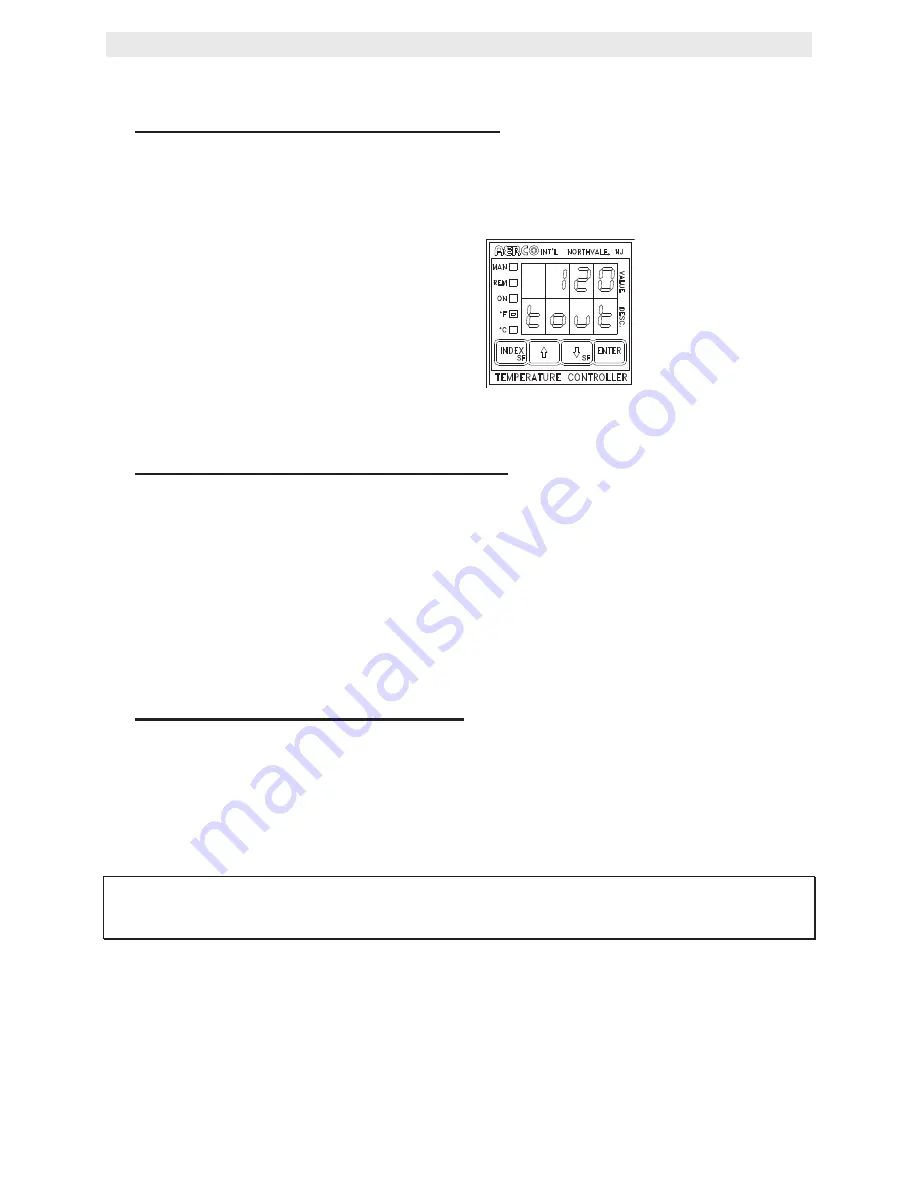
APPENDIX B
viii
x
SECURE MENU TO THE MAIN MENU
While in the SECURE menu press INDEX and the
arrow key. This will place you in the
SECONDARY menu. Press INDEX and the
arrow key again, to return to the MAIN menu.
The display will indicate:
x
SCROLLING THROUGH MENU ITEMS
To scroll through Menu items in a menu level, Press INDEX.
To scroll thru the PRIMARY, SECURE, or SECONDARY menus in reverse,
simultaneously press INDEX and the
arrow key.
To return to the first menu item of the SECONDARY menu from any other
SECONDARY menu item, without scrolling, simultaneously press the INDEX and the
arrow
key.
x
CHANGING MENU ITEM VALUES
To change the value of a selected menu item press either the
arrow key, to increase
the item value, or the
arrow key to decrease the item value. Press, ENTER to accept
the
change.
NOTE:
ENTER must be pressed after changing the value of a parameter If ENTER is not pressed
the controller will default to the value displayed prior to the change.
Summary of Contents for AERCO KC Series
Page 51: ...TROUBLESHOOTING 41...
Page 65: ...APPENDIX C ix...
Page 72: ...APPENDIX F xvi...
Page 74: ...APPENDIX F xviii...
Page 76: ...APPENDIX G xx...
Page 77: ...APPENDIX G xxi...
Page 78: ...APPENDIX H xxii...
Page 79: ...APPENDIX H xxiii...
Page 80: ...APPENDIX H xxiv...