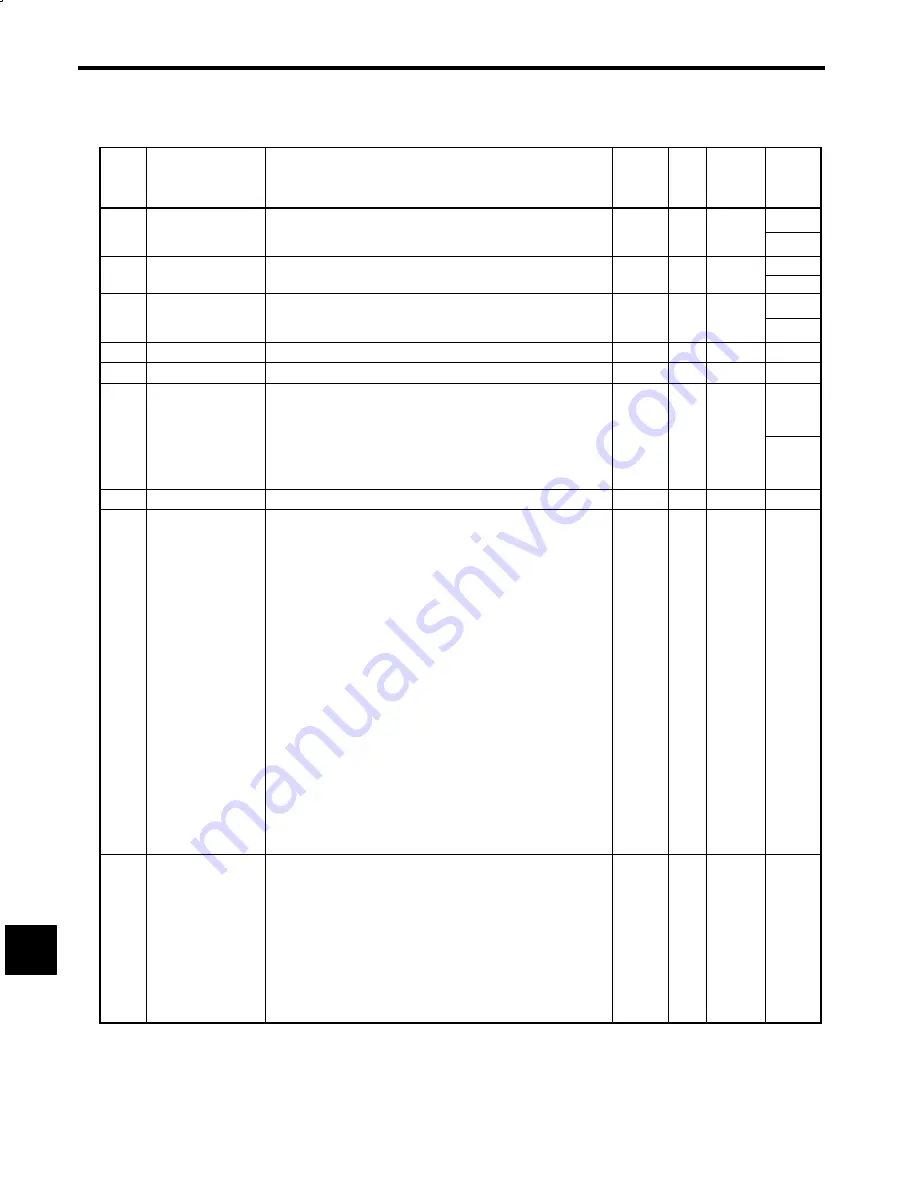
Control Constants
10
-12
Table 10.3
Magnetic Sensor Orientation Constants (continued)
Con-
stant
No.
Name
Explanation
Change
*
1
Unit Standard
Setting
Upper
Limit/
Lower
Limit
C3 15
Starting Soft Start
Time
Soft start time for accelerating from stop to orientation speed. Use this
parameter to reduce gear noise at starting
No
ms
0
50
C3-15
Time
T
SFO
parameter to reduce gear noise at starting.
Acceleration rate is (500 min
−
1
)/sec.
No
ms
0
0
C3 16
Flux Level
Flux level at completion of orientation. Motor noise and torque
h
i
i
fl
l
l
No
60
100
C3-16
φ
ORT
p
q
change in proportion to flux level.
No
---
60
15
C3 17
Orientation Speed
Reduction Coefficient
Reduction coefficient to set orientation speed in proportion to the
traveling angle for incremental positioning
No
0
32767
C3-17
Reduction Coefficient
K
SOR
traveling angle for incremental positioning.
No
---
0
0
C3 18
---
---
C3-18
---
---
---
---
---
---
C3 19
---
---
C3-19
---
---
---
---
---
---
C3 20
Sensor Signal Stan-
dardization Angle
θ
SEN
Angle for standardizing magnetic sensor signal detection sensitivity
θ
SEN
= 180
°×
Detection range (mm (inches))
÷
Mounting radius
÷ π
Set 20.0 to
θ
SEN when
θ
SEN
> 20.0.
F d
i
h k h
ifi i
f h
i
d
No
Deg
5 0
20.0
C3-20
For detection range, check the specifications of the magnetizer and
apply the values below:
MG-1378BS (15 mm (0.59 inches))
MG-1444S (7 mm (0.28 inches))
No
Deg.
5.0
5.0
C3 21
---
---
C3-21
---
---
---
---
---
---
C3 22
Orientation Control
Signal Selections 1
SEL-M1
*2
Control mode setting signals, e.g., for specifying the direction of
rotation in orientation control.
S
Bits 1 and 0: Positioning rotation direction
00: Automatically selected rotation direction
01: Same direction as the forward/reverse run signal
10: Fixed rotation direction
11: Automatically selected rotation direction
S
Bit 2: Selection for fixed rotation direction
0: Forward rotation of load shaft
1: Reverse rotation of load shaft
S
Bit 3: Stop position reference code
0: 12-bit binary
1: 3 digit BCD
No
11000000
C3-22
1: 3-digit BCD
S
Bit 4: Tuneup operation
0: Tuneup enabled
1: Tuneup disabled
S
Bit 5: Incremental positioning reference point
0: Previous stop reference position
1: Current stop position
S
Bit 6: Encoder selection
0: Load shaft encoder
1: Motor encoder
S
Bit 7: Rotation direction of motor and load shaft
0: Reverse
1: The same
No
---
11000000
---
C3 23
Orientation Control
Signal Selections 2
SEL-M2
*2
Dither signal pattern and gain
S
Bit 1: Dither signal pattern
0: 6 steps (83 Hz)
1: 2 steps (250 Hz)
S
Bits 4, 3, and 2: Dither signal level (H) (i.e., MGR and LGR are OFF)
000: 0.0% 011: 7.5% 110: 15.0%
No
00000000
C3-23
000: 0.0% 011: 7.5% 110: 15.0%
001: 2.5% 100: 10.0% 111: 17.5%
010: 5.0% 101: 12.5%
S
Bit 7, 6, and 5: Dither signal level (L) (i.e., MGR or LGR is ON)
000: 0% 011: 3%
110: 6%
001: 1% 100: 4% 111: 7%
010: 2% 101: 5%
No
---
00000000
---
10
Summary of Contents for CIMR-M5 Series
Page 12: ...Notes for Motor xi...