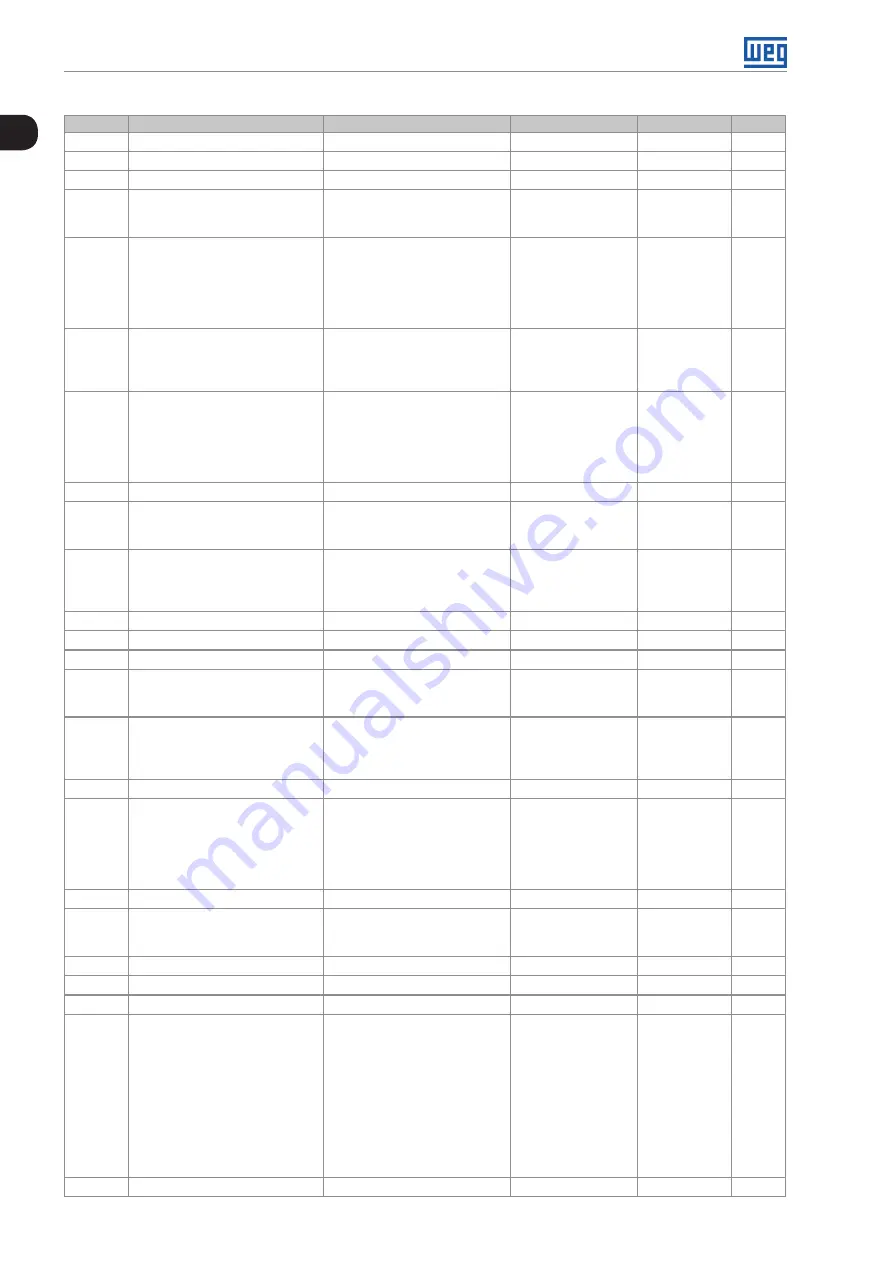
0
Quick Reference of Parameters, Alarms and Faults
0-8 | CFW300
Param.
Description
Adjustable Range
Factory Setting
Prop.
Page
P304
Skip Frequency 2
0.0 to 400.0 Hz
0.0 Hz
P306
Skip Band
0.0 to 25.0 Hz
0.0 Hz
P308
Serial Address
1 to 247
1
cfg
P310
Serial Baud Rate
0 = 9600 bits/s
1 = 19200 bits/s
2 = 38400 bits/s
1
cfg
P311
Serial Bytes Config.
0 = 8 bits, No, 1
1 = 8 bits, Even, 1
2 = 8 bits, Odd, 1
3 = 8 bits, No, 2
4 = 8 bits, Even, 2
5 = 8 bits, Odd, 2
1
cfg
P312
Serial Protocol
0 to 1 = Reserved
2 = Slave Modbus RTU
3 and 4 = Reserved
5 = Master Modbus RTU
2
cfg
P313
Action for Comminic. Error
0 = Inactive
1 = Ramp Stop
2 = General Disable
3 = Go to LOC
4 = LOC Keep Enab
5 = Cause Fault
1
P314
Serial Watchdog
0.0 to 999.0 s
0.0 s
cfg
P316
Serial Interf. Status
0 = Inactive
1 = Active
2 = Watchdog Error
ro
P320
Flying Start/Ride-Through
0 = Inactive
1 = Flying Start
2 = FS / RT
3 = Ride-Through
0
cfg
P331
Voltage Ramp
0.2 to 60.0 s
2.0 s
P332
Dead Time
0.1 to 10.0 s
1.0 s
P340
Auto-Reset Time
0 to 255 s
0 s
cfg
P352
Fan Control Configuration
0 = OFF
1 = ON
2 = CT
2
cfg
P358
(*)
Encoder Fault Config.
0 = Off
1 = F067 ON
2 = F079 ON
3 = F067, F079 ON
3
cfg
P375
(*)
Temperature NTC
0 to 100 ºC (32 °F to 212 °F)
ro
P397
Control Configuration
0000 to 000F (hexa)
Bit 0 = Slip Compens. Regen.
Bit 1 = Reserved
Bit 2 = IO Stabilization
Bit 3 = P297 Reduction
Temperature
000Bh
cfg
P399
Motor Rated Efficiency
50.0 to 99.9 %
67.0 %
cfg, V V W
P400
Motor Rated Voltage
0 to 240 V
According to
cfg, V V W
P401
Motor Rated Current
0.0 to 40.0 A
1.0 x I
nom
cfg
P402
Motor Rated Speed
0 to 30000 rpm
1720 (1310) rpm
cfg
P403
Motor Rated Frequency
0 to 400 Hz
60 (50) Hz
cfg
P404
Motor Rated Power
0 = 0.16 HP (0.12 kW)
1 = 0.25 HP (0.18 kW)
2 = 0.33 HP (0.25 kW)
3 = 0.50 HP (0.37 kW)
4 = 0.75 HP (0.55 kW)
5 = 1.00 HP (0.75 kW)
6 = 1.50 HP (1.10 kW)
7 = 2.00 HP (1.50 kW)
8 = 3.00 HP (2.20 kW)
9 = 4.00 HP (3.00 kW)
10 = 5.00 HP (3.70 kW)
According to
inverter model
cfg, V V W
P405
(*)
Encoder Pulse Number
32 to 9999
1024
cfg
Summary of Contents for CFW300 V1.3X
Page 2: ......
Page 8: ...Contents...
Page 46: ...Identification of the Inverter Model and Accessories 6 4 CFW300 6...
Page 60: ...Logical Command and Speed Reference 7 14 CFW300 7...
Page 72: ...V f Scalar Control 9 10 CFW300 9...
Page 80: ...VVW Vector Control 10 8 CFW300 10...
Page 116: ...Digital and Analog Inputs and Outputs 12 24 CFW300 12...
Page 132: ...Reading Parameters 15 6 CFW300 15...