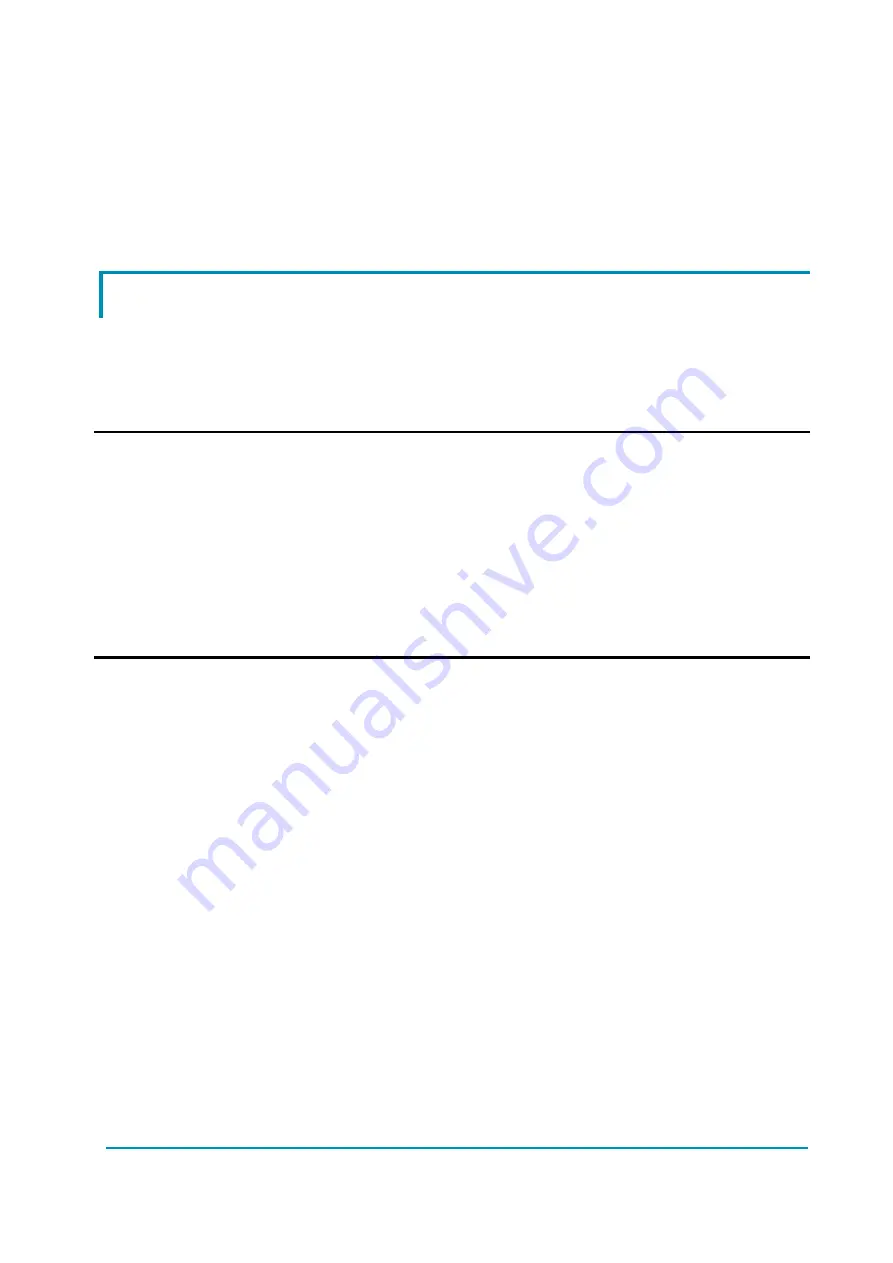
AF9ZP0BA - EPS-ACW REACH TRUCK - User Manual
Page - 63/90
15 EPSACW ALARMS
The list of the alarms occurring in the epsacW is listed in 15.2.
When an alarm occurs, traction must be brought to a controlled safe state. This
activity IS FULLY IN CHARGE OF THE LIFTTRUCK MANUFACTURER. Refer to
15.1 for the details.
15.1 Stop Traction when epsacW is no longer operative
In case of an alarm in the epsacW, the traction must be brought to a controlled
safe state (traction stop or traction speed limitation). The epsacW invokes this
event with a STOP TRACTION REQUEST sent on the CAN Bus communication
system. An optional hardwired output (CNA#14) is available too (optional and
activated only on a customer’s demand).
U
Whenever at least one of the two microcontrollers in the epsacW detects an
alarm in the steering system, that microcontroller turns on (from LOW to
HIGH) a STOP TRACTION REQUEST bit in a PDO (STATUS WORD)
continuously sent to the unit designated to stop the traction.
The job in the Zapi steering system finishes when the STOP TRACTION
REQUEST has been sent. So the Lifttruck Manufacturer is responsible for
coordinating the communication between different units in the truck and
furthermore for testing and validating that this alarm information will be
properly handled in the destination unit and leading to a traction safe state
when the steering system is no longer operative.
Let us call the unit in the truck designated to lead the traction in a safe state
(whatever it is) as the Traction Master Control (TMC).
TMC is expected to continuously send a PDO (used as a synchronization frame) to
the epsacW:.
TMC -> EPS_MuC_SuC (synch like frame)
The two uCs inside the epsacW must answer.
1) EPS_MuC - > TMC
AND
2) EPS_SuC - > TMC
These response PDOs includes the STOP TRACTION REQUEST bit.
The time repetition for this (synch) PDO TMC -> EPS_MuC_SuC MUST BE
LOWER EQUAL THAN 32msec.
TMC - > EPS_MuC_SuC: Every Tr <= 32msec
EPS_MuC - > TMC:
MuC STOP TRACTION REQUEST
EPS_SuC - > TMC:
SuC STOP TRACTION REQUEST
The job in the Zapi steering system finishes when the STOP TRACTION
REQUEST has been sent to the TMC. The position of the STOP TRACTION
REQUEST flag is given by table 15.1-1 below: