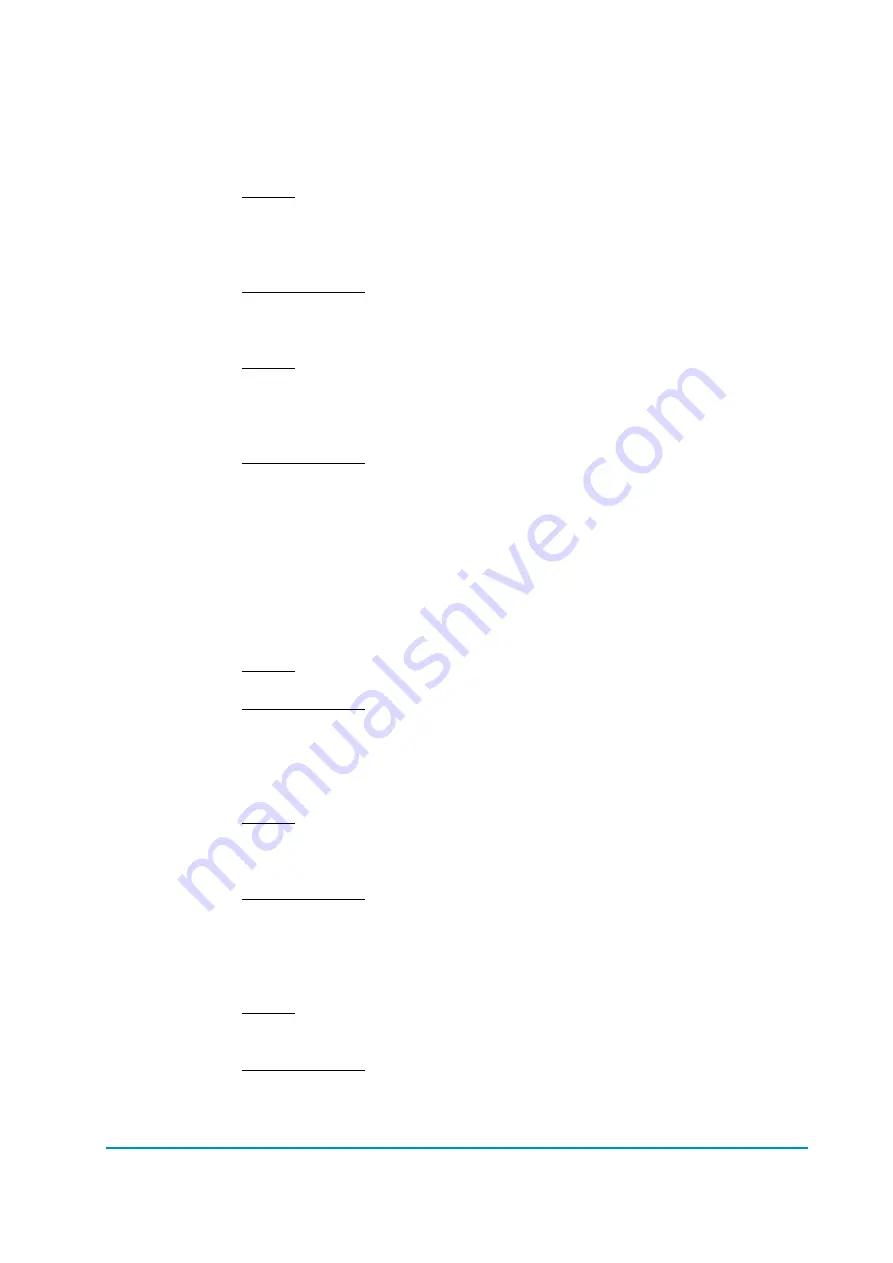
AF6ZP0AL - COMBIAC0 & ACE0 - User Manual
Page - 65/79
same value as the battery voltage measured with a voltmeter. If it is does
not match, then do a “ADJUST BATTERY” function.
C) Replace the battery.
18) “ANALOG INPUT”
Cause:
This alarm occurs when the A/D conversion of the analog inputs gives frozen
value, on all of the converted signals, for more than 400msec. The goal of
this diagnosis is to detect a failure of the A/D converter or a problem in the
code flow that omits the refreshing of the analog signal conversion.
Troubleshooting:
If the problem occurs permanently it is necessary to substitute the controller.
19) “ENCODER ERROR”
Cause:
This fault is signalled in following conditions: the frequency supplied to the
motor is higher than 40 Hz and the signal feedback from the encoder has a
jump higher than 40 Hz in few tens mSec. This condition is related to a
malfunctioning of the encoder.
Troubleshooting:
A) Check both the electric and the mechanical encoder functionality, the
wires crimping.
B) Check the encoder mechanical installation, if the encoder slips inside its
compartment raising this alarm condition.
C) Also the electromagnetic noise on the sensor bearing can be a cause for
the alarm. In these cases try to replace the encoder.
D) If the problem is still present after replacing the encoder, the failure is in
the controller.
20) “TILLER ERROR”
Cause:
Mismatch between the H&S input and the tiller input.
Troubleshooting:
Check the harness related to CAN#1 and CAN#29 with a voltmeter. If the
state of these inputs is right, then it could be a problem inside the controller,
which has to be changed.
21) “WATCHDOG”
Cause:
This is a safety related test. It is a self diagnosis test within the logic. The
watch dog circuit is composed by two monostable multivibrators so there is a
double check of software execution.
Troubleshooting:
This alarm could be caused by an hardware failure in one of two (or both)
multivibrator or due to a software execution problem. For both cases it is an
internal fault of the controller which must be replaced.
22) “SMART DRIVER KO”
Cause:
The built in smart driver is open, not able to provide the electro mechanic
brake positive.
Troubleshooting:
A) It is suggested to check the harness, in order to verify if the Smart driver
output CNA#2 is shorted to –Batt.
B) If, even disconnecting the wire from the connector pin, the output stays at