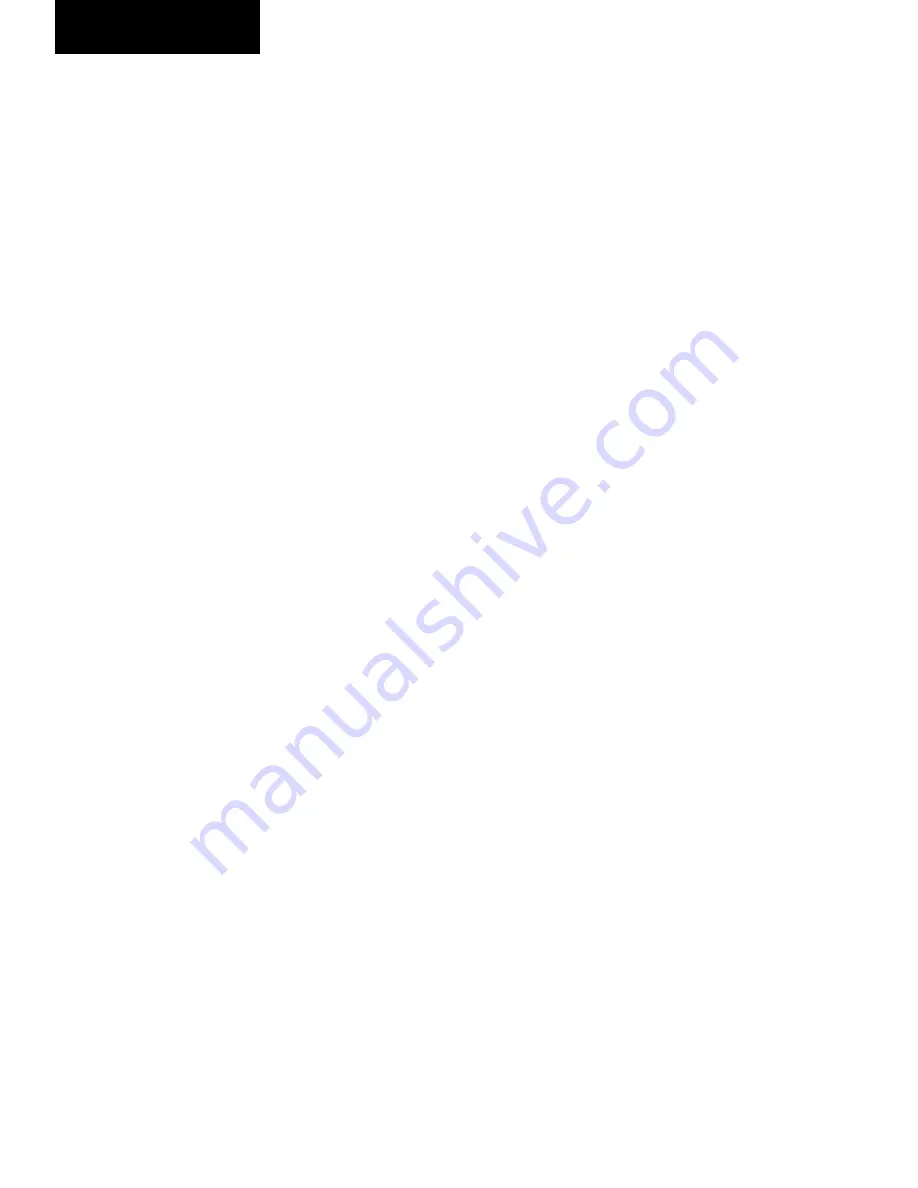
14
YORK INTERNATIONAL
FORM 201.19-NM1 (204)
stag gered rows and mechanically expanded into cor ro sion
resistant aluminum alloy
fi
ns with full height
fi
n col lars.
They have a design working pressure of 450 PSIG
(31 bar). Each coil is rested to 495 PSIG (34 bar).
Multiple fans move air through the coils. They are
dy nam i cal ly and statically balanced, direct drive with
cor ro sion re sis tant glass
fi
ber reinforced composite
blades mold ed into low noise, full airfoil cross section,
pro vid ing vertical air discharge from extended ori
fi
ces
for ef
fi
cien cy and low sound. Each fan is located in a
sep a rate com part ment to prevent cross
fl
ow during fan
cy cling. Guards of heavy gauge, PVC coated galvanized
steel are pro vid ed.
The fan motors are high ef
fi
ciency, direct drive, 6-pole,
3-phase, Class- “F,” current overload protected, totally
en closed (TEAO) type with double sealed, per ma nent ly
lubricated ball bearings.
Economizer
Economizer is a refrigerant to refrigerant, compact plate-
type heat exchanger to maximize chiller capacity and
ef
fi
ciency by subcooling liquid refrigerant delivered to
the cooler expansion valve. Constructed of corrosion
resistant stainless steel plates formed to induce turbulent
fl
ow and enhance heat transfer, then oven brazed and
pressure tested for reliability. Designed and constructed
with ASME and TÜV certi
fi
cation for 31 bar (450 psig).
