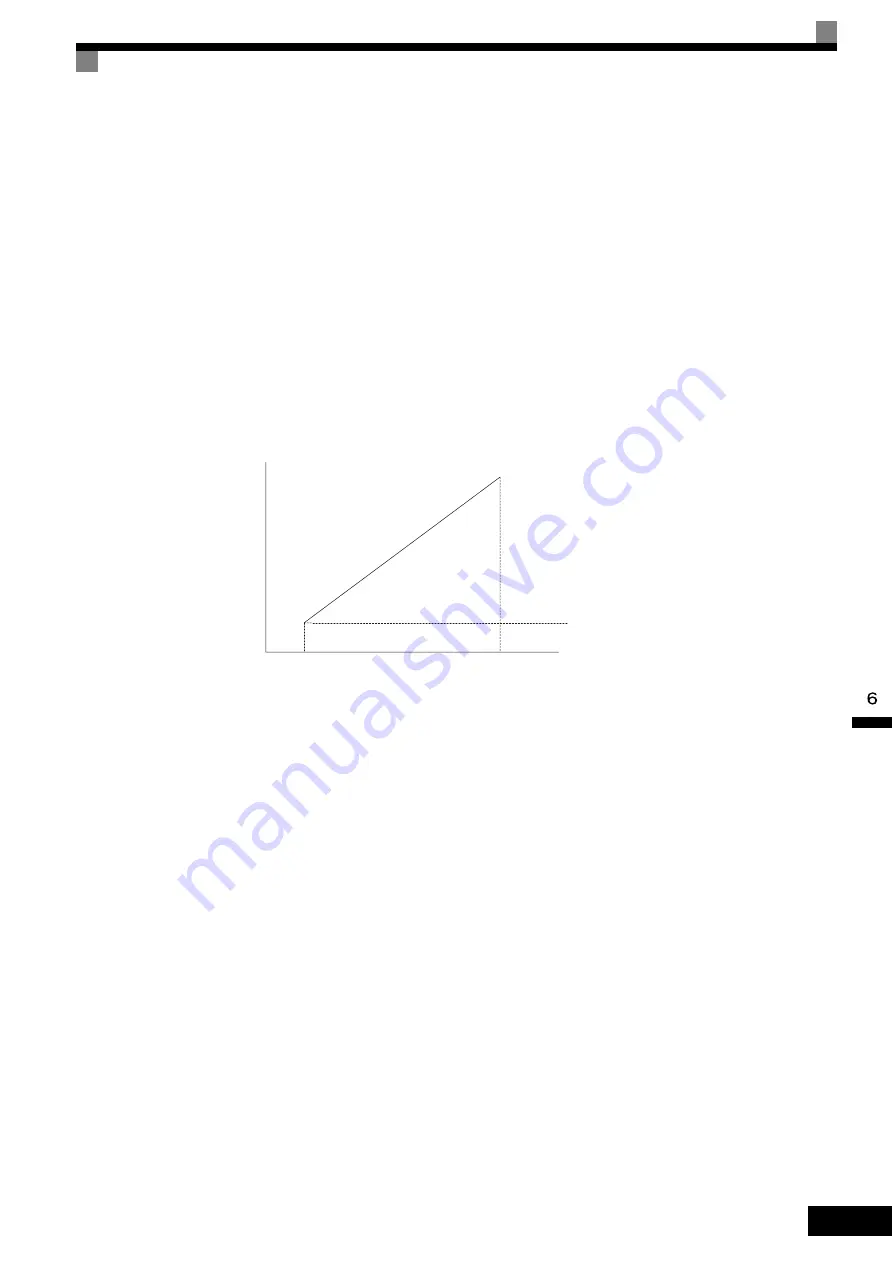
Individual Functions
6-
141
Precautions for Open-loop Vector 2 Control (PRG: 102
only)
•
The ASR primary delay time setting for open-loop vector 2 control is divided between constants C5-06
and C5-10. The constant that is used depends on the size of the operating frequency. If the operating fre-
quency is between 0 and 35 Hz, adjust the setting using C5-06, and if the operating frequency is greater
than 35 Hz, adjust the setting using C5-10.
•
To increase the speed response, adjust the gain with reference to the explanations on page 4-19 in
Chapter
4
Trial Operation
.
Gain Adjustment for Speed Control during V/f Control with PG
When using V/f control with PG, set the proportional gain (P) and the integral time (I) at E1-09 (minimum out-
put frequency) and E1-04 (maximum output frequency).
Speed Control Gain Integral Time Adjustment for V/f
Control with PG
shows how the proportional gain and integral time change in linear fashion based on the
speed.
Fig 6.76 Speed Control Gain Integral Time Adjustment for V/f Control with PG
Gain Adjustments at Minimum Output Frequency
Operate the motor at the minimum output frequency. Increase C5-03 (ASR proportional gain 2) to a level
where there is no oscillation. Decrease C5-04 (ASR integral time 2) to a level where there is no oscillation.
Monitor the Inverter's output current and verify that it is less than 50% of the Inverter rated current. If the out-
put current exceeds 50% of the Inverter's rated current, decrease C5-03 and increase C5-04.
Gain Adjustments at Maximum Output Frequency
Operate the motor at the maximum output frequency. Increase C5-01 (ASR proportional gain 1) to a level
where there is no oscillation. Decrease C5-02 (ASR integral time 1) to a level where there is no oscillation.
Fine Adjustments
When you want even finer gain adjustment, adjust the gain while observing the speed waveform. The adjust-
ment method is the same as that for vector control.
Enable integral operation during acceleration and deceleration (by setting F1-07 to 1) when you want the
motor speed to closely follow the frequency reference during acceleration and deceleration. Reduce the setting
of C5-01 if overshooting occurs during acceleration, and reduce the setting of C5-03 and increase the setting
of C5-04 if undershooting occurs when stopping. If overshooting and undershooting cannot be eliminated by
adjusting only the gain, reduce the value of C5-05 speed control and reduce the limit of the frequency refer-
ence compensation value.
P and I setting
Motor speed (Hz)
E1-04
Max. output frequency
0
P = C5-03
I = C5-04
P = C5-01
I = C5-02
E1-09
Min. output frequency