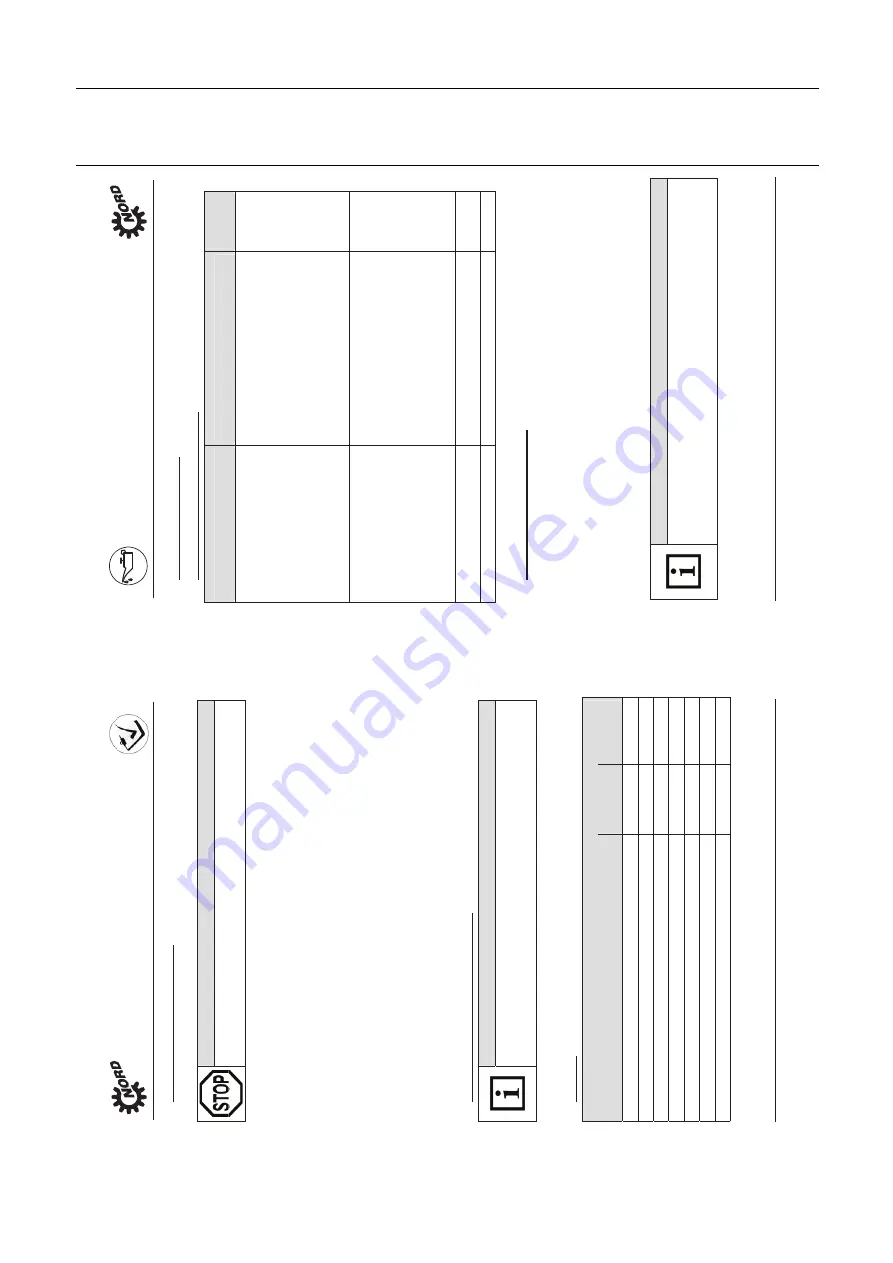
8 Appendix
Ensure totally clean surfaces during mounting. Always use original Alfa Laval parts.
4. Commissioning
www.nord.com B1000-GB-0713
-21-
4.3
Operation with lubricant cooling
Water cooling
Caution!
The drive may
only be commissioned after the cooling
spiral has been connected
to
the
cooling circuit, and the cooling circuit has been put into operation.
The coolant
must have
a similar thermal
capacity
as
water
(specific
thermal
capacity
at 20°C
c=4.18 kJ/kgK).
Industrial
water without any
air bubbles
o
r
sediments i
s
recommended
a
s
a
coolant. The water hardness must be
between 1° dH
and 15° dH, and the pH value must be
between pH 7.4 and pH 9.5. No aggressive liquids should be added to the coolant!
