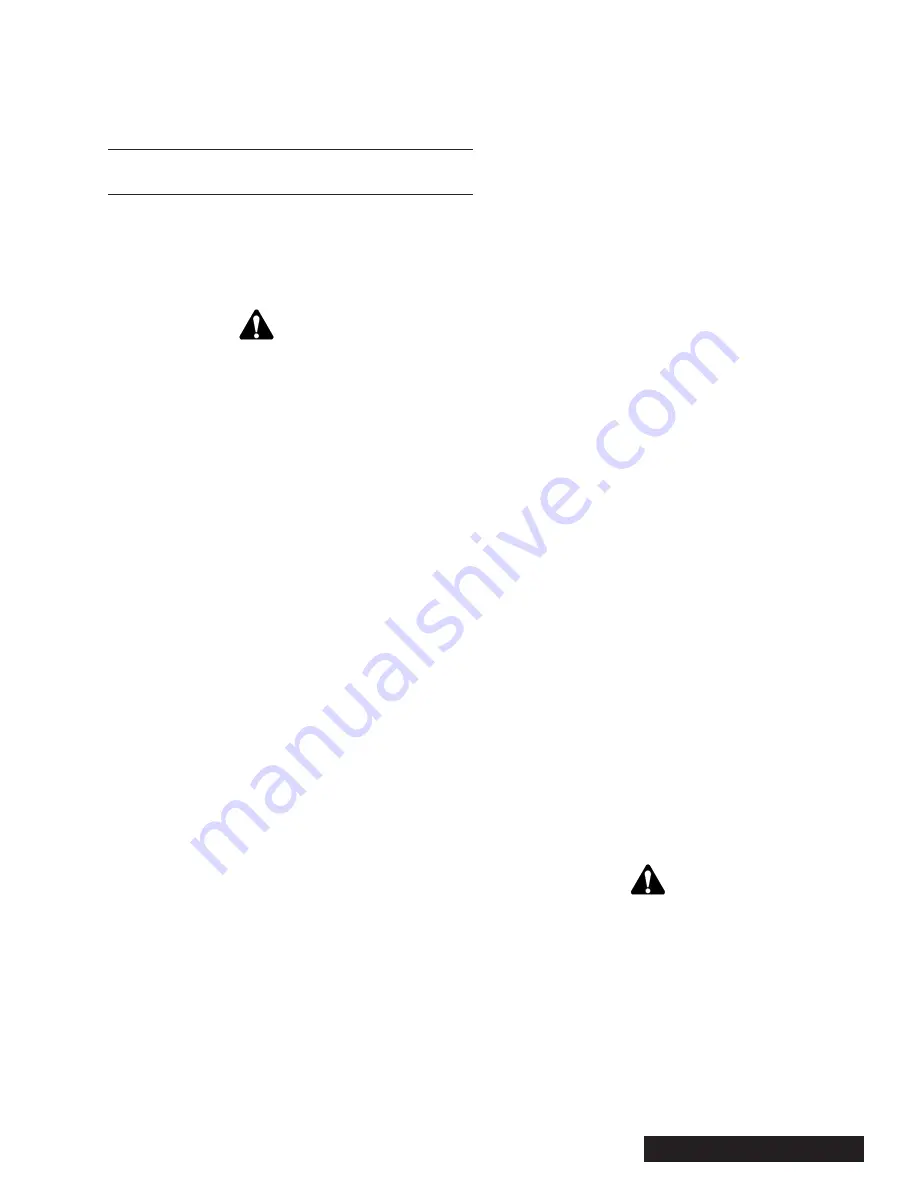
Section 7 — Maintenance • 49
Do not operate the equipment unless all covers and
guards are in place and properly secured.
Troubleshooting,
Testing, and Adjustments
Synchronizing Tow
Vehicle Brake Controller
To ensure safe brake performance and synchronizing,
read the brake controller manufacturer’s instructions com
-
pletely before attempting any synchronization procedure.
Caution
Injury and property damage can result from failure to
brake safely. Make sure the area is clear of vehicular
and pedestrian traffic.
Make several hard stops from 20 mph (32.3 kph) on a dry
paved road free of sand and gravel. If the trailer brakes
lock and slide, slightly decrease the gain setting on the
controller. If they do not slide, slightly increase the gain
setting. Adjust the controller just to the point of impending
brake lockup and wheel skid.
Notice
Not all trailer brakes are capable of wheel lockup.
Loading conditions, brake type, wheel and tire size
can all affect whether a brake can lock up. It is not
generally considered desirable to lock up the brakes
and slide the tires. This can cause unwanted spot-
ting of tires and could also result in a loss of control.
For proper braking performance, it is recommended that
the controller be adjusted to allow the trailer brakes to
come on just slightly ahead of the tow vehicle brakes.
