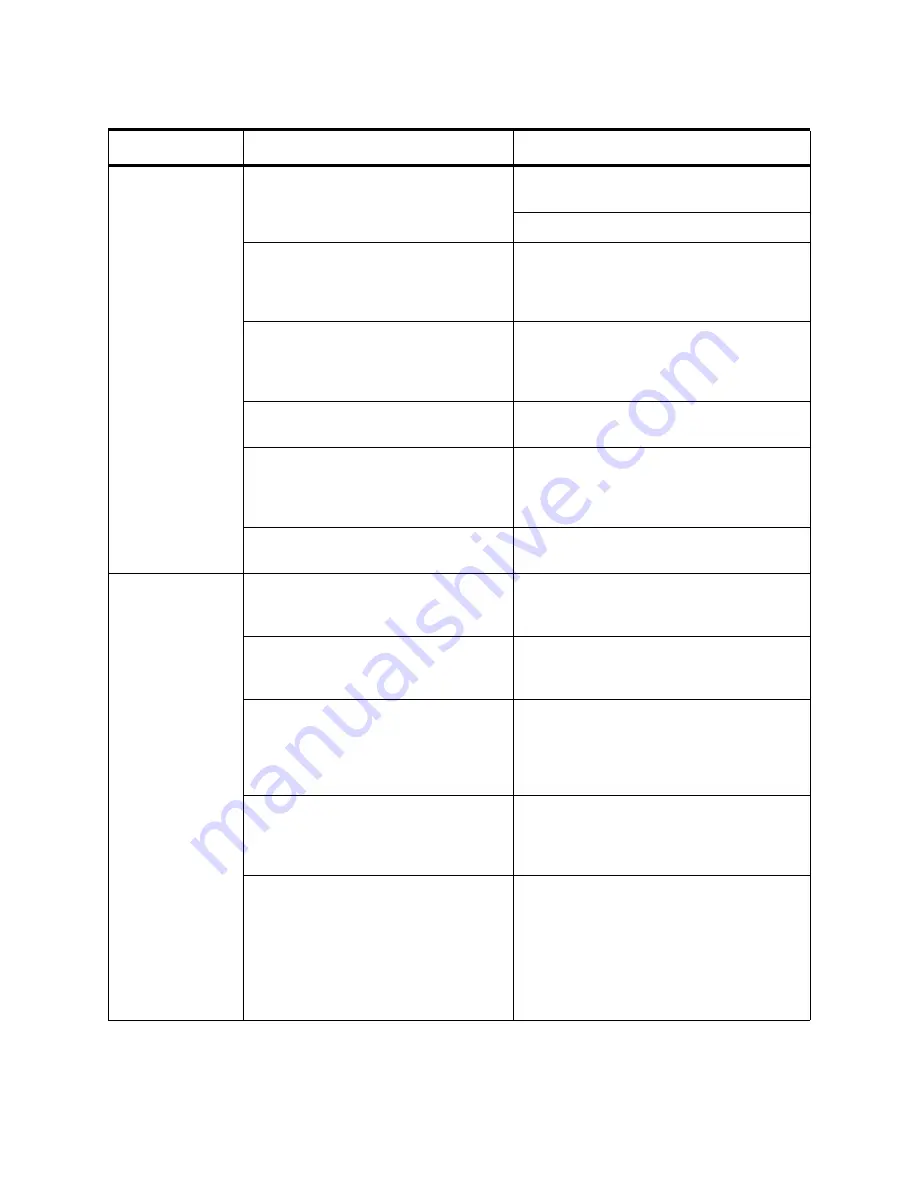
8QbTgQbUDb_eR\UcX__dY^W
)!"
=UTGU\T# %?`UbQd_bµc7eYTUD)## "
= #" "%1`bY\" "
Control not
responding to
data entry device
Bad connection between weld
processor and DEP-100S.
Check the connection between the weld
processor and DEP-100S.
Check for faulty connector or cable.
If networking, there is no network
supply or external 120 VAC
connected to the power supply.
(Required to power the DEP-100S.)
Assure that the network power supply is
connected and external 120 VAC is
supplied.
If networking, check for improper or
loose wiring at MedLAN connection.
Check for secure and proper wiring. Refer
to MedLAN wire designations described in
“Providing MedLAN Connections” on page
2-15.
Two controls share the same
MedLAN address.
Check each control’s address. Verify that
each has a unique address.
Verify that the data entry device
software is compatible with the weld
processor. (Consult your WTC
representative for assistance.)
Update software.
Faulty weld processor, faulty DEP-
100S or faulty network power pack.
Replace as necessary.
Control
sequences
without firing
SCR
The control is in No Weld.
Check the status of the WELD/NO WELD
input. Verify that the control and all data
entry devices are in Weld mode.
A fault occurred, causing the control
to complete the weld schedule in No
Weld.
Check the data entry device to determine
any fault conditions. Clear the fault(s),
correct the problem and re-initiate.
Programming error.
Check the weld schedule being initiated to
verify that the weld schedule contains a
weld function. Also verify that the weld
function has a value greater than zero for
number of cycles.
Weld processor is not sending firing
signals to the firing card. (Bad
connection between weld processor
and firing card.)
Remove power from the chassis and
check for faulty connectors or cables. Re-
seat modules and cycle power.
Is the firing card receiving firing
signals? (Is the Firing LED on the
card on during the weld function?)
If YES, check the firing card and SCR
wiring. Replace as necessary. Also check
to see if firing into an open primary or
secondary of the weld transformer.
(Check the power factor settings.)
If NO, check the weld processor card and
replace as necessary.
Problem
Possible Cause
Possible Solution
Summary of Contents for MedWeld 3005
Page 2: ...YY UTGU T UbQd_bµc 7eYTU V_b D 1 bY ...
Page 84: ...3_ e YSQdY_ c Q T 9 UTGU T UbQd_bµc 7eYTU D 1 bY ...
Page 110: ...GU T CSXUTe Uc UTGU T UbQd_bµc 7eYTU D 1 bY ...
Page 126: ...1TfQ SUT C_VdgQbU 6UQdebUc UTGU T UbQd_bµc 7eYTU D 1 bY ...
Page 144: ...CUde QbQ UdUbc UTGU T UbQd_bµc 7eYTU D 1 bY ...