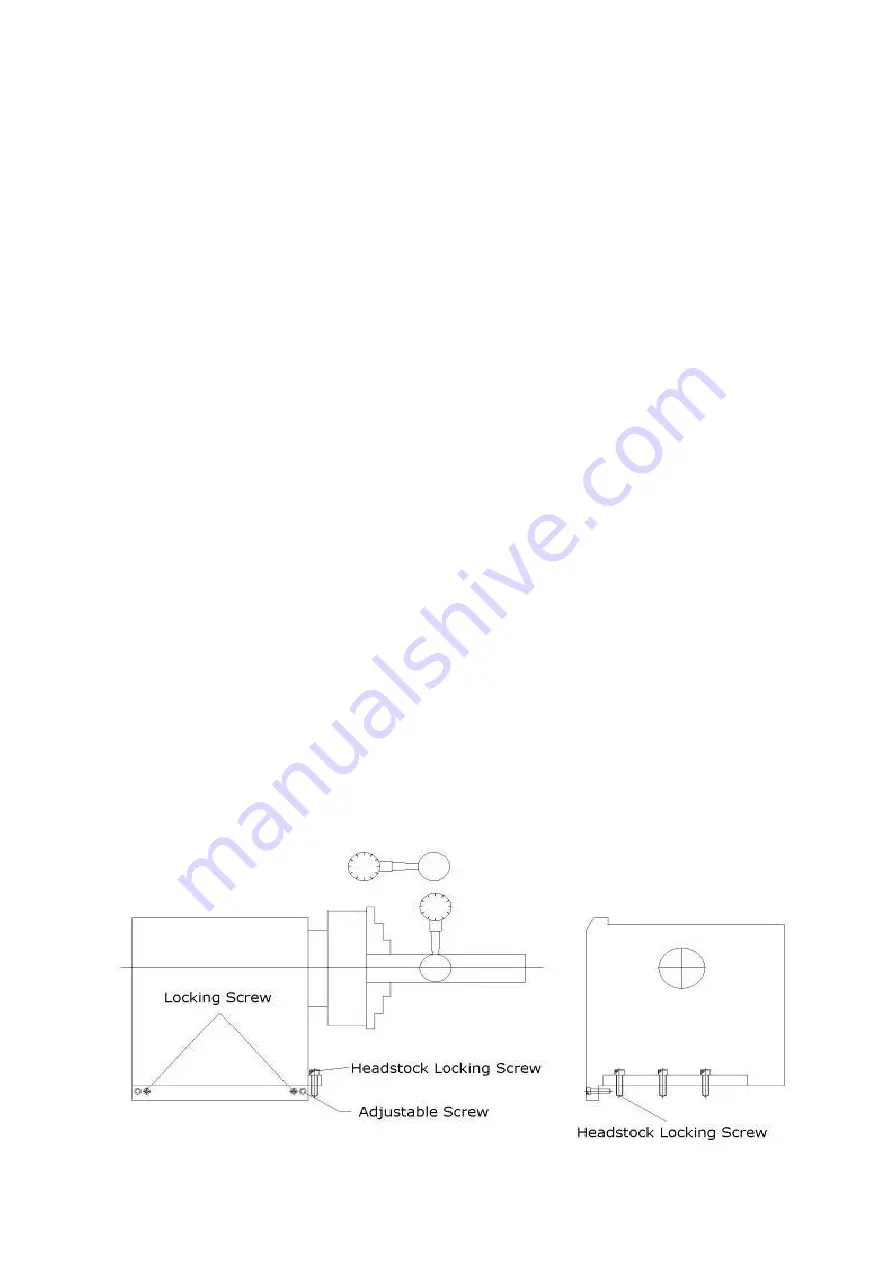
Page 4-2
9) Keep adding new lubricant into the lubricant tank to sustain the lubricant
level.
10) After a while, turn off the lathe and the spindle. Disconnect the escape hose
from the container, and then connect back to the lubricant tank.
4.1.2
Fittings
Check all fittings after 500 hours of operation especially their tightness between
tubes. After that, do the regular check every 200 hours.
4.2 Machine body
In order to maximize the machine performance, the accuracy on headstock and
all slides have to be re-adjust after three months of operation. After that,
re-adjust every six months to one year to keep the machine in best accuracy.
4.2.1 Aligning headstock
lf taper appears on turning work piece and convex on rounding, adjust the
parallel of headstock by following steps
1)
Insert gauge bar in the spindle bore. Attach the base of test indicator to the
tool post. Apply the stylus of the indicator to the outer diameter of the bar.
Move the saddle along Z axis and measure the maximal difference.
2)
If the pointer of the in indicator swings drastically, release the headstock
fixing screws and adjusting the adjusting to fine the paralleled of spindle and
Z axis
3)
After adjustment, tighten the fixing screws and move the saddle to observe
the pointer of the indicator.
Содержание ATL 1820E
Страница 5: ...1 SAFETY INSTRUCTIONS ...
Страница 22: ...Page 1 17 ...
Страница 24: ...2 MACHINE SPECIFICATIONS ...
Страница 25: ...Page 2 1 2 MACHINE SPECIFICATIONS 2 1 Dimensional drawing ...
Страница 27: ...Page 2 3 2 1 2 Chip Conveyor ...
Страница 31: ...3 INSTALLATION ...
Страница 34: ...3 1 2 Layout floor plan Following is a top view drawing ...
Страница 43: ...4 MAINTENANCE ...
Страница 55: ...5 CHUCK ...
Страница 64: ...Page 7 3 7 1 HEADSTOCK 1 HEADSTOCK _ 18 SPINDLE BORE 58mm 2 ...
Страница 65: ...Page 7 4 18 SPINDLE BORE 58mm 2 ...
Страница 69: ...Page 7 8 7 2 BED Z AXIS TRANSMISSION ...
Страница 71: ...Page 7 10 7 3 CARRIAGE CROSS SLIDE ...
Страница 74: ...Page 7 13 7 4 TAILSTOCK MANUAL TAILSTOCK _ 18 ...