UL/CSA listed.
Oil Separator/System
The external oil separator, with no moving parts and
de signed for minimum oil carry-over, is mounted in
the dis charge line of the compressor. The high pressure
dis charge gas is forced around a 90 degree bend. Oil is
forced to the outside of the separator through cen trif u gal
action and captured on wire mesh where it drains to the
bottom of the oil separator and
fl
ows to the condenser
for cooling before returning to the compressor.
The oil (YORK “L” oil – a POE oil used for all re frig -
er ant applications), which
fl
ows back into the com-
pres sor through a replaceable 0.5 - 3.0 micron oil
fi
lter,
is at high pressure. This high pres sure “oil injection”
forces the oil into the com pres sor where it is fed to the
bearings for lubrication. After lubricating the bearings,
it is injected through ori
fi
ces on a closed thread near
the suction end of the rotors. The oil is automatically
in ject ed because of the pressure difference between the
discharge pres sure and the reduced pressure at the suc-
tion end of the rotors. This lubricates the rotors as well as
provides an oil seal against leakage around the ro tors to
assure re frig er ant compression (volumetric ef
fi
cien cy).
The oil also provides cooling by transferring much of
the heat of com pres sion from the gas to the oil keeping
dis charge tem per a tures down and reducing the chance
for oil breakdown. Oil injected into the rotor cage
fl
ows
into the ro tors at a point about 1.2x suction. This assures
that a required minimum differential of at least 30 PSID
(2.1 bar) exists between discharge and 1.2x suc tion, to
force oil into the rotor case. A minimum of 10 PSID
(0.6 bar) is all that is re quired to assure pro tec tion of
the compressor. Oil pressure safety is mon i tored as the
dif fer ence between suction and the pres sure of the oil
en ter ing the ro tor case.
Maximum working pressure of the oil separator is 450
PSIG (31 bar). Oil level should be above the midpoint
of the “low er” oil sight glass when the compressor is
run ning. Oil level should not be above the top of the
“up per” sight glass.
Oil Cooling
Oil cooling is provided by routing oil from the oil sep a -
ra tor through several of the top rows of the con dens er
coils and back to the compressor.
Capacity Control
The compressors will start at the minimum load po si tion
and provide a capacity control range from 10% - 100%
of the full unit load using a continuous function slide
valve. The microprocessor modulates a voltage signal to
a 3-way pres sure reg u lat ing capacity control valve which
controls com pres sor capacity, in de pen dent of system
pressures, and balances the com pres sor ca pac i ty with
the cool ing load. Loading is ac com plished by varying
pressure through the pressure regulating ca pac i ty control
valve to move the slide valve against the spring pressure
to promote stable smooth loading.
Automatic spring return of the slide valve to the min-
i mum load position will ensure compressor start ing at
min i mum motor load.
Power and Control Panel
All controls and motor starting equipment are factory
wired and function tested. The panel enclosures are
de signed to IP55 and are manufactured from powder
paint ed galvanized steel.
The Power and Control Panel are divided into power
sec tions for each compressor and associated fans, a con-
trol section and an electrical options section. The pow er
and control sections have separate hinged, latched, and
gasket sealed doors equipped with wind struts.
Product Description
Summary of Contents for YCAS0130
Page 45: ...45 YORK INTERNATIONAL FORM 201 19 NM1 204 5 This page intentionally left blank...
Page 47: ...47 YORK INTERNATIONAL FORM 201 19 NM1 204 6 This page intentionally left blank...
Page 63: ...63 YORK INTERNATIONAL FORM 201 19 NM1 204 This page intentionally left blank 7...
Page 73: ...73 YORK INTERNATIONAL FORM 201 19 NM1 204 LD09239 FIG 22B CONTROL PANEL COMPONENT LOCATION 7...
Page 75: ...75 YORK INTERNATIONAL FORM 201 19 NM1 204 7 LEGEND LD09241...
Page 77: ...77 YORK INTERNATIONAL FORM 201 19 NM1 204 7 CONNECTION DIAGRAM SYSTEM WIRING LD09242...
Page 78: ...78 YORK INTERNATIONAL FORM 201 19 NM1 204 Technical Data COMPRESSOR TERMINAL BOX LD09243...
Page 79: ...79 YORK INTERNATIONAL FORM 201 19 NM1 204 7 LD09373 ELEMENTARY DIAGRAM CONTROL CIRCUIT...
Page 81: ...81 YORK INTERNATIONAL FORM 201 19 NM1 204 7 This page intentionally left blank...
Page 121: ...121 YORK INTERNATIONAL FORM 201 19 NM1 204 7 This page intentionally left blank...
Page 193: ...193 YORK INTERNATIONAL FORM 201 19 NM1 204 8 This page intentionally left blank...