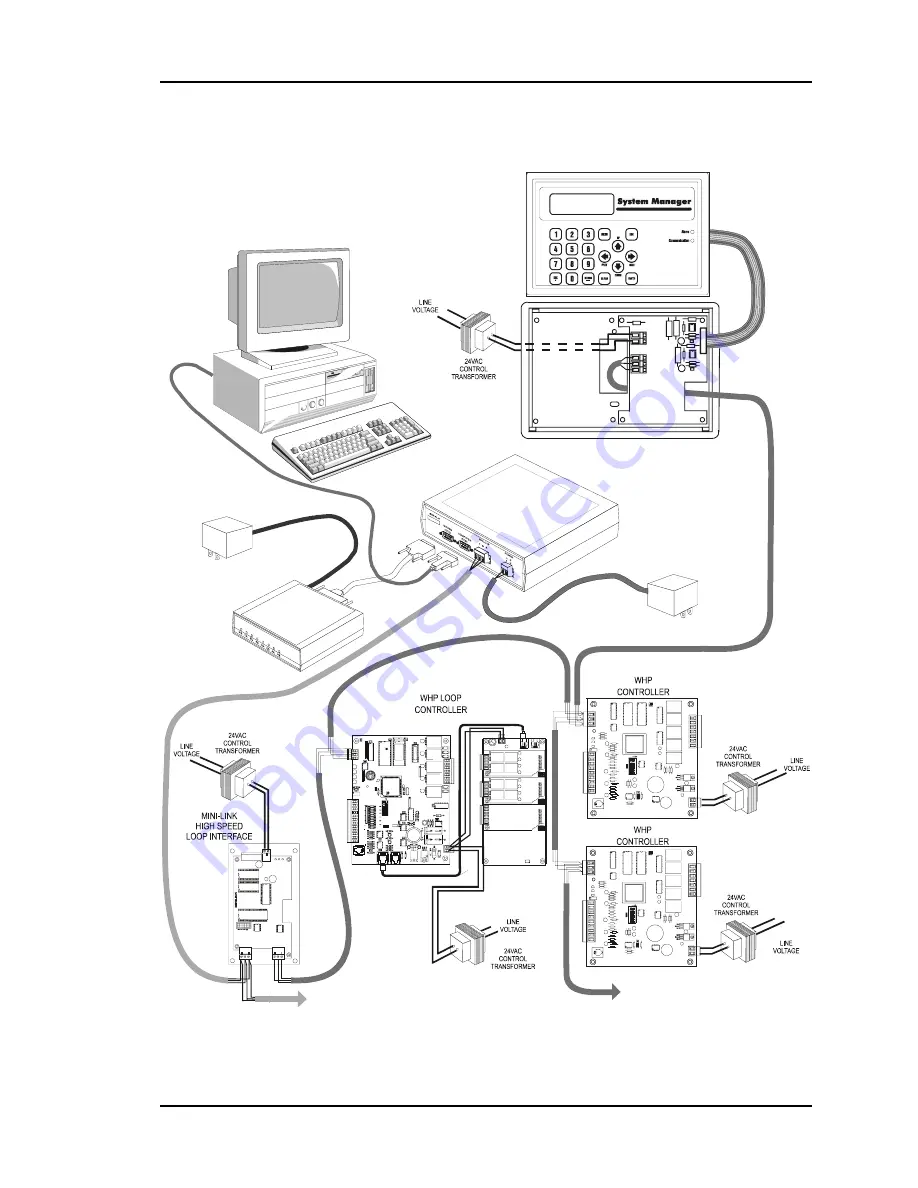
WattMaster WHP
Section 4
Start-Up and Troubleshooting
4-3
All communications wiring should be labeled to avoid confusion and to aid future
servicing.
COMPUTER
(OPTIONAL)
SYSTEM MANAGER
Remote Link
(OPTIONAL)
UNIT COMES WITH
STANDARD WALL MOUNT
120/24 VAC POWER SUPPLY
( MAY ALSO BE POWERED FROM 24VAC )
COMM LINK II
INTERFACE
(MULTIPLE LOOP)
TO OTHER MINILINKS
(NETWORK TERMINALS ONLY)
TO OTHER WHP CONTROLLERS
YS101716 REV. 1
SYSTEM MANAGER POWER SUPPLY
SHLD
COMMUNICATIONS
RS-485
R
T
GND
24VAC
POWER
LOOP
NETWORK
T
T
SH
SH
R
R
24V
A
C
GN
D
RELAY
OUTPUT
COM
1-3
OUT
OUT
1
2
COM
4-5
OUT
OUT
OUT
3
4
5
24VAC
24VAC
GND
GND
PWR
COMM
T
T
SHLD
SHLD
LD4
REC.
