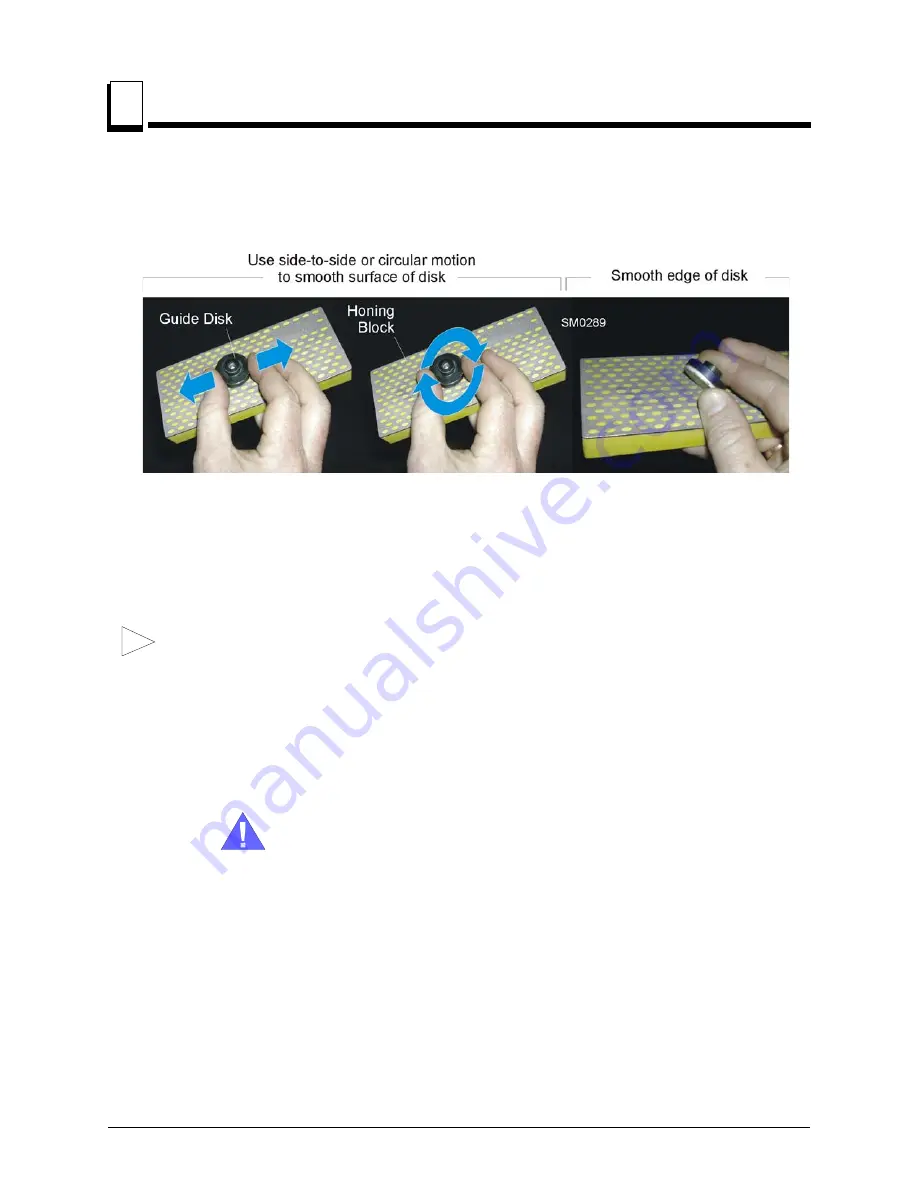
Maintenance
Ceramic Guide Disks
5
5-5
30S97doc041910
Maintenance
See Figure 5-2.
Remove the guide disk from the blade guide assembly and rub against
the honing block using even, back-and-forth or circular strokes to smooth the disk sur-
face. Use the honing block to smooth the sharp edges around the disk.
If the guide disk is too damaged to reuse, replace with a new disk. New disks should be
honed smooth before they are used to remove the rough surface created during the man-
ufacturing process. Smooth the surface and edges of the disk as described above.
2. High-performance roller/block guides only:
Check the ceramic disks are properly
spaced from the blade every 100 hours of operation. As the rollers wear, the blade will
move up, requiring adjustment of the disks. Use the provided shim or a feeler gauge to
check the disks are adjusted .008” - .010” from the blade.
See Figure 5-3.
To adjust the disks up, loosen the nuts on the outer adjustment bolts and
back the bolts out slightly. Tighten the middle bolt to raise the disk mounting plate up until
it contacts the outer bolts. Check the space between the disk and the blade. When proper
spacing is achieved, tighten the outer bolt nuts.
IMPORTANT!
The ceramic disks should be parallel to the
blade. Check the space between the insert and the blade at
each side of the insert to insure it is parallel. Use the appro-
priate outer adjustment bolt to tilt the insert mounting plate
so the insert is parallel to the blade.
FIG. 5-2
100