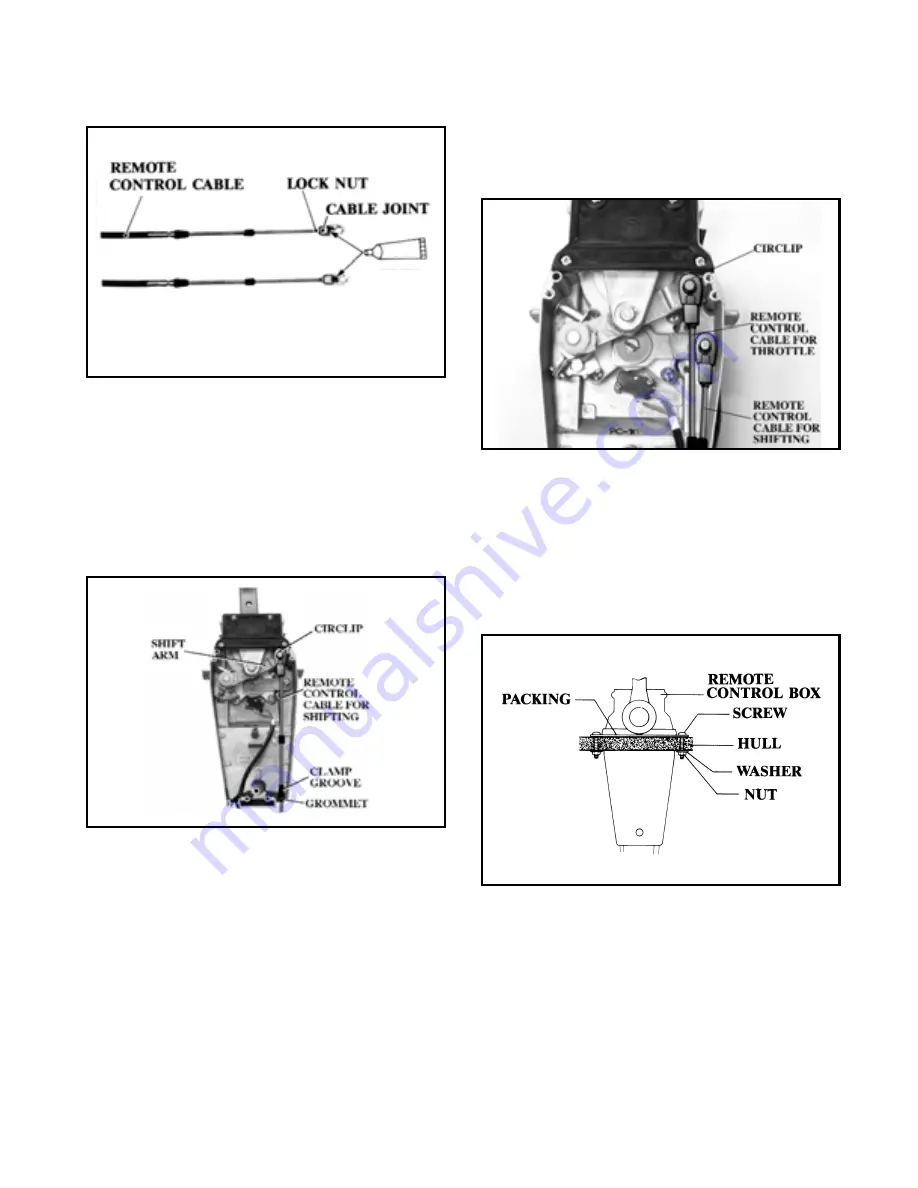
4-27
Outboard Rigging Guide - 2001
704 Binnacle Mount Remote Control Ass’y.
4.
Insert the outer sheave of the remote control
cable for shifting into the housing clamp so
that the groove on its end fits over the ridge
in the clamp. Fit the cable joint over the pin,
on the end of the shift arm, and lock it with
the circlip.
5.
