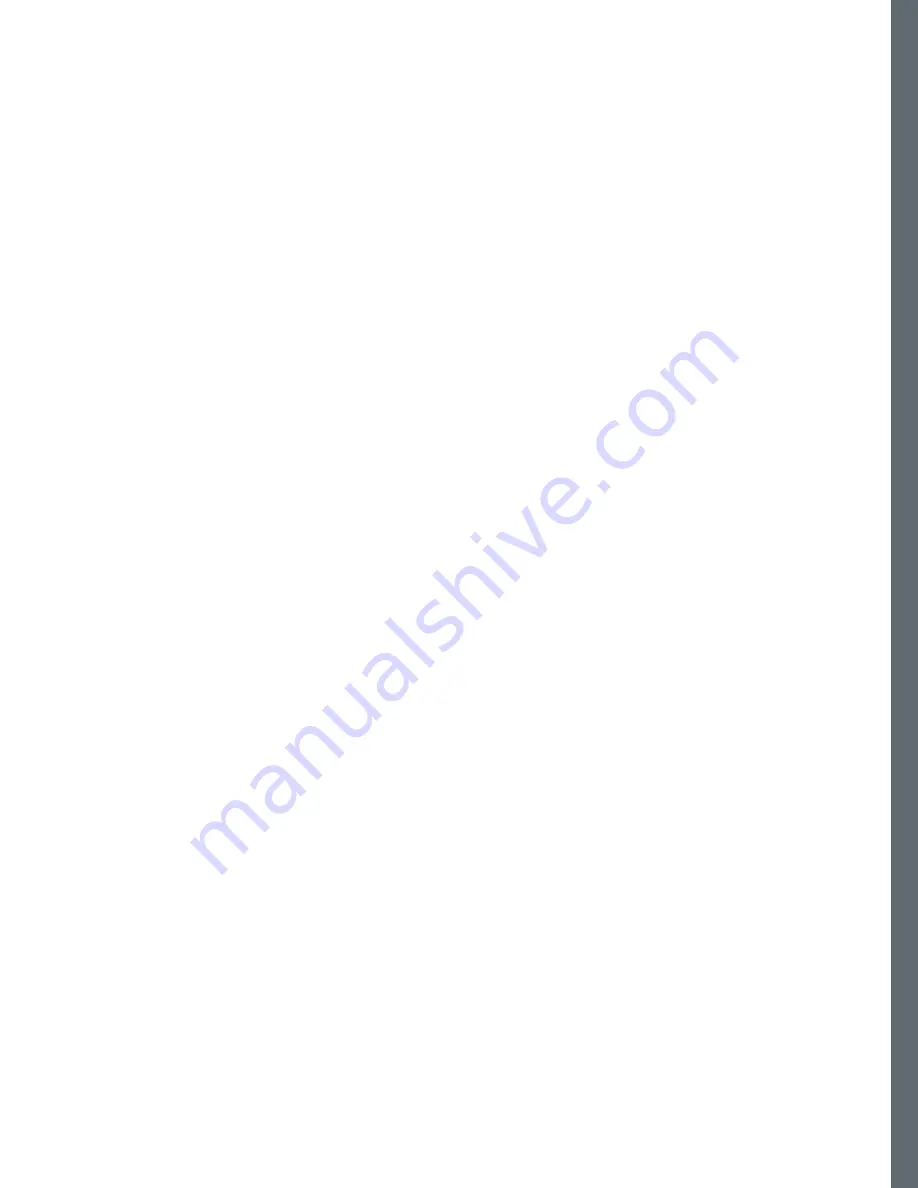
www.alemitecarbonshield.com
ALEMITE CARbON SHIELD SERvICE SHEET | 31
Oil Related Alarms
1. check oil screw – Issued when the PLC detects
a 2% change in the input from the vacuum
sensor but no change in mist pressure, oil level
or oil temperature has been detected. This alarm
warns the user that a change in the oil vacuum
and potentially the oil consumption has occurred.
Determining the magnitude of this change is
outside of the scope of the Carbon Shield control
system design. The end user should investigate
the situation and take corrective action. If the
change is determined to be acceptable, the end
user can clear this alarm using the Adaptive
Mode function. This alarm can also be triggered
when draining the reservoir while the unit is
running. There is a time delay of 5 seconds
before the alarm is issued.
2. oil temp Alarm Hi – Issued when the oil
thermocouple detects an oil temperature above
170°F (76.7 degrees C). There is no time delay.
3. oil temp Alarm Lo – Issued when the oil
thermocouple detects an oil temperature
below 85°F (29.4 degrees C). There is no
time delay.
4. oil temp sensor fault – Issued when the oil
thermocouple input to the PLC indicates out
of the 4-20mA range. There is no time delay.
5. oil sensor fault – Level sensor input to the PLC
indicates to be out of the 4-20mA range. There
is no time delay.
6. oil LVL Alarm Lo – Issued when oil in the tank is
at about 0.25 gallons (0.95 L) of useful oil. There
is no time delay.
7. oil LVL Alarm Hi – Issued when tank is overfilled
by 0.25 inches (0.6 cm) above max. level. It may
indicate leaking oil solenoid or level sensor needs
calibration. See Start Up procedure in this manual
for level sensor calibration.
8. oil Refill Alarm, check oil Level/Refill Valve –
Issued when the PLC starts the oil refill system
and the oil level in the tank doesn’t increase
after 5 minutes.
Other Alarms
9. setup is not finished select setup Done –
Issued during the set up sequence to warn the
user that the Carbon Shield unit still requires
their input. This condition indicates that the
system is not ready to operate autonomously.
Содержание Carbon Shield
Страница 1: ...INSTALLATION OPERATION AND MAINTENANCE MANUAL ...
Страница 2: ......
Страница 4: ...2 www alemitecarbonshield com Fig 01 ...
Страница 5: ...Alemite Carbon Shield Service Guide 3 www alemitecarbonshield com Fig 02 ...
Страница 39: ...Alemite Carbon Shield Service Guide 37 www alemitecarbonshield com ...
Страница 53: ...Alemite Carbon Shield Service Guide 51 www alemitecarbonshield com Wiring Diagrams Relay Wiring Fig 92 Fig 92 ...
Страница 57: ...References Installed Arrangement Fig 95 Fig 95 www alemitecarbonshield com ...