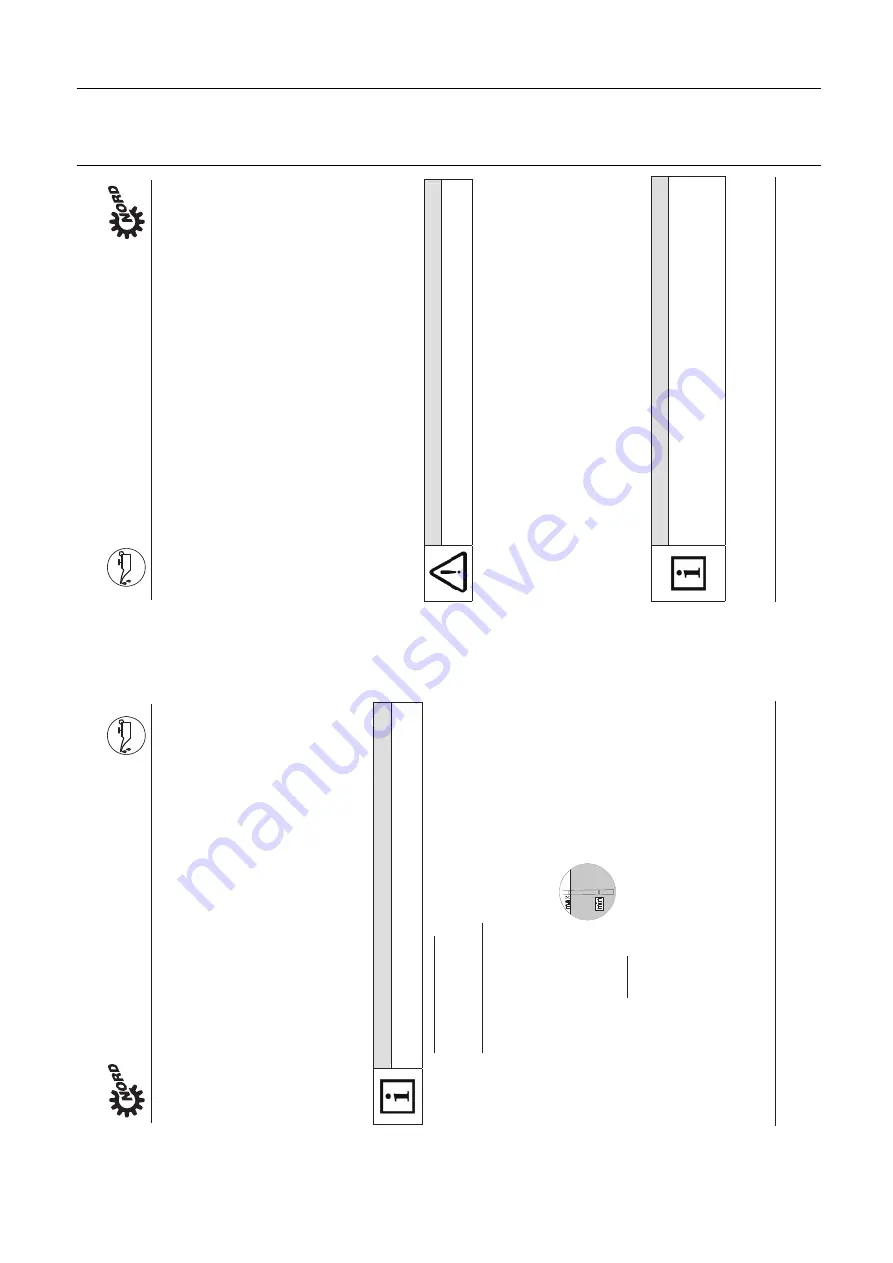
8 Appendix
Ensure totally clean surfaces during mounting. Always use original Alfa Laval parts.
5. Service and Maintenance
www.nord.com B1000-GB-0713
-23-
Check for running noises
If the gear
unit
produces
unusual
running
noises
and/or
vibrations,
this
could
indicate
damage
to
the gear unit In this case the gear should be shut down and a general overhaul carried out.
Check the oil lev
e
l
Section 6.1 describes the
versions and
the
corresponding
oil
level
screws. With
double gear
units, the oil
level must be checked on both units.
The pressure
vent must be at the position
marked in Section 6.1.
The oil level does not need to be checked on gear units without oil level screw (see Section 6.1).
Gear
unit types that are not supplied
full
of oil must
be filled before
the oil level
is checked.
