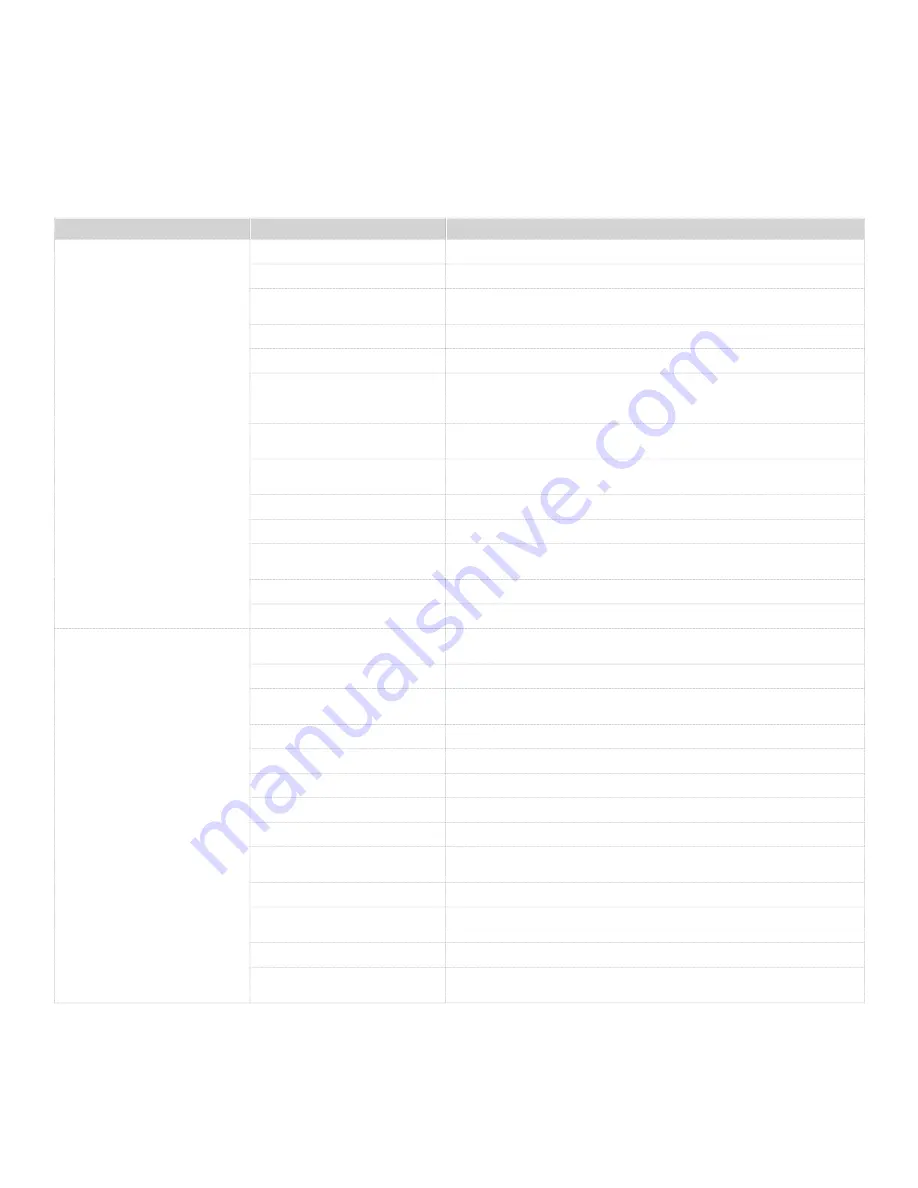
19
Wilo-WiBooster - Installation and Operation Manual
FAULT
CAUSE
REMEDIES
Pump(s) do not start
No mains voltage
Inspect fusts, cables and connections
Main switch “OFF”
Switch on main switch
Water level in break tank too low, i.e.
low-water level reached
Check break tank inlet valve/inlet pipe
Low-water level switch has triggered Check intake pressure
Low-water level switch defective
Check, if necessary replace the lowwater level switch
Electrodes incorrectly connected or
supply pressure switch incorrectly
set
Check installation or setting and correct
Intake pressure exceeds start-up
pressure
Check settings and correct if necessary
Check valve closed at pressure
sensor
Inspect, open check valve if necessary
Start-up pressure set too high
Check setting and correct if necessary
Fuse defective
Check fuses and replace if necessary
Motor protection has triggered
Check set values against the pump or motor data, measure current values and
correct setting if necessary. Check motor for defects and replace if necessary
Contactor defective
Check and replace if necessary
Turn-to-turn fault in motor
Check, if necessary replace motor or have repaired
Pump does (pumps do) not switch
off
Intake pressure fluctuates severely
Check intake pressure, if necessary take measures to stabilise supply pressure
(e.g. pressure reducer)
Intake pipe blocked or shut off
Check inlet pipe, if necessary remove blockage or open check valve
Nominal diameter of inlet pipe too
small
Check the inlet pipe, increase the crosssection for the inlet pipe if necessary
Inlet pipe incorrectly installed
Check inlet pipe, if necessary change pipe guide
Air in inlet
Check, if necessary seal pipe. Vent pumps
Impellers blocked
Check pump, if necessary replace or have repaired
Non-return valve leaking
Check, if necessary replace seal or replace non-return valve
Non-return valve blocked
Check, if necessary remove blockage or replace non-return valve
Gate valve in system closed or not
sufficiently open
Check, open the check valve completely if necessary
Volume flow too large
Check pump data and default values and correct if necessary
Check valve closed at pressure
sensor
Inspect, open check valve if necessary
Switch-off pressure set too high
Check setting and correct if necessary
Direction of motor rotation false
Check the direction of rotation and correct by changing over the phases if
necessary
continued next page
7.3
WiBooster PLC levels of access
The PLC includes three levels of control access: monitoring,
operator settings and advanced settings. These levels of access
prevent unauthorized individuals from accessing parameters
that are critical to proper function of the Wilo WiBooster. If
the “Operator Settings” or “Advanced Settings” buttons are
pressed from the main screen a keyboard will appear to allow a
password to be entered for the requested level of access.
7.3.1
Troubleshooting Guide