Fit the grommet (accessory) in the clamp
groove.
6.
Connect the remote control cable for the
throttle to the throttle arm in the same man-
ner.
7.
Secure the back plate and mounting flange
firmly, with the five screws, and fit the pack-
ing in place.
8.
After installing the remote control cables,
temporarily secure the remote control box to
the predetermined position with the screws
and nuts (accessories).
YAMAHA
MARINE
GREASE
Summary of Contents for C-50
Page 2: ......
Page 9: ......
Page 35: ......
Page 37: ......
Page 61: ......
Page 63: ......
Page 65: ...2 2 Outboard Rigging Guide 2001 Engine Mounting Dimensions ...
Page 67: ...2 4 Outboard Rigging Guide 2001 Engine Mounting Dimensions ...
Page 71: ...2 8 Outboard Rigging Guide 2001 Transom Mounting Patterns 25HP 2 Cylinder ...
Page 72: ...2 9 Outboard Rigging Guide 2001 Transom Mounting Patterns 25X3 3 Cyl 30HP 40HP Manual Tilt ...
Page 109: ......
Page 111: ......
Page 155: ...3 44 Outboard Rigging Guide 2001 Boat Wiring Diagrams T9 9 with 703 Control ...
Page 156: ...3 45 Outboard Rigging Guide 2001 T9 9 with Switch Panel ...
Page 177: ...3 66 Outboard Rigging Guide 2001 After Market Dash Wiring ...
Page 178: ...3 67 Outboard Rigging Guide 2001 COMPLETE BOAT WIRING DIAGRAMS 70 90HP F80 F115 ...
Page 179: ...3 68 Outboard Rigging Guide 2001 Complete Boat Wiring Diagrams V4 V6 Single Engine ...
Page 180: ...3 69 Outboard Rigging Guide 2001 Complete Boat Wiring Diagrams V4 V6 Single Engine Cont d ...
Page 181: ...3 70 Outboard Rigging Guide 2001 Complete Boat Wiring Diagrams V4 V6 F115 Dual Engine ...
Page 182: ...3 71 Outboard Rigging Guide 2001 Complete Boat Wiring Diagrams V4 V6 F115 Dual Engine Cont d ...
Page 183: ...3 72 Outboard Rigging Guide 2001 Complete Boat Wiring Diagrams V6 HPDI Single Engine ...
Page 184: ...3 73 Outboard Rigging Guide 2001 Complete Boat Wiring Diagrams V6 HPDI Dual Engine ...
Page 185: ......
Page 187: ......
Page 236: ......
Page 242: ...5 5 Outboard Rigging Guide 2001 Tachometer Digital Multi function Tachometer ...
Page 359: ...6C 2 Outboard Rigging Guide 2001 E FEATURES ...
Page 376: ...7 15 Outboard Rigging Guide 2001 F15 F25 Remote Control Attach Kit REMOVAL ...
Page 406: ...NOTES ...
Page 407: ...NOTES ...
Page 418: ...Outboards 6X1 DUAL STATION SYSTEM INSTALLATION MANUAL YAMAHA MOTOR CO LTD 6X1 28199 Y2 10A 1 ...
Page 423: ...10A 6 GENERAL INFORMATION WIRING AND COMPONENT PARTS Single engine system Second station ...
Page 424: ...10A 7 Twin engine system Second station ...
Page 453: ...WIRING DIAGRAM FIRST STATION Single engine 10A 36 ...
Page 454: ...SECOND STATION Single engine 10A 37 ...
Page 455: ...10A 38 ...
Page 456: ...10A 39 ...
Page 457: ...Outboards 6X1 DUAL STATION SYSTEM SERVICE GUIDE 10B 1 ...
Page 460: ...10B 4 ...
Page 462: ...10B 6 Outboard Rigging Guide 2001 EXTERNAL VIEW OUTLINE OF FEATURES ...
Page 495: ...10B 39 Outboard Rigging Guide 2001 ...