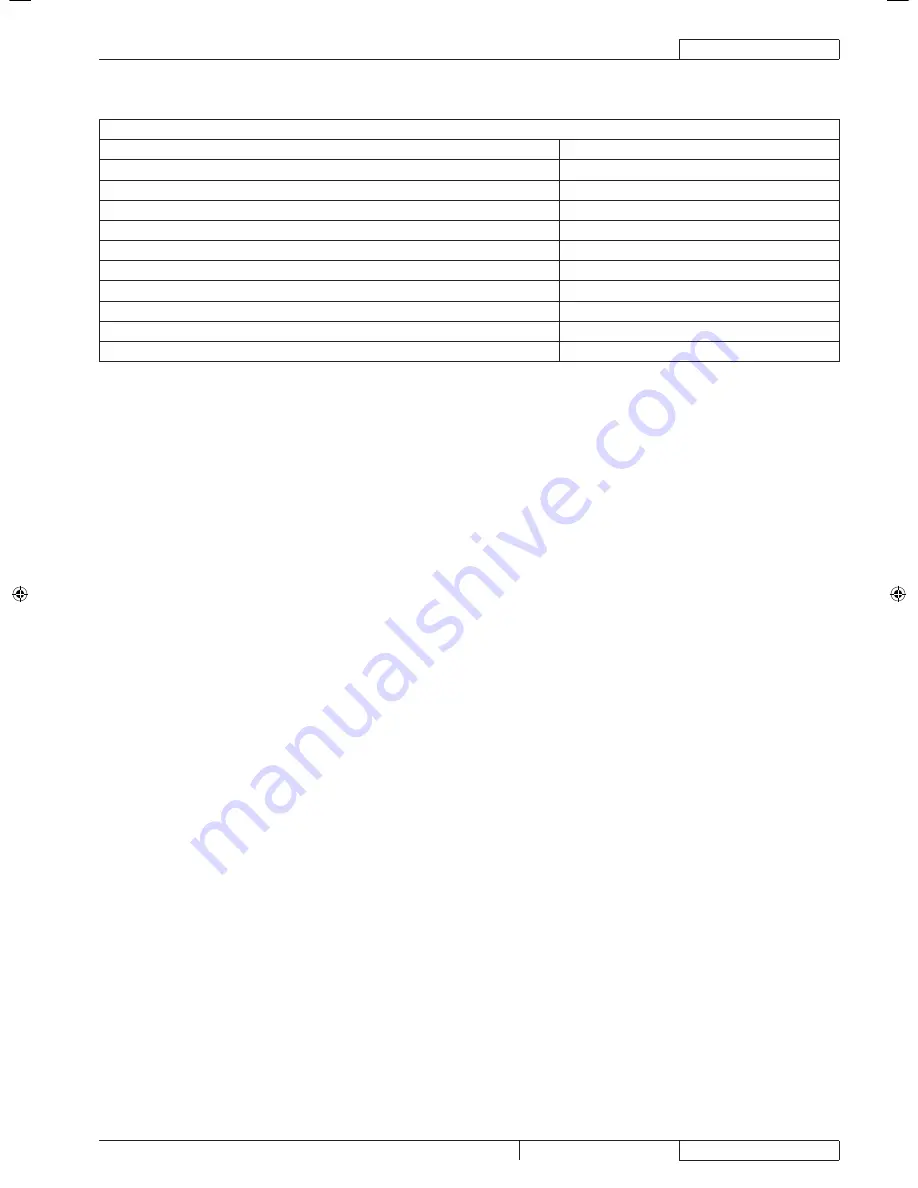
GENERAL INFORMATION
SERVICE MANUAL
ENGLISH
SC3000 26” Disc
9099052000
7
TECHNICAL DATA (Continues)
Technical data for machines with brush/pad-holder deck
Description
SC3000 26” Disc
Brush/pad diameter
13 in (330 mm)
Weight without batteries and with empty tanks
385.8 lb (175 kg)
Maximum weight with batteries, full tanks and operator (GVW)
983.2 lb (446 kg)
Hourly efficiency [2,5 mi/h (4 km/h)]
~ 24488 ft
2
(~ 2,275 m
2
)
Deck right/left offset (variable)
0 ÷ 3,9 in / 1 ÷ 0 in (0 ÷ 100 mm / 25 ÷ 0 mm)
Brush distance from the floor (when lifted)
1,9 in (48 mm)
Brush/pad motor power
2 x 0.53 hp (2 x 400 W)
Brush/pad-holder speed
230 rpm
Brush/pad-holder pressure with extra-pressure function turned off
66.1 lb (30 kg)
Brush/pad-holder pressure with extra-pressure function turned on
105.8 lb (48 kg)
A2 ENGLISH(2).indd 7
29/07/2011 17.02.31
Содержание SC3000 26" Disc
Страница 2: ......
Страница 28: ...BRUSHING SYSTEM ENGLISH SERVICE MANUAL 26 9099052000 SC3000 26 Disc WIRING DIAGRAM P100384A ...
Страница 35: ...RECOVERY WATER SYSTEM SERVICE MANUAL ENGLISH SC3000 26 Disc 9099052000 33 WIRING DIAGRAM P100387A ...
Страница 36: ...RECOVERY WATER SYSTEM ENGLISH SERVICE MANUAL 34 9099052000 SC3000 26 Disc ...
Страница 39: ...PARKING BRAKE SYSTEM SERVICE MANUAL ENGLISH SC3000 26 Disc 9099052000 37 WIRING DIAGRAM P100389A ...
Страница 40: ...PARKING BRAKE SYSTEM ENGLISH SERVICE MANUAL 38 9099052000 SC3000 26 Disc ...
Страница 48: ...DRIVE SYSTEM ENGLISH SERVICE MANUAL 46 9099052000 SC3000 26 Disc WIRING DIAGRAM P100393A ...
Страница 68: ...ELECTRICAL SYSTEM ENGLISH SERVICE MANUAL 66 9099052000 SC3000 26 Disc WIRING DIAGRAM Continues P100403A ...
Страница 69: ......