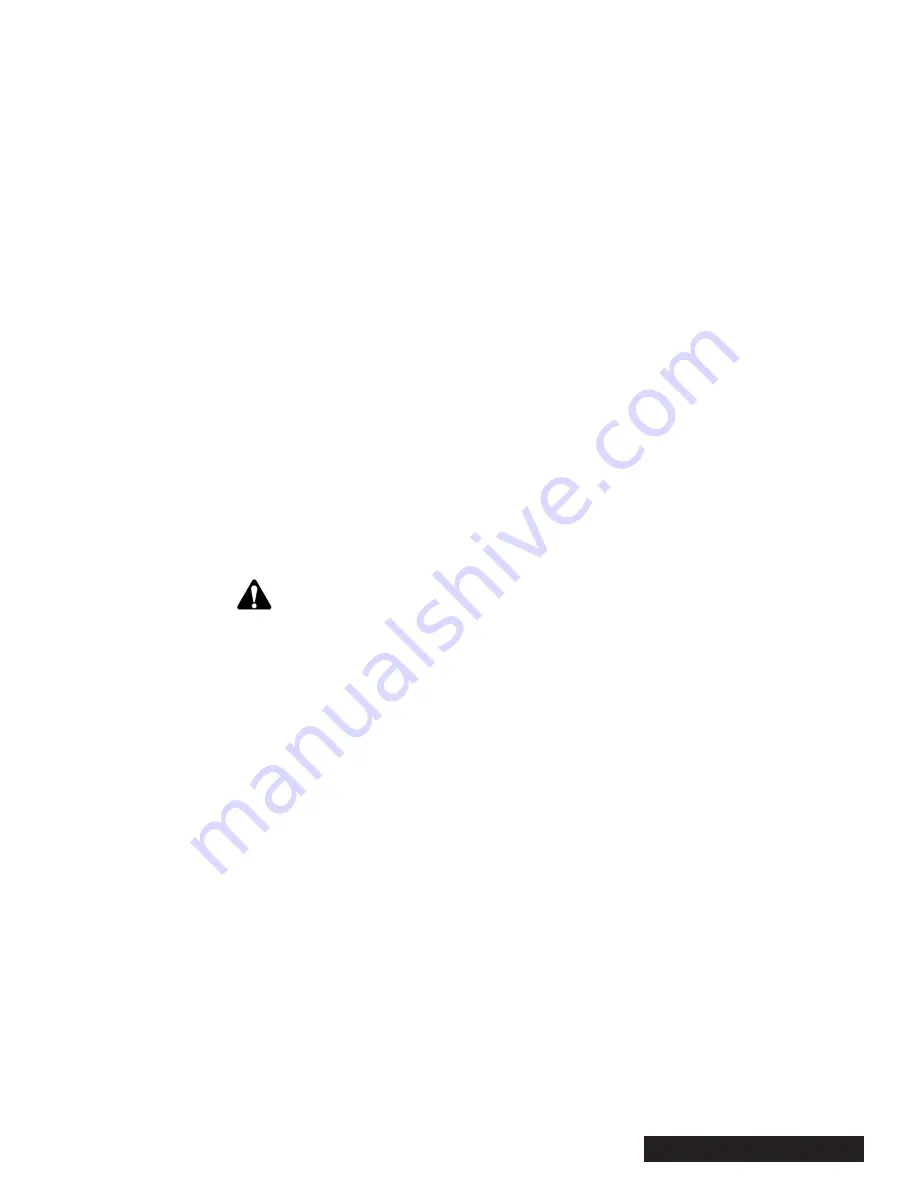
Section 7 — Maintenance • 53
Engine/Clutch
Check engine/clutch operator’s manuals for specific
bearing lubrication, maintenance, and replacement
procedures.
Bearing Replacement
Spherical Bearings
Spherical roller bearings are used on both sides of the
cutter assembly and all feed roll bearings. Self-aligning
bearings such as these are used in areas where perfect
alignment is difficult to maintain. This type of bearing
allows the component to follow the movements of the
structure without applying a side load to the internal
components of the cylinder. Daily lubrication of these
bearing is required to prevent the inner rim that maintains
the alignment from seizing to the outer rim of the bearing.
Daily lubrication ensures contamination is flushed from
the bearings inner components.
Cutter Bearing Replacement
1. Perform LOTO procedures.
2. Remove blades.
3. Remove top cutter housing, belt guard, and bearing
cover.
Warning
Death or serious injury may occur when using improp-
er lifting rigging. Use properly rated hoist, spreader
bar and straps when hoisting drum assembly.
4. Support the cutter assembly using an overhead
crane or hoist. Refer to unit specifications for weight
of cutter assembly.