(see
“Changing the oil”)
Checking the oil level:
1. The
oil
level
may
only
be
checked
when
the
gear
unit
is
at a standstill and
has
cooled
do
w
n
. The gear unit must be secured to prevent accidental switch-on.
2.
The oil level screw corresponding to the version must be screwed out. (See Section 6.1)
Note!
At the first oil
level check a small amount of oi
l may escape,
as
t
he oil level may
be below
the
lower edge of the oil level hole.
3.
Gear units with
oil level screw: The maximum oil level is the lower edge of the oil level hole.
The minimum
oil level i
s
4 mm below the oil level
hole.
If the oil level is too low, this must be
corrected
using
the correct type of oil. An oil level glass is available instead
of the oil level
screw
4.
Gear units with an oil level vessel: The oil level must be checked
in the
oil
le
v
e
l
v
e
ssel
with
the aid of the dipstick plug
(thread
G1 1/4).
The oil
level must be between
the upper and
lower mark when the dipstick
is
completely
screwed
in (see Fig.
5-2). The
oil level
must be
corrected with the correct type of
oil
if nece
ssary. These
gearboxes
may
only be
operated
in
the configuration stated in Section 6.1.
5. The
oil
level
screw
or
the
cap
screw
with
dipstick and
all
other
loosened screws
must
be
correctly re-tightened.
Figure 5-2: Check the oil level with a dipstick
5. Service and Maintenance
-24- B1000-GB-0713
www.nord.com
Regreasing
Some gear unit designs (free
drive shaft, Option
W, agitator designs
VL2 and VL3) are
equipped
with a regreasing device.
For agitator versions VL2 and VL3, the vent screw located opposite to the grease nipple must be
unscrewed before regreasing. Grease should be injected until a quantity of 20-25g escapes from
the vent hole. After this, the vent plug must be reinserted and tightened.
For
Option W
and some IEC
adapters, the
outer roller bearing must be
regreased with
approx.
20-25g of grease via the grease nipple provided
Recommended grease: Petamo GHY 133N (see Section 6.4: Klüber Lubrication).
Replacing the automatic lubricant dispenser
Screw-off the cartridge
case
cover (2), (see Fig. 4-
1)
.
The
lubrication
dispenser
(5) i
s
screwed
out and replaced with a new component (Part No. 283 0100). Then activate (see Chapter 4.2)!
Changing the oil
The figures
in Section 6.1
show the oil
drain screw,
the oil level screw and
the pressure
vent
screw for various designs.
Sequence:
1.
Place the drip tray below the oil drain screw or the oil drain cock
2.
Completely remove oil level screw, screwed sealing plug with dipstick if an oil level tank
is being used and oil drain screw.
Danger!
Warning: Hot oil!
3.
Drain all the oil from the gear unit.
4.
If the screw lock coating
of the oil dra
in screw o
r
oil level screw is
damaged
in the
thread, a n
e
w
oil level screw
must
b
e
used
or the
thread cleaned
and
coated
with
securing lubricant, e.g.
Loctite
242,
Loxeal
54-03
prior
to
inserting. Check
the
sealing
ring for damage. Replace with a new sealing ring in case of damage.
5.
Support the
seal
ring, insert the
oil drain screw into
the hole
and
tighten to the correct
torque! (See Section 6.2 for torque values)
6. Using
a
suitable
filling
device,
refill
with
oil
of
the
same
type
through
the
oil
level
hole
until oil emerges from the
oil level hole.
(The oil can
also be filled through the pressure
vent screw or a sealing plug
located higher
than the oil level). If an oil level vessel is
used, fill the oil through the upper inlet (thread G1¼) until the oil level is set as described
in Section 5.2.
7.
Wait at least 15 minutes, or at least 30 minutes if an oil level tank is used, and then
check the oil level. Proceed as described in Section 5.2.
Note!
The oil does not need to be changed on gear units without oil level screw (see Section 6.1).
These gear units are lubricated for life.
Standard
helical gear units have
n
o
oil level
screw. Here,
the oil is
topped up
through the
pressure vent bolt using the quantities listed in the table in Section 6.5.
60
Содержание ALTB-SB-20
Страница 1: ...ESE03056 EN6 2020 05 Original manual Instruction Manual ALTB SB 20...
Страница 2: ......
Страница 40: ...7 Parts list Service kits Ensure totally clean surfaces during mounting Always use original Alfa Laval parts 40...
Страница 43: ...8 Appendix Ensure totally clean surfaces during mounting Always use original Alfa Laval parts 8 3 WPS 43...
Страница 73: ...73...