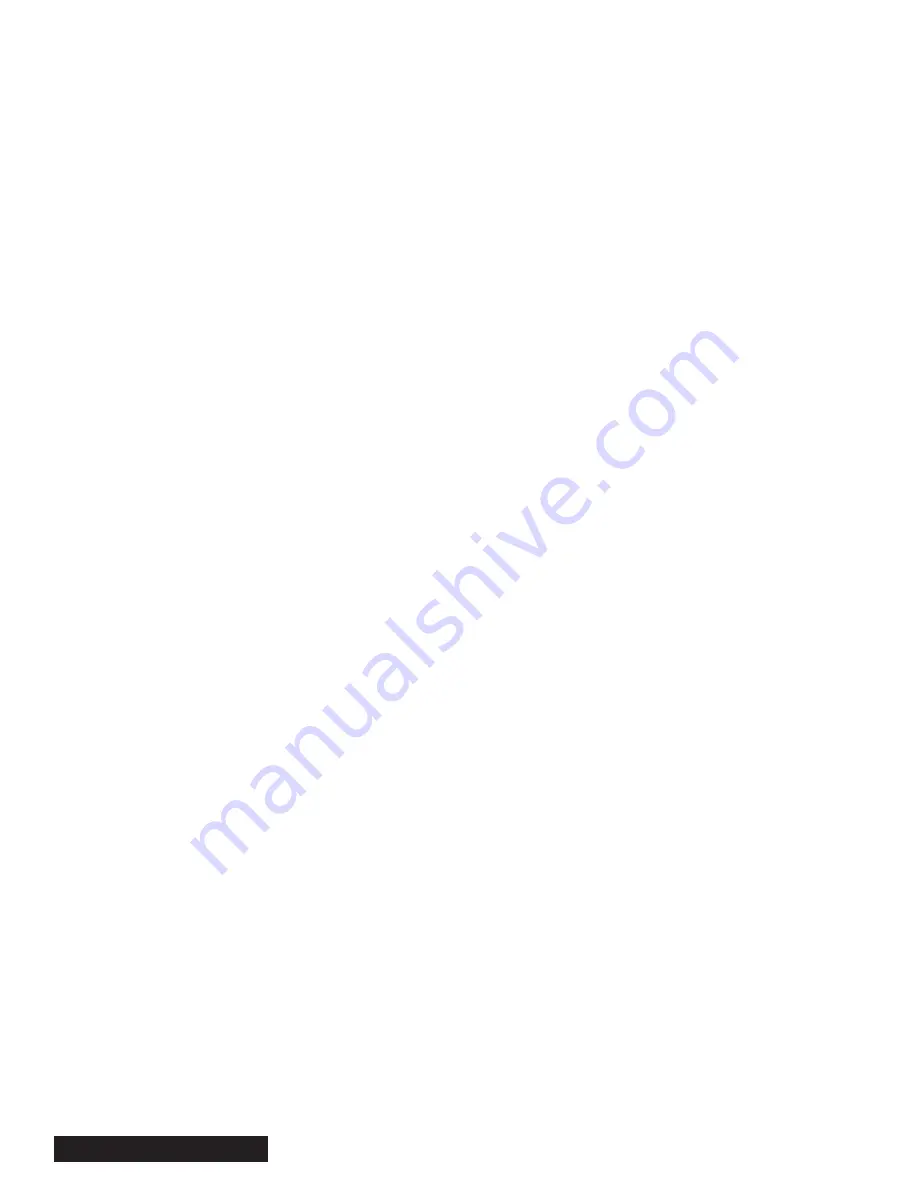
40 • Section 7 — Maintenance
Return Line Filter
The return line filter is a cartridge type 10 micron filter
that cleans the oil before it enters the reservoir.
The return line filter head contains a filter bypass valve.
This bypass valve opens when there is a pressure drop
of 15 psi (1.03 bar) across the filter cartridge. When the
valve is open, oil flows directly into the reservoir bypass
-
ing the filter. This prevents the cartridge from bursting
during cold start ups or if it is clogged.
If the filter becomes clogged the oil flows directly into
the reservoir bypassing the filter. The lack of filtration will
eventually damage hydraulic components.
During the break-in period of a new unit, the hydraulic
components will deposit break-in wear particles in the
return line filter cartridge. Change the return line car
-
tridge after the first 15 to 25 PTO hours. Then, change
the cartridge as recommended by the checklists in the
Appendix. If the unit is operated in very dusty conditions,
replace the return line filter more often. Also, replace the
cartridge after new oil has circulated through the system
for the first time.
Always replace the return line filter cartridge with a
genuine Altec replacement part. Other filters may screw
or fit into the filter housing, but may not have the same
micron rating. Also, other filters may allow oil to bypass
at a different rate.
