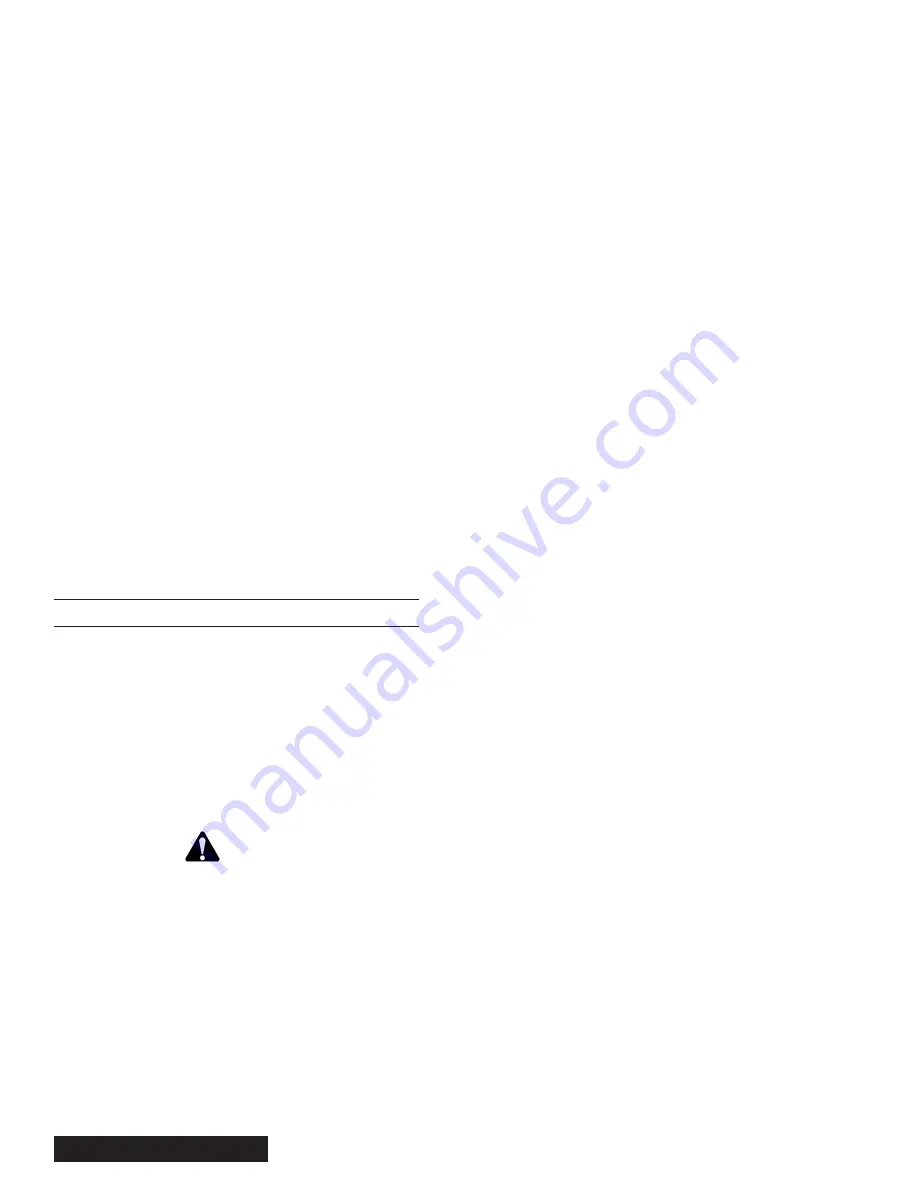
44 • Section 7 — Maintenance
3. Pump grease into the grease fitting. The old, displaced
grease will begin to flow back out the cap around the
grease gun nozzle.
4. When the new, clean grease is observed, remove
the grease gun, wipe off any excess, and replace
the rubber plug in the cap.
Refer to the axle manufacturer’s manual for more infor
-
mation.
Jack Stand
Depending on the model jack stand supplied with the
chipper there may be a grease fitting. If so, lubricate with
one or two pumps.
Engine Power Take-Off (PTO)
The PTO clutch mechanism is supplied by the engine
manufacturer. It is very important to lubricate the PTO
bearings, clutch levers, and linkage. For specific informa
-
tion and lubrication interval requirements refer to your
PTO owner’s manual.
Engine
Due to varying engine models and engine specifications,
check the engine owner’s manual (EOM) for the specific
lubrication requirements of your supplied engine.
Structures
The structural components of the unit are identified in the
Component Identification in Section 2. The unit has been
designed to meet or exceed the ANSI Specifications for
Z133.1 Safety Requirements.
Regular inspection of the welds and structures is required
to make sure that components maintain their strength.
Periodic cleaning of the structures is also recommended.
This will prevent damage that can result from dirt ac-
cumulation.