5. Remove any pulleys or auxiliary equipment from the
out board sections of the cutter shaft.
6. Clean and de-bur the exposed sections of the shaft.
7. Remove the two set screws on each bearing as-
sembly.
8. Remove the four bearing flange bolts and remove
the bearing.
9. Install bearings. Apply Loctite #242 to all four bearing
flange bolts. Torque the four bearing flange bolts to
the torque values in the Appendix.
10. Center the cutter assembly in the cutter housing.
11. Make sure one set screw on each bearing is aligned
with the flat on the cutter shaft. Apply Loctite #242
to all four set screws. Tighten all four set screws.
12. Reinstall blades and adjust the anvil/blade gap.
13. Reinstall pulleys or auxiliary equipment previously
removed.
14. Reinstall all guards and covers.
Electrical
Electrohydraulic Control
The DRM 12 is equipped with both electronic and hydraulic
controls. The system is comprised of the following parts.
• Hydraulic reservoir located on the street side of the
drum housing.
• Hydraulic pump mounted on the engine inside the
engine housing.
• Main control valve located on top of the infeed chute.
• Hydraulic cylinder anchored at the feed box and feed
roller assembly.
• Holding valve located on the curb side of the feed
box.
• EFC valve located on the infeed chute.
• Feed motor located on the curb side of the feed roller
assembly.
• Magnetic speed sensor (magnetic pickup sensor)
located on the street side of the drum shaft behind
the bearing guard.
• Control module located underneath the control valve
mounting bracket.
FeedSense® (EFC)
FeedSense® is a sub-system of the overall electrohydrau
-
lic operation of the chipper which manages the cutting
drum speed. This system ensures that the drum is cut
-
ting at an optimal speed which yields best efficiency and
maximum throughput. The specific components involved
in the system are the control module, electrohydraulic
EFC valve, and the magnetic speed sensor.
Using the magnetic pickup sensor, the control module
monitors the drum rpm. The EFC valve remains in the
neutral (blocked) state until the proper rpm have been
reached. This prevents rotation of the motor in both
forward and reverse directions. When the drum rpm is
above 2,150 rpm, the EFC valve allows hydraulic flow
to the motor. Now the operator can manipulate the feed
control bar forward and reverse to feed the material in
and out respectively. When feeding wood forward, the
Содержание DRM 12
Страница 3: ......
Страница 7: ...2 Section 1 Introduction...
Страница 17: ...12 Section 3 Safety Rear View Top View Bottom View 12 5 22 19 10 23 10 17 30 20 3 2 30...
Страница 18: ...Section 3 Safety 13 4 8 7 2 3 970116658 1 6 5...
Страница 19: ...14 Section 3 Safety 970116649 970116652 12 14 13 10 11 9...
Страница 21: ...16 Section 3 Safety D G G D 25 26 24 27 23 22...
Страница 22: ...Section 3 Safety 17 970137595 3X 30 31 28 29...
Страница 23: ...18 Section 3 Safety...
Страница 41: ...36 Section 6 Care of the Unit...
Страница 62: ...Appendix...
Страница 63: ......
Страница 79: ...16 Appendix Glossary...
Страница 83: ...Appendix Daily Preoperational Checklist...
Страница 85: ...Appendix Preventive Maintenance and Inspection Checklist...
Страница 88: ......
Страница 89: ......
Страница 91: ......
Страница 93: ......
Страница 96: ...07 13 970413443 A 2A PAGE 1 OF 2 ASSEMBLY FEED SYSTEM HYDRAULIC LIFT DRM 12...
Страница 99: ...07 13 970413407 A 3A PAGE 1 OF 4 ASSEMBLY FEED CONTROL HYDRAULIC LIFT DRM 12...
Страница 103: ...08 13 970485929 A 4A PAGE 1 OF 3 ASSEMBLY HAND CRANK CHUTE ROTATION DRUM CHIPPER...
Страница 108: ...07 13 970413409 A 5A PAGE 1 OF 3 ASSEMBLY POWER SYSTEM KUBOTA 67 HP 74 HP 99 HP DIESEL DRM 12...
Страница 113: ...07 13 970413438 A 6A PAGE 1 OF 4 FINAL ASSEMBLY DRM 12...
Страница 117: ......
Страница 118: ......
Страница 119: ......
Страница 120: ......
Страница 121: ......
Страница 122: ......
Страница 123: ......
Страница 124: ......
Страница 125: ......
Страница 127: ......
Страница 128: ......
Страница 129: ......
Страница 138: ...79A PAGE 1 OF 3 05 13 970457633 A ASSEMBLY FUEL SYSTEM DRM12 CFD1217...