Oil Specifications
Use high quality oil in the hydraulic system. The oil should
contain rust, oxidation, and corrosion inhibitors. It should
also contain antifoam and antiwear additives.
Hydraulic oil is commonly classified by viscosity. The
viscosity of hydraulic oil changes with temperature. The
higher the viscosity index of an oil, the less the viscosity
will change as the temperature changes. A multiviscosity
oil contains additives which increase the viscosity index.
Multiviscosity oils should have high shear stability to
maintain oil performance by avoiding excessive change
in viscosity.
The ability of hydraulic oil to provide adequate fluid at
low temperatures is measured by its pour point. If the
pour point is not low enough, oil will not flow into the
pump at a fast enough rate when the pump is operated
at low temperatures. This will cause cavitation, which
can quickly destroy the pump.
Notice
Only use hydraulic oil as recommended. Other fluids
added to the hydraulic system can increase compo-
nent wear and affect the lubricating characteristics
of the oil.
Only use oils meeting the viscosity rating for military
specification MIL-5606 in extremely cold climates.
These oils have fewer antiwear characteristics and
are not recommended for full time use.
Most companies can supply equivalent oils. The oil
selected for the hydraulic system depends on the tem-
perature during unit operation.
Oil Condition
An important part of hydraulic system preventive main-
tenance includes checking the condition of the hydraulic
oil.
Periodic laboratory analysis is the most accurate method
of determining the condition of hydraulic oil and determin-
ing when it should be changed. A visual inspection may
also be useful to check oil condition.
A hydraulic oil supplier should be able to do testing or
recommend a test laboratory. The laboratory should
provide the following information.
• Particle count
• Trace element analysis (component wear, outside
contaminants, and oil additive concentrations)
• Viscosity test
• Water content test
Before taking a sample of oil, operate the unit to circu-
late the oil. Warm it to operating temperature. Take the
sample from the middle level of the reservoir using a
clean hand pump, such as a disposable syringe and a
piece of plastic tubing. If this is not available, drain the
sample from the bottom of the reservoir. Allow several
quarts of oil to flow out before collecting the sample to
remove any dirt and water that has collected in the res-
ervoir near the drain.
If a sample container has not been provided by the labora-
tory, use a wide mouth, screw top, clear glass container.
Clean it with hot water and detergent. Rinse it thoroughly
and let it air dry before putting oil into it.
Once the report is received, compare it to previous oil
analysis reports for the same unit. This information will
provide trends toward oil deterioration. It may give early
warnings of a problem developing within hydraulic system
components.
Содержание DRM 12
Страница 3: ......
Страница 7: ...2 Section 1 Introduction...
Страница 17: ...12 Section 3 Safety Rear View Top View Bottom View 12 5 22 19 10 23 10 17 30 20 3 2 30...
Страница 18: ...Section 3 Safety 13 4 8 7 2 3 970116658 1 6 5...
Страница 19: ...14 Section 3 Safety 970116649 970116652 12 14 13 10 11 9...
Страница 21: ...16 Section 3 Safety D G G D 25 26 24 27 23 22...
Страница 22: ...Section 3 Safety 17 970137595 3X 30 31 28 29...
Страница 23: ...18 Section 3 Safety...
Страница 41: ...36 Section 6 Care of the Unit...
Страница 62: ...Appendix...
Страница 63: ......
Страница 79: ...16 Appendix Glossary...
Страница 83: ...Appendix Daily Preoperational Checklist...
Страница 85: ...Appendix Preventive Maintenance and Inspection Checklist...
Страница 88: ......
Страница 89: ......
Страница 91: ......
Страница 93: ......
Страница 96: ...07 13 970413443 A 2A PAGE 1 OF 2 ASSEMBLY FEED SYSTEM HYDRAULIC LIFT DRM 12...
Страница 99: ...07 13 970413407 A 3A PAGE 1 OF 4 ASSEMBLY FEED CONTROL HYDRAULIC LIFT DRM 12...
Страница 103: ...08 13 970485929 A 4A PAGE 1 OF 3 ASSEMBLY HAND CRANK CHUTE ROTATION DRUM CHIPPER...
Страница 108: ...07 13 970413409 A 5A PAGE 1 OF 3 ASSEMBLY POWER SYSTEM KUBOTA 67 HP 74 HP 99 HP DIESEL DRM 12...
Страница 113: ...07 13 970413438 A 6A PAGE 1 OF 4 FINAL ASSEMBLY DRM 12...
Страница 117: ......
Страница 118: ......
Страница 119: ......
Страница 120: ......
Страница 121: ......
Страница 122: ......
Страница 123: ......
Страница 124: ......
Страница 125: ......
Страница 127: ......
Страница 128: ......
Страница 129: ......
Страница 138: ...79A PAGE 1 OF 3 05 13 970457633 A ASSEMBLY FUEL SYSTEM DRM12 CFD1217...