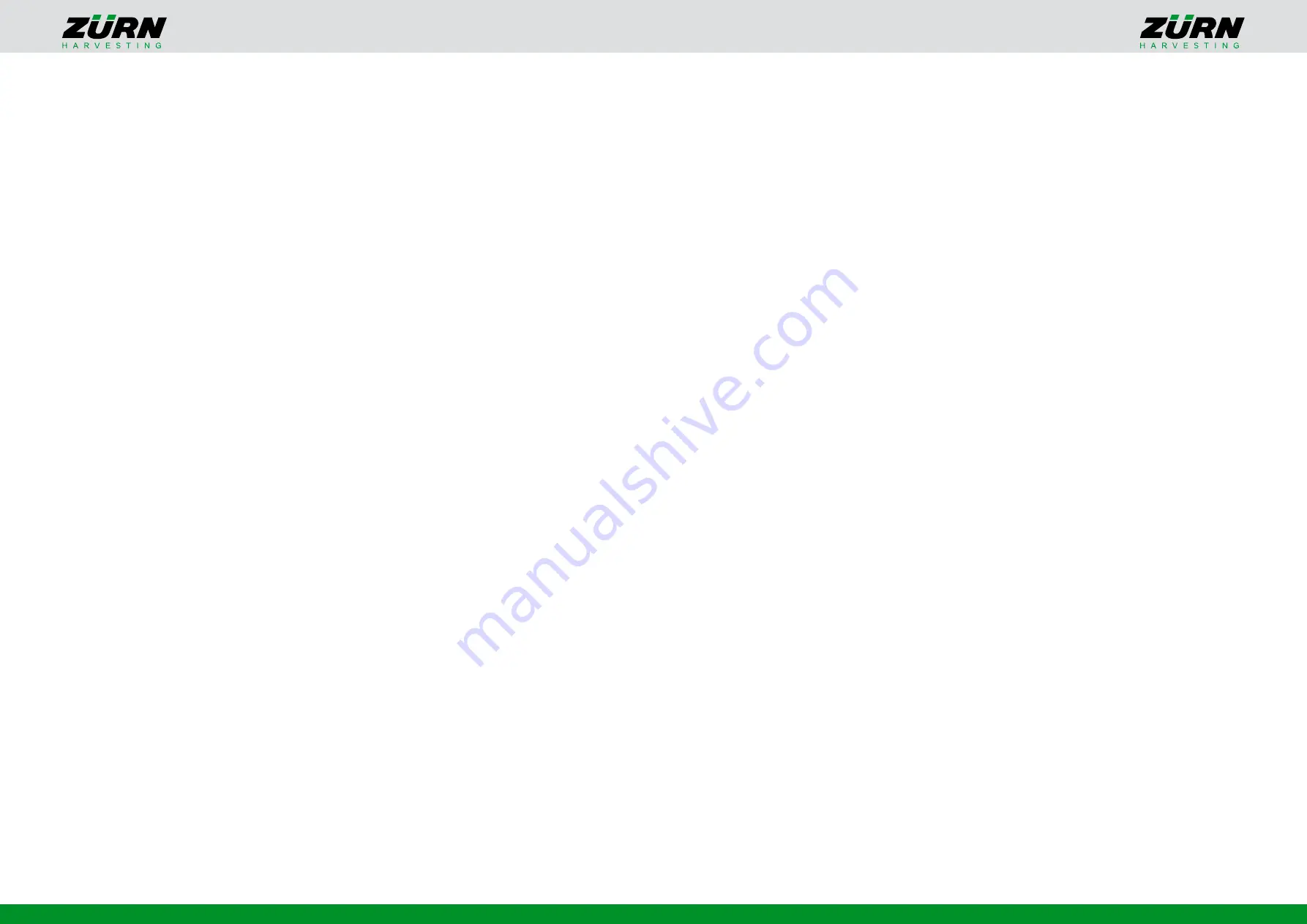
50/52 | Operation manual Z130-SE | 05/2016
51/52 | Operation manual Z130-SE | 05/2016
then set to full load
• Correctly adjust belt tensioning device
13.13. Unsatisfactory threshing out
• Adjust threshing concave closer
• Increase cylinder speed
• Correct basic adjustment of the threshing
concave
• Clean dirty threshing elements
• Have worn or damaged threshing elements
repaired
• Fit de-awner bars
13.14. Machine imbalance
• Clean dirty threshing cylinder
• Remove accumulations of dirt in the belt
pulleys
• Renew damaged threshing cylinder blocks
• Check sieve and shaker for wear and
fracture
13.15. Broken grains
• Reduce threshing cylinder speed
• Adjust threshing concave further away
• Use fewer de-awner bars
13.16. Uneven loading of the sieve
• Check belt for damage
• Clean inlet belt conveyor
• Check belt tension
• Check belt roller bearings
13.17. Sieve case bangs
• Tighten all sieve case fastening bolts
• Check sieve fastening
• Have sieve case bearings renewed
• Check sieve case and shaker drive for wear
and fracture
13.18. Excessive mat formation on
the lamella sieve / messy grain
• More wind
• Adjust wind baffles
• Reduce threshing cylinder speed
• Adjust threshing concave further away
• Adjust lamella sieve opening further away
13.19. Grain tank discharge does
not work
• Check curved auger flights and repair if
necessary
• If necessary adjust slider position at grain
tank auger cover
• Have hydraulic oil pressure checked
14. Technical data
14.1. Header
• Cutting width 1.25 m / 1.50 m / 1.75 m /
2.0 m
• Knife drive hydraulic
• Feeding auger and transfer roller
• Blow-out device
• Crop divider
• Crop lifter
• Depth control using sliding skids and hea-
der load relief springs
14.2. Reel
• 4-piece reel with hydraulic drive
• Hydraulic reel speed adjustment
• Hydraulic reel height adjustment
• Mechanical reel horizontal adjustment
(optionally also hydraulic)
• Brush bars (optional)
14.3. Threshing cylinder
• Ø 350 mm
• Width 780 mm
• 6 impact bars
• Manual, electrically adjustable variator
14.4. Threshing concave
• 10 concave bars
• 118° wrapping angle
• 0.31 m
2
cutting area
• 4 de-awner bars can be inserted from the
side
• Concave adjustment from the driver’s seat
14.5. Shaker
• Shaker area 1.8 m
2
• 3 active steps
14.6. Cleaning
• Continuously adjustable, hydraulically
driven cleaning blower
14.7. Sieve
• Upper sieve: adjustable lamella sieve
• Under sieve: round hole sieve
• Total sieve area (with double sieve) 2 m
2
• Oscillating sieve case
• Double injection point
14.8. Corn conveyance
• Pneumatic conveying system
• Grain transport via cyclone to side bag-
ging system or to the optional grain tank,
or to the optional weighing system
14.9. Grain tank (optional)
• 450 / 600 litre
• Can be folded to the rear for grain-free
cleaning
• Loading height of the grain tank pipe
2.60m
• Hydraulically folding grain tank discharge
pipe
14.10. Engine
• 36kW John Deere or Yanmar engine
• 4 cylinder
• Water-cooled
• 60-litre fuel tank
14.11. Propulsion
• Hydrostatic propulsion with wheel hub
motors
• Inch pedal (foot pedal) for stop-and-go
operation
• 2 vehicle speed ranges, continuously adjus-
table from 0-10 km/h, or from 0-20 km/h
14.12. Steering
• Hydraulic steering