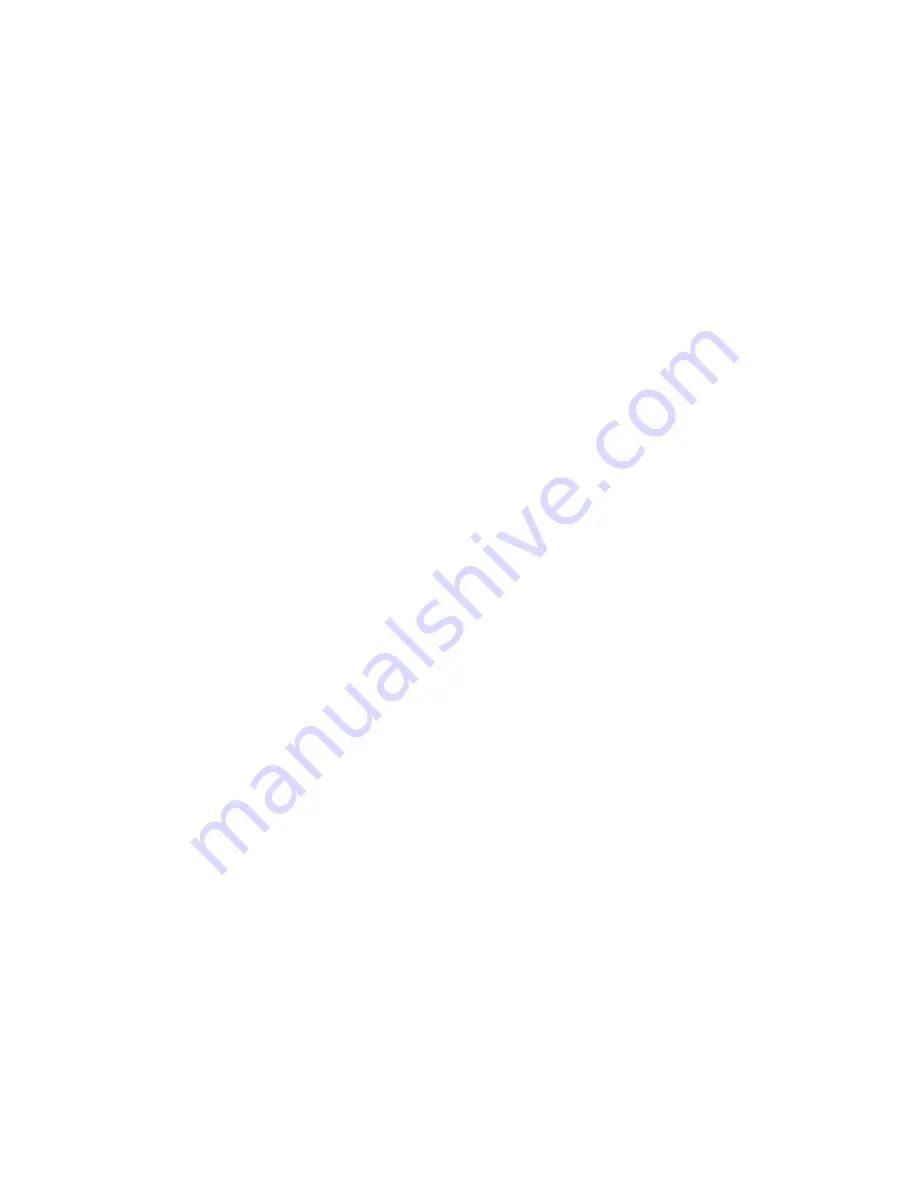
Section 4 — Before You Operate… • 27
Traffic, coworkers, spectators, debris, brush, and other
equipment constantly change the hazards so constant
awareness and adaptation to those changes must be
practiced. Placing yourself, or others into a dangerous
situation, being careless or simply not paying attention
can result in death or serious injury.
Never place hands, arms, legs, or feet into the infeed
chute.
Never attempt to push material into the infeed chute us-
ing your hands or feet.
Do not use any item with metal components as a tool
to push brush into the cutter mechanism. Blade failure
can occur and cause violent discharge from the cutter
mechanism causing death or serious injury. Only materi-
als which are being chipped should be used as push or
drag tools.
• Feeding brush to the chipper involves a technique
that requires a smooth continuous motion. Place the
prepared brush on the feed table, push it into the
throat of the cutter housing, and then move quickly
to the curb side of the chipper.
• Please follow the procedures and safety designations
listed below.
Notice
Make sure the brush is not too large for the machine.
Placing material that is too large for the opening can
result in clogging or jamming of the material.
The operator shall stand to the side when operating the
chipper. Material in the transition area could be kicked
back while positioning the material into the infeed chute.