12V
AIN
1
2
3
4
5
GND
GND
AOUT
AIN
AIN
AIN
AIN
4-5
OUT
COMM
TEST
32K
8K
RAM
EPROM
ADDRESS ADD
PRESSURE
SENSOR
485
COMM
R
R
YS101564
EW
D
O
G
0-
5
VD
C
0-
1
VD
C
CPU
RELAY
OUTPUT
COM
1-3
OUT
OUT
1
2
COM
4-5
OUT
OUT
OUT
3
4
5
PWR
COMM
LD4
REC.
12V
AIN
1
2
3
4
5
GND
GND
AOUT
AIN
AIN
AIN
AIN
4-5
OUT
COMM
TEST
32K
8K
RAM
EPROM
ADDRESS ADD
PRESSURE
SENSOR
485
COMM
YS101564
EW
D
O
G
0-
5
VD
C
0-
1
VD
C
CPU
AIN1
AIN2
AIN3
AIN4
GND
AOUT1
YS101784
4 ANALOG IN MOD I/O BD.
4RLY IO BD.
4RLY IO BD.
YS101790
YS101790
2
4
V
A
C
G
N
D
RL
Y
1
D1
D2
D3
D4
D5
CX
3
RAM
EPROM
C3
C2
U6
P
H
IL
IP
S
CX6
C1
CX2
U2
U3
PAL
CX4
U4
TUC-5R PLUS
YS101816 REV. 2
V1
V2
V3
V5
V4
TB2
4
NETWORK
TOKEN
16
32
8
SW1
ADD
2
1
ADDRESS
V6
PO
W
ER
GND
24VAC
L1
D1
6
R6
C9
SC1
R1
1
U1
1
MC340
64A
D1
3
C16
9936
VR2
7824C T
M
TB4
R2
7
C13
R1
0
VR1
C1
9
C1
8
NE5090NPB3192
0PS
U8
CX
8
U9
X1
R7
D1
0
R13
D12
C7
CX10
U10
CX12
U12
U14
CX14
PJ
3
PJ
2
PJ1
EXPANSION
PRESSURE
SENSOR
T'STAT
C17
D15
R26
C20
R25
R24
R22
U15
CX13
U13
C15
R19
R15
C14
D1
8
D1
7
PU1
PU2
PU3
PU4
PU5
PU7
D6
D7
D8
D9
D11
D14
C12
C10
0-
5
VD
C
0-
1
VD
C
JP1
C1
1
X2
GND
TB3
INPUTS
GND
GND
+VDC
AIN1
AIN2
AIN3
AIN4
AIN5
AOUT1
AOUT2
AIN7
RN4
1
RN5
RS-485
CX5
U5
R
TB1
SHLD
T
COMM
COMM
RN3
1
RN1
U1
CX1
1
LD6
COMM
PWR
LD7
LED1
LED2
LD9
LD8
R1
U7
RV1
VREF ADJ
R28
+VREF
5.11V
TEST POINT
EWDOG
D19
RN2
1
COM1-3
COM4-5
R5
R4
R3
R2
R1
RL
Y
2
RL
Y
3
RL
Y
4
RL
Y
5
CX15
(1 MEG)
HH
P1
C2
1
03/31/04 03:38PM WED
OCCUPIED
NO ALARMS
Figure 4-2: Communications Loop Routing
Summary of Contents for Water Source Heat Pump
Page 1: ...WHP Water Source Heat Pump Design Installation Operations Manual Revision 02A...
Page 2: ......
Page 4: ......
Page 6: ......
Page 22: ...Section 1 WattMaster WHP 1 16 Design Guide Notes...
Page 48: ......
Page 80: ...Section 3 WattMaster WHP 3 32 Programming Notes...
Page 125: ...WattMaster WHP Section 4 Start Up and Troubleshooting 4 43 Notes...