The
coolant pressure
must
not
exceed
8 ba
r
. The required
quantit
y
of coolant
is
10
litres/minute
, and
the
coolant inlet temperature
should not exceed
40°C;
we recommend
10°C
.
We also
recommend
fitting
a pressure reducer
at the
coolant inlet
to avoid any
damage due
to
excessive pressure.
If there is a danger
of frost
the operator
should
add a
suitable anti-freeze
solution
to the cooling
water.
The
temperature of the
cooling
w
a
ter
and the
cooling w
a
ter
fl
o
w
rate
must
be
superv
ised
and
ensured
by the operator.
Air/Oil cooler
This version
and all important
data
concerning
the air/oil
cooler
can
be obtained
from
Catalogue
G1000, or contact the manufacturer of the cooling unit.
4.4
Running-in time for the worm gear unit
Note!
In order to achieve maximum efficiency of the worm gear unit, the gear unit must be subjected
to a running-in period of approx. 25 h – 48 h under maximum load.
There may be a reduction in efficiency before the running-in period is complete.
4.5 Checklist
Checklist
Object of the check
Checked on
:
Information –
see Section
Is the vent plug activated or the pressure vent screwed in?
S
e
c
.
3
.4
Does the required configuration conform with the actual installation?
Sec. 6.1
Are the external gear shaft forces within permitted limits (chain tension)?
Sec. 3.6
Is the torque support correctly fitted?
Sec. 3.7
Are contact guards fitted to rotating components?
Sec. 3.9
Is the automatic lubricant dispenser activated?
Sec. 4.2
Is the cooling cover connected to the cooling circuit?
Sec. 3.12/4.3
5. Service and Maintenance
-22- B1000-GB-0713
www.nord.com
5.
Service and maintenance
5.1
Service and maintenance intervals
Service and Maintenance Intervals
Service and Maintenance Work
Information –
see Section
At least every six months
- Visual inspection
- Check for running noise
s
- Check oil level
- Re-grease
(applicable only to free drive shaft / Option W
and on agitator bearings / Option VL2 / VL3)
- Replace automatic lubricator (for operating
times < 8 h/day: a replacement interval for the
lubricant dispenser of 1 year is permissible)
(only with IEC/NEMA standard motors)
5.2
5.2
5.2
5.2
5.2
For operating temperatures up to 80°C
Every 10000 operating hours
at least every 2 years
(The interval is double this if the unit is
filled with synthetic products)
For higher temperatures or extreme
operating conditions (high humidity,
aggressive environments and large
temperature fluctuations) the oil change
intervals must be halved.
- Change the oil
- Clean or replace the vent plug.
5.2
5.2
Every 25000 operating hours,
at least every 5 years
- Replace shaft sealing rings if worn
- Re-lubrication of the bearings in the gear unit
5.2
5.2
At least every 10 years
- General overhaul
5.2
5.2
Service and maintenance w
o
rk
Servicing and maintenance
w
o
rk must only
be performed
b
y
qualified specialist
personnel.
Installation and maintenance
w
o
rk
must only
be performed
w
h
e
n
gear
units are a
t
a
standstill. The driv
e must be isolated and secured to prev
ent accidental start-up.
Visual inspection
The gear unit must be checked for leaks. In addition,
the gear unit must be inspected for external
damage and cracks in the hoses, hose
connections
and rubber buffers. Have the gear unit
repaired in case of
leaks, e.g. dripping gear oil
or cooling water, damage or cracks. P
lease contac
t
the NORD service department.
Note!
Shaft sealing rings are rubbing seals and have sealing lips made from an elastomer
material. These sealing lips are lubricated
w
ith a special grease at the factory. This
reduces the wear due to their function and ensures a long service life. An oil film in the
region of the rubbing sealing lip is therefore normal and is not due to leakage.
59
Содержание ALTB-SB-20
Страница 1: ...ESE03056 EN6 2020 05 Original manual Instruction Manual ALTB SB 20...
Страница 2: ......
Страница 40: ...7 Parts list Service kits Ensure totally clean surfaces during mounting Always use original Alfa Laval parts 40...
Страница 43: ...8 Appendix Ensure totally clean surfaces during mounting Always use original Alfa Laval parts 8 3 WPS 43...
Страница 73: ...73...