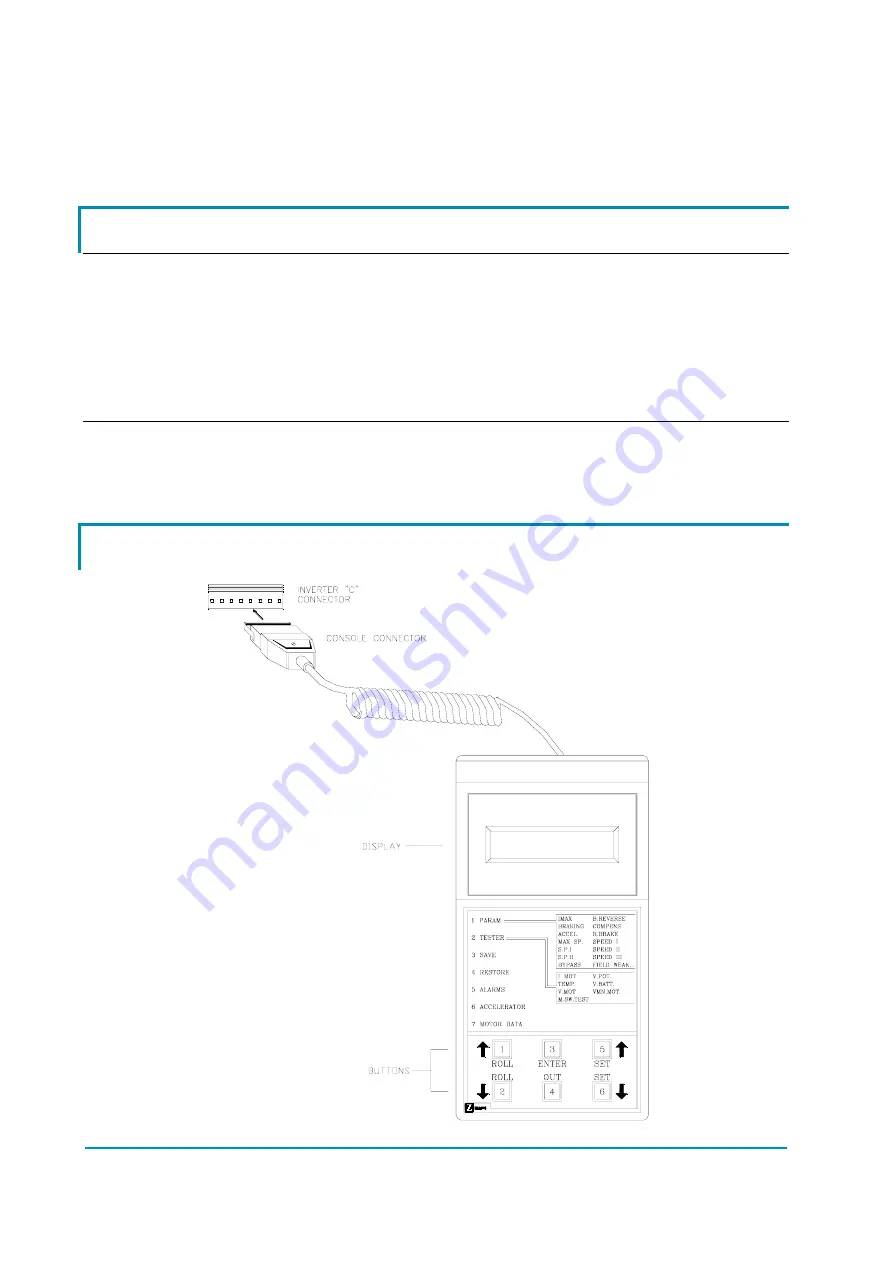
Page - 32/79
AF6ZP0AL - COMBIAC0 & ACE0 - User Manual
10 PROGRAMMING & ADJUSTMENTS
USING DIGITAL CONSOLE
10.1 Adjustments via console
4
To access and adjust all parameters it is necessary to use the Zapi console.
Since the COMBIAC0/ACE0 has no external serial connector, the Zapi console
has to be connected through a remote module, like a Zapi tiller card of a Zapi
display. This module has to be connected to the same Canbus line of the
inverter.
Otherwise it is possible to connect a pc to the Canbus line and use the PC CAN
Console software. This tool is more powerful than the standard serial console.
The following paragraphs describe the controller configuration in the case the
operator is using the Zapi console.
10.2 Description of console (hand set) & connection