When properly adjusted, there will be no sensation of
trailer jerking or pushing the tow vehicle during braking.
Breakaway Braking System
To ensure proper operation of the breakaway system, the
chipper battery and charging system must be operating
properly. The chipper must be properly hitched to the tow
vehicle. This must include the following.
• The hitch properly fastened and all retaining pins
secured.
• Safety chains crossed in an X pattern under the
tongue and secured to the tow vehicle. Allow enough
slack in the chains for turning.
• Breakaway cable must be of shorter length than the
chains.
In the event of an unwanted separation of the chipper from
the tow vehicle, the tongue should drop into the cradle
formed by the X pattern of the chains. The breakaway
cable must pull the plunger from the switch before the
entire tongue weight of the chipper comes to a rest in
the chain cradle.
When the breakaway switch is activated, full voltage
from the chipper battery is applied to the brakes. The
chipper will come to a complete stop, but will not lock
up the brakes.
Testing of the breakaway can be accomplished by jack-
ing up the chipper, spinning the wheel, and pulling the
plunger. The brakes should apply. The tires may lock up
on a slick or unstable surface.
Notice
The breakaway switch is to be used for emergencies
only. The breakaway system rapidly discharges the
battery when the plunger pin is removed. Reinstall
plunger immediately after completion of test.
Inspection and Maintenance
Your chipper brakes must be inspected and serviced
immediately if a loss of performance is indicated. With
normal use, servicing at one year intervals is usually
adequate. With increased usage, this work should be
done more frequently as required. Magnets and shoes
must be changed when they become excessively worn
or scored, a condition which can reduce vehicle braking.
Clean the backing plate, magnet arm, magnet and brake
shoes. Make certain that all the parts removed are re-
placed in the same brake and drum assembly. Inspect for
any loose or worn parts, stretched or deformed springs
and replace as necessary. For ease of maintenance
Altec parts department can supply complete backing
plate assemblies. This includes new shoes, magnets,
springs, and connecting hardware already assembled,
ready to bolt in place.
Caution
Serious illness can result from breathing asbestos
dust. Avoid breathing or creating dust when servic-
ing the brakes.
Avoid machining, filling, or grinding the brake linings.
Do not use compressed air or dry brushing for cleaning
(dust can be removed with a damp brush).
Brake Adjustment
Adjust brakes at the following intervals. Refer to the axle
owners manual.
Содержание DRM 12
Страница 3: ......
Страница 7: ...2 Section 1 Introduction...
Страница 17: ...12 Section 3 Safety Rear View Top View Bottom View 12 5 22 19 10 23 10 17 30 20 3 2 30...
Страница 18: ...Section 3 Safety 13 4 8 7 2 3 970116658 1 6 5...
Страница 19: ...14 Section 3 Safety 970116649 970116652 12 14 13 10 11 9...
Страница 21: ...16 Section 3 Safety D G G D 25 26 24 27 23 22...
Страница 22: ...Section 3 Safety 17 970137595 3X 30 31 28 29...
Страница 23: ...18 Section 3 Safety...
Страница 41: ...36 Section 6 Care of the Unit...
Страница 62: ...Appendix...
Страница 63: ......
Страница 79: ...16 Appendix Glossary...
Страница 83: ...Appendix Daily Preoperational Checklist...
Страница 85: ...Appendix Preventive Maintenance and Inspection Checklist...
Страница 88: ......
Страница 89: ......
Страница 91: ......
Страница 93: ......
Страница 96: ...07 13 970413443 A 2A PAGE 1 OF 2 ASSEMBLY FEED SYSTEM HYDRAULIC LIFT DRM 12...
Страница 99: ...07 13 970413407 A 3A PAGE 1 OF 4 ASSEMBLY FEED CONTROL HYDRAULIC LIFT DRM 12...
Страница 103: ...08 13 970485929 A 4A PAGE 1 OF 3 ASSEMBLY HAND CRANK CHUTE ROTATION DRUM CHIPPER...
Страница 108: ...07 13 970413409 A 5A PAGE 1 OF 3 ASSEMBLY POWER SYSTEM KUBOTA 67 HP 74 HP 99 HP DIESEL DRM 12...
Страница 113: ...07 13 970413438 A 6A PAGE 1 OF 4 FINAL ASSEMBLY DRM 12...
Страница 117: ......
Страница 118: ......
Страница 119: ......
Страница 120: ......
Страница 121: ......
Страница 122: ......
Страница 123: ......
Страница 124: ......
Страница 125: ......
Страница 127: ......
Страница 128: ......
Страница 129: ......
Страница 138: ...79A PAGE 1 OF 3 05 13 970457633 A ASSEMBLY FUEL SYSTEM DRM12 CFD1217...