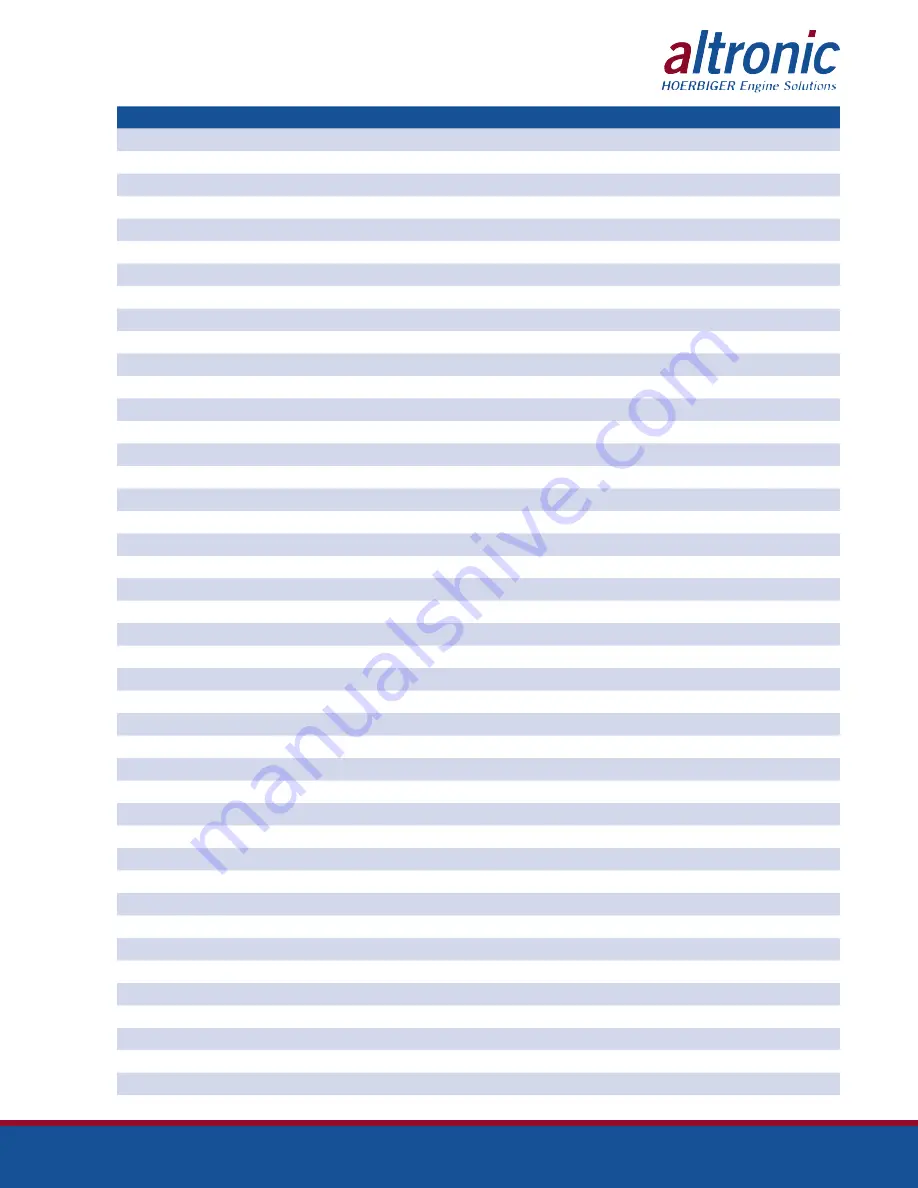
DE-3000+ IOI 8-15
All rights reserved © ALTRONIC, LLC 2015
58
ADDRESS
DESCRIPTION
42971
Channel 22 MIN SENSOR LIMIT (Writable)
42972
Channel 22 MAX SENSOR LIMIT (Writable)
42973
Channel 23 SPAN (Writable)
42974
Channel 23 ZERO (Writable)
42975
Channel 23 MIN SENSOR LIMIT (Writable)
42976
Channel 23 MAX SENSOR LIMIT (Writable)
42977
Channel 24 SPAN (Writable)
42978
Channel 24 ZERO (Writable)
42979
Channel 24 MIN SENSOR LIMIT (Writable)
42980
Channel 24 MAX SENSOR LIMIT (Writable)
42981
Channel 25 SPAN (Writable)
42982
Channel 25 ZERO (Writable)
42983
Channel 25 MIN SENSOR LIMIT (Writable)
42984
Channel 25 MAX SENSOR LIMIT (Writable)
42985
Channel 26 SPAN (Writable)
42986
Channel 26 ZERO (Writable)
42987
Channel 26 MIN SENSOR LIMIT (Writable)
42988
Channel 26 MAX SENSOR LIMIT (Writable)
42989
Channel 27 SPAN (Writable)
42990
Channel 27 ZERO (Writable)
42991
Channel 27 MIN SENSOR LIMIT (Writable)
42992
Channel 27 MAX SENSOR LIMIT (Writable)
42993
Channel 28 SPAN (Writable)
42994
Channel 28 ZERO (Writable)
42995
Channel 28 MIN SENSOR LIMIT (Writable)
42996
Channel 28 MAX SENSOR LIMIT (Writable)
42997
Channel 29 SPAN (Writable)
42998
Channel 29 ZERO (Writable)
42999
Channel 29 MIN SENSOR LIMIT (Writable)
43000
Channel 29 MAX SENSOR LIMIT (Writable)
43001
Channel 30 SPAN (Writable)
43002
Channel 30 ZERO (Writable)
43003
Channel 30 MIN SENSOR LIMIT (Writable)
43004
Channel 30 MAX SENSOR LIMIT (Writable)
43653
Channel 31 SPAN (Writable – See Note 4 below for Calibration)
43654
Channel 31 ZERO (Writable – See Note 4 below for Calibration)
43655
Channel 31 MIN SENSOR LIMIT (Writable – See Note 4 below for Calibration)
43656
Channel 31 MAX SENSOR LIMIT (Writable – See Note 4 below for Calibration)
43657
Channel 32 SPAN (Writable)
43658
Channel 32 ZERO (Writable)
43659
Channel 32 MIN SENSOR LIMIT (Writable)
43660
Channel 32 MAX SENSOR LIMIT (Writable)
Содержание DE-3000+ Series
Страница 71: ...DE 3000 IOI 8 15 All rights reserved ALTRONIC LLC 2015 71 FIG 2 DE 3000 SYSTEM DIAGRAM DE 3000 ...
Страница 74: ...DE 3000 IOI 8 15 All rights reserved ALTRONIC LLC 2015 74 FIG 5 WIRING DIAGRAM PERSONAL COMPUTER ...
Страница 75: ...DE 3000 IOI 8 15 All rights reserved ALTRONIC LLC 2015 75 FIG 6 WIRING DIAGRAM SENSOR AND TRANSDUCER INPUTS ...
Страница 76: ...DE 3000 IOI 8 15 All rights reserved ALTRONIC LLC 2015 76 FIG 7 WIRING DIAGRAM CURRENT LOOP OUTPUTS ...
Страница 77: ...DE 3000 IOI 8 15 All rights reserved ALTRONIC LLC 2015 77 FIG 8 WIRING DIAGRAM DIGITAL OUTPUT SWITCHES ...