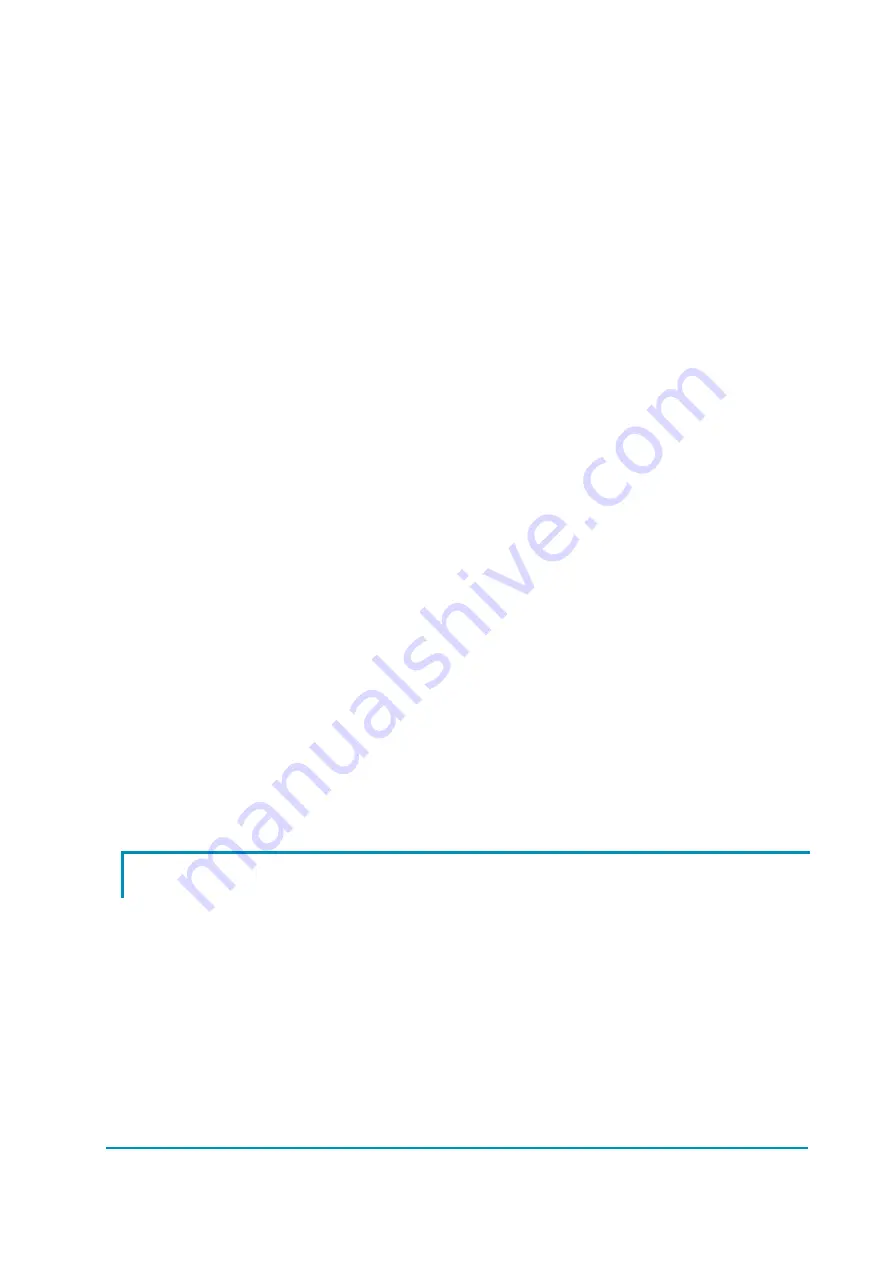
AF2ZP0CL - ACE2 - User Manual
Page - 25/85
connected to -Batt.
A14
ENCB
Incremental encoder phase B input.
A15
ENC GND
Encoder negative power supply.
A16
NLC
Main contactor coil output. The coil is driven to
negative reference.
A17
PLC/PAUX
Positive of the LC and Auxiliary coil.
A18
NAUX
Auxiliary coil output. The coil is driven to negative
reference.
A19 SAFETY OUT
In the COMBI configuration it is connected to SAFETY
IN (CNA#11) of traction controller.
It can also be used to drive an external load to
negative reference when the pump motor is driven.
The maximum current load is 1 A. In case of inductive
load it is suggested to use a free-wheeling diode
across the load (with cathode connected to +Batt)
A20
CAN-L
Low level CAN-BUS voltage I/O.
A21
CAN-H
High level CAN-BUS voltage I/O.
A22
PTHERM
Input for motor temperature sensor. It is possible to
use a digital or analogue (PTC) sensor.
A23 NTHERM
-Batt.
B1
PCLRXD
Positive serial reception (Not used: it can be
disconnected).
B2
NCLRXD
Negative serial reception.
B3
PCLTXD
Positive serial transmission.
B4
NCLTXD
Negative serial transmission.
B5
GND
Negative console power supply.
B6
+12
Positive console power supply.
B7
FLASH
It must be connected to B8 for the Flash memory
programming.
B8
FLASH
It must be connected to B7 for the Flash memory
programming.
6.3 Description of power connections
View of the power bars:
-BATT
Negative of the battery.
+BATT
Positive of the battery.
U; V; W
Connection bars of the three motor phases; follow this
sequence and the indication on the motor.
Summary of Contents for ACE2
Page 7: ...AF2ZP0CL ACE2 User Manual Page 7 85 2 3Block diagram...
Page 28: ...Page 28 85 AF2ZP0CL ACE2 User Manual 7 3Connection drawing Traction configuration...
Page 29: ...AF2ZP0CL ACE2 User Manual Page 29 85 7 4Connection drawing Pump configuration...
Page 30: ...Page 30 85 AF2ZP0CL ACE2 User Manual 7 5Connection drawing Combi configuration...
Page 33: ...AF2ZP0CL ACE2 User Manual Page 33 85 8 3 2 Pump configuration...