Caution
Injury can result from slipping and falling. Use care
when cleaning the unit.
Periodic inspection of the structures is recommended
to be certain there is no deformation, abnormal wear or
abrasion, interference between moving parts, or cracking
of the welds on structural members.
Inspect the structures and welds as recommended by
the checklists in the Appendix.
Care of Exterior Surfaces
Altec units are manufactured out of structural steel, gal-
vanized steel and/or aluminum components with differing
resistance to corrosion. While Altec uses components,
designs and coatings that maximize corrosion resistance,
regular cleaning and maintenance is necessary to pre-
serve the finish over the life of the equipment.
Frequent and regular washing will lengthen the life of the
new equipment’s painted finish and components. Wash
the equipment frequently with warm or cold water to
remove dirt and preserve the original luster of the paint.
Never wash the equipment in direct sunlight or when
the metal surfaces are hot to the touch as it may cause
streaks on the finish. Caution must be used in selecting
detergents and degreasers that may damage the finish.
Use only commercially available automotive grade clean
-
ers. High pressure washing systems should be used with
caution, with the tip of the nozzle maintained at a distance
of 12” (30.5 cm) or more from the surface.
It is particularly important to wash the unit during winter
months as salt and other ice melting products are ex-
tremely corrosive and can damage the vehicle. Other
corrosive environments that would necessitate additional
washing may include coastal areas, farming communities
where chemicals are sprayed, or mining operations.
Waxing of the exterior is typically not required, however
waxing will provide additional protection and help restore
the finish to the original luster. This may not only improve
appearance, but will likely extend the service life of the
equipment.
It is important to repair any chips or scratches that occur
to prevent further corrosion. If the paint damage exposes
primer, then a liquid touch up paint may be used. Dam
-
age that extends to unpainted metal must be primed
prior to applying a top coat. Touch up paint for standard
Altec colors may be ordered by calling 1-877-GO ALTEC.
Your local auto body shop can assist you with matching
a custom color.
Equipment that is used in harsh environments and off road
use needs to have more routine washing and maintenance
to the under body area. When the equipment is washed
it should washed on the underside as well and routinely
checked for any damage to the paint/undercoat. Any
damage discovered should be touched up accordingly
with a good rust preventative material and/or undercoat.
This will help prevent corrosion that could spread from
these areas that are not easily seen.
Accumulated dirt can damage the unit and cause it to
malfunction. Dirt buildup also accelerates wear on the
components.
Содержание DRM 12
Страница 3: ......
Страница 7: ...2 Section 1 Introduction...
Страница 17: ...12 Section 3 Safety Rear View Top View Bottom View 12 5 22 19 10 23 10 17 30 20 3 2 30...
Страница 18: ...Section 3 Safety 13 4 8 7 2 3 970116658 1 6 5...
Страница 19: ...14 Section 3 Safety 970116649 970116652 12 14 13 10 11 9...
Страница 21: ...16 Section 3 Safety D G G D 25 26 24 27 23 22...
Страница 22: ...Section 3 Safety 17 970137595 3X 30 31 28 29...
Страница 23: ...18 Section 3 Safety...
Страница 41: ...36 Section 6 Care of the Unit...
Страница 62: ...Appendix...
Страница 63: ......
Страница 79: ...16 Appendix Glossary...
Страница 83: ...Appendix Daily Preoperational Checklist...
Страница 85: ...Appendix Preventive Maintenance and Inspection Checklist...
Страница 88: ......
Страница 89: ......
Страница 91: ......
Страница 93: ......
Страница 96: ...07 13 970413443 A 2A PAGE 1 OF 2 ASSEMBLY FEED SYSTEM HYDRAULIC LIFT DRM 12...
Страница 99: ...07 13 970413407 A 3A PAGE 1 OF 4 ASSEMBLY FEED CONTROL HYDRAULIC LIFT DRM 12...
Страница 103: ...08 13 970485929 A 4A PAGE 1 OF 3 ASSEMBLY HAND CRANK CHUTE ROTATION DRUM CHIPPER...
Страница 108: ...07 13 970413409 A 5A PAGE 1 OF 3 ASSEMBLY POWER SYSTEM KUBOTA 67 HP 74 HP 99 HP DIESEL DRM 12...
Страница 113: ...07 13 970413438 A 6A PAGE 1 OF 4 FINAL ASSEMBLY DRM 12...
Страница 117: ......
Страница 118: ......
Страница 119: ......
Страница 120: ......
Страница 121: ......
Страница 122: ......
Страница 123: ......
Страница 124: ......
Страница 125: ......
Страница 127: ......
Страница 128: ......
Страница 129: ......
Страница 138: ...79A PAGE 1 OF 3 05 13 970457633 A ASSEMBLY FUEL SYSTEM DRM12 CFD1217...