In the event there is debris in the transition, use another
piece of wood to clear the transition area before standing
behind the infeed chute with the feed roller in a raised
position.
While feeding the chipper it is common for material to be
suddenly and violently kicked up or to the side. Never
stand or position yourself directly above or beside mate-
rial while being fed. Once material is engaged, quickly
move away from the material.
On equipment with FeedSense®, special care must be
taken since the material starts and stops at intervals
without warning. Never approach the material once it
has become engaged by the feed roller. In the event
that material has not advanced in a reasonable amount
of time, reverse the material completely with the control
bar and start the material again. Make sure the throttle
is completely advanced to the factory preset setting to
ensure proper operation of the FeedSense®.
Make sure the chip deflector curtain is in proper condi
-
tion, in place, and secure. This device is provided to stop
or reduce the velocity of any kickbacks during chipping
operations.
During chipping operations, never position yourself di-
rectly behind the infeed chute. Brush or debris can be
kicked back or up without warning.
Do not feed material while another operator is between
you and the infeed chute. Only one operator should feed
the unit at any given time.
Never attempt to lift material that is beyond your lifting
capabilities and incorporate proper lifting techniques to
avoid injury.
Improper use of cranes, winches, and tractors to load
material can result in death or serious injury and can se-
verely damage the equipment. The use of these types of
lifting tools should be operated by experienced personnel
that are trained in their proper use, understand the limita-
tions of the chipper, can comprehend the ramifications
and dangers of improper use and have been authorized
by the employer to perform these procedures. Dam-
age to the equipment through the use of non-attached
or improperly used lifting devices may not be covered
under the warranty.
Do not feed crotches or multiple pieces of wood that can
become a pinch point during feeding.
Do not lean, stand, sit, or permit others to lean, stand, or
sit on the feed table during chipping operations.
Never reach into or lean over the feed table or into the
infeed chute.
Keep the working area clear of limbs and debris. Tripping
or entanglement can allow the operator to be dragged
into the chipper.
Do not throw clean up sweepings into the cutter mecha-
nism. Foreign material such as stones, wire or metal
scrap can cause blade failure.
1. Position the cut end of the brush toward the feed
table. Approach the feed table from the curb side at
an angle that will not position you directly in front but
to the side of the feed table to avoid brush kickback
and traffic hazards.
Содержание DRM 12
Страница 3: ......
Страница 7: ...2 Section 1 Introduction...
Страница 17: ...12 Section 3 Safety Rear View Top View Bottom View 12 5 22 19 10 23 10 17 30 20 3 2 30...
Страница 18: ...Section 3 Safety 13 4 8 7 2 3 970116658 1 6 5...
Страница 19: ...14 Section 3 Safety 970116649 970116652 12 14 13 10 11 9...
Страница 21: ...16 Section 3 Safety D G G D 25 26 24 27 23 22...
Страница 22: ...Section 3 Safety 17 970137595 3X 30 31 28 29...
Страница 23: ...18 Section 3 Safety...
Страница 41: ...36 Section 6 Care of the Unit...
Страница 62: ...Appendix...
Страница 63: ......
Страница 79: ...16 Appendix Glossary...
Страница 83: ...Appendix Daily Preoperational Checklist...
Страница 85: ...Appendix Preventive Maintenance and Inspection Checklist...
Страница 88: ......
Страница 89: ......
Страница 91: ......
Страница 93: ......
Страница 96: ...07 13 970413443 A 2A PAGE 1 OF 2 ASSEMBLY FEED SYSTEM HYDRAULIC LIFT DRM 12...
Страница 99: ...07 13 970413407 A 3A PAGE 1 OF 4 ASSEMBLY FEED CONTROL HYDRAULIC LIFT DRM 12...
Страница 103: ...08 13 970485929 A 4A PAGE 1 OF 3 ASSEMBLY HAND CRANK CHUTE ROTATION DRUM CHIPPER...
Страница 108: ...07 13 970413409 A 5A PAGE 1 OF 3 ASSEMBLY POWER SYSTEM KUBOTA 67 HP 74 HP 99 HP DIESEL DRM 12...
Страница 113: ...07 13 970413438 A 6A PAGE 1 OF 4 FINAL ASSEMBLY DRM 12...
Страница 117: ......
Страница 118: ......
Страница 119: ......
Страница 120: ......
Страница 121: ......
Страница 122: ......
Страница 123: ......
Страница 124: ......
Страница 125: ......
Страница 127: ......
Страница 128: ......
Страница 129: ......
Страница 138: ...79A PAGE 1 OF 3 05 13 970457633 A ASSEMBLY FUEL SYSTEM DRM12 CFD1217...