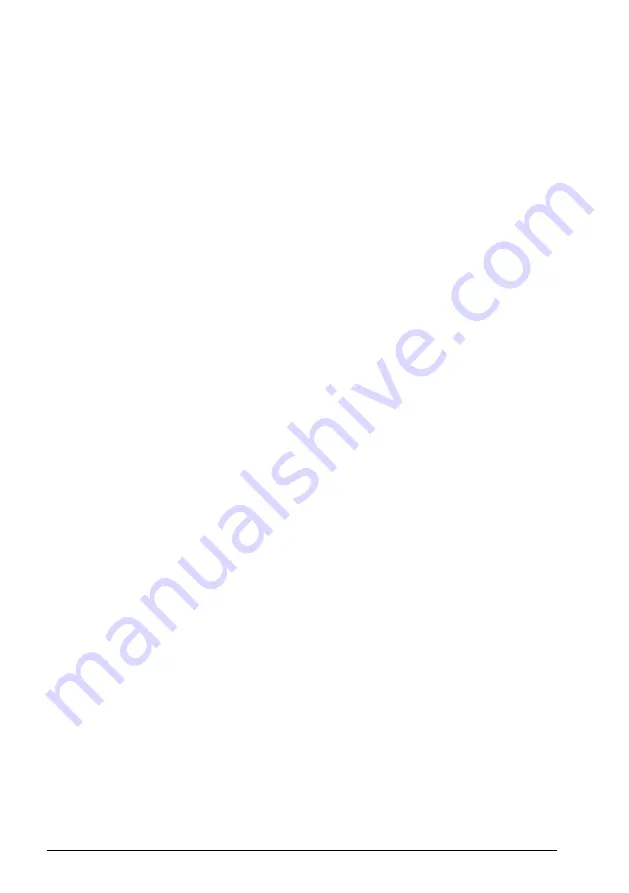
Maintenance
After the operation of the circuit is validated at start-up, the STO function shall be
maintained by periodic proof testing. In high demand mode of operation, the maximum
proof test interval is 20 years. In low demand mode of operation, the maximum proof
test interval is 5 or 2 years; see section
. It is assumed that all
dangerous failures of the STO circuit are detected by the proof test. To perform the
proof test, do the
Validation test procedure (page 216)
.
Note:
See also the Recommendation of Use CNB/M/11.050 (published by the European
co-ordination of Notified Bodies) concerning dual-channel safety-related systems with
electromechanical outputs:
• When the safety integrity requirement for the safety function is SIL 3 or PL e (cat. 3
or 4), the proof test for the function must be performed at least every month.
• When the safety integrity requirement for the safety function is SIL 2 (HFT = 1) or
PL d (cat. 3), the proof test for the function must be performed at least every 12
months.
The STO function of the drive does not contain any electromechanical components.
In addition to proof testing, it is a good practice to check the operation of the function
when other maintenance procedures are carried out on the machinery.
Include the Safe torque off operation test described above in the routine maintenance
program of the machinery that the drive runs.
If any wiring or component change is needed after start-up, or the parameters are
restored, do the test given in section
Validation test procedure (page 216)
Use only spare parts approved by ABB.
Record all maintenance and proof test activities in the machine logbook.
■
Competence
The maintenance and proof test activities of the safety function must be carried out by
a competent person with adequate expertise and knowledge of the safety function as
well as functional safety, as required by IEC 61508-1 clause 6.
220 The Safe torque off function
Содержание ACS880-11
Страница 1: ... ABB INDUSTRIAL DRIVES ACS880 11 drives Hardware manual ...
Страница 2: ......
Страница 4: ......
Страница 26: ...26 ...
Страница 52: ...52 ...
Страница 82: ...82 ...
Страница 95: ...R6 R8 IP21 R6 R8 IP55 Electrical installation IEC 95 ...
Страница 103: ...R6 1 5 N m 0 5 N m Electrical installation IEC 103 ...
Страница 104: ...R8 1 5 N m 0 5 0 6 N m 104 Electrical installation IEC ...
Страница 112: ...With FDPI 02 modules OPEN TERMIN ATED 1 1 2 2 OPEN TERMINATED 3 112 Electrical installation IEC ...
Страница 116: ...R6 R8 UL Type 1 R6 R8 UL Type 12 116 Electrical installation North America NEC ...
Страница 120: ...R3 7 7 8 8 L1 L2 L3 T1 U T2 V T3 W PE Ground 1 7 N m 1 2 lbf ft 120 Electrical installation North America NEC ...
Страница 142: ...142 ...
Страница 154: ... Fan arrow must point up 154 Maintenance ...
Страница 160: ...160 ...
Страница 181: ... Package dimensions R6 R3 R8 Technical data 181 ...
Страница 202: ...R3 IP21 UL Type 1 3AXD50000045323 202 Dimension drawings ...
Страница 203: ...R3 Option B056 IP55 UL Type 12 3AXD50000045322 Dimension drawings 203 ...
Страница 204: ...R6 IP21 UL Type 1 3AXD50000045353 204 Dimension drawings ...
Страница 205: ...R6 Option B056 IP55 UL Type 12 3AXD50000045352 Dimension drawings 205 ...
Страница 206: ...R8 IP21 UL Type 1 3AXD50000047667 206 Dimension drawings ...
Страница 207: ...R8 Option B056 IP55 UL Type 12 3AXD50000047667 Dimension drawings 207 ...
Страница 208: ...208 ...
Страница 225: ... Declarations of conformity The Safe torque off function 225 ...