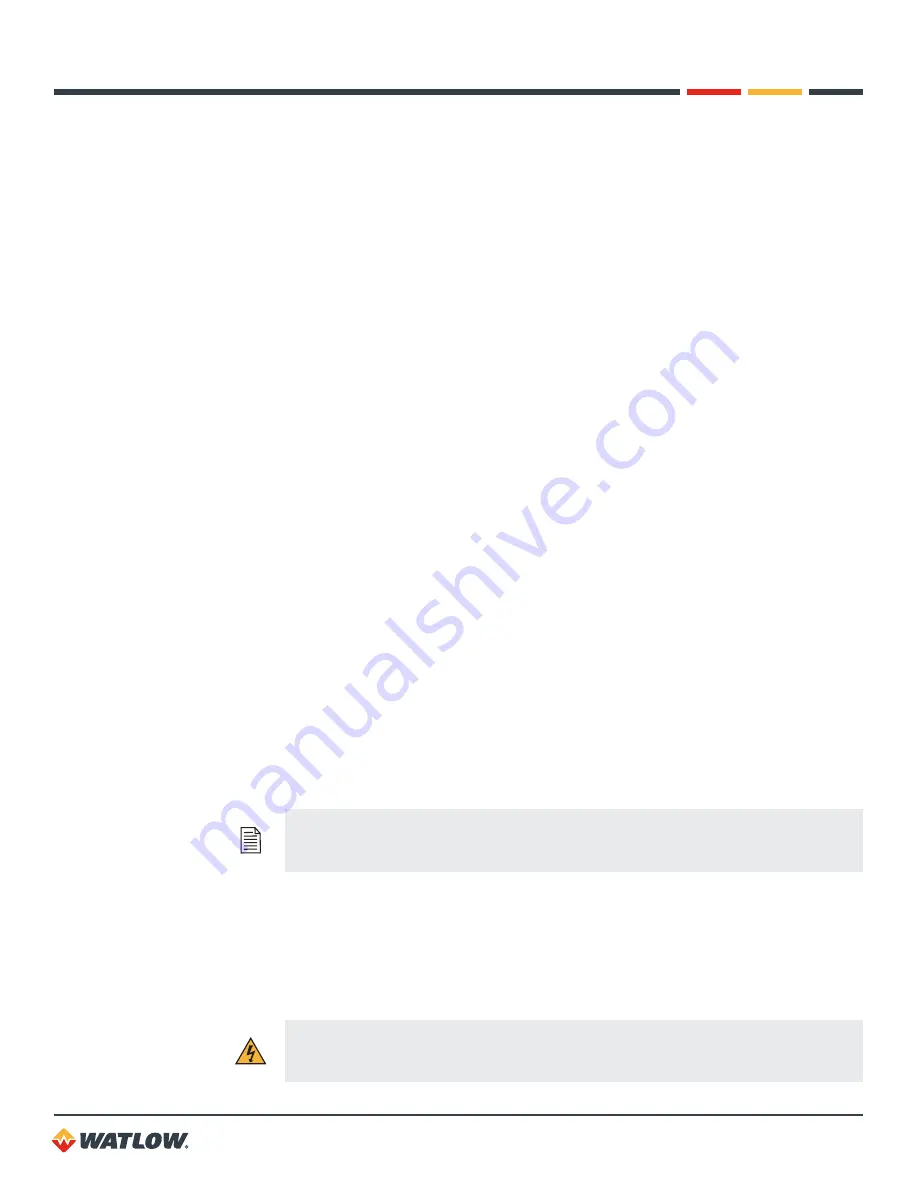
CLS200 Series User’s Guide
Chapter 3: Using CLS200
58
Prerequisites
Before autotuning the controller, it must be installed with control and sensor circuitry and the thermal
load in place.
It must be safe to operate the thermal system, and the approximate desired operating temperature
(setpoint) must be known.
The technician or engineer performing the autotune should know how to use the controller front
panel or MMI software interface to do the following:
1. Select a loop to operate and monitor.
2. Set a loop’s setpoint.
3. Change a loop’s control status (
MAN
,
TUNE
,
AUTO
).
4. Read and change the controller’s global and loop setup parameters.
Background
Autotuning is performed at the maximum allowed output. If you have set an output limit, autotuning
occurs at that value. Otherwise, the control output is set to 100% during the autotune. Only the heat
output (output 1) of a loop may be autotuned.
The PID constants are calculated according to process’s response to the output. The loop need
not reach or cross setpoint to successfully determine the PID parameters. While autotuning the
controller looks at the delay between when power is applied and when the system responds in order
to determine the integral term (TI). The controller then looks for the slope of the rising temperature
to become constant in order to determine the proportional band (PB). The derivative term (TD) is
derived mathematically from the TI.
When the controller has finished autotuning, the loop’s control status switches to
AUTO
. If the
process reaches 75% of the setpoint or the autotuning time exceeds 30 minutes, the controller
switches to
AUTO
and applies the PID constants it has calculated up to that point.
The autotune is started at ambient temperature or at a temperature above ambient. However, the
temperature must be
stable
and there must be sufficient time for the controller to determine the new
PID parameters.
Performing an Autotune
NOTE!
A loop must be stable at a temperature well below the setpoint in order to
successfully autotune. The controller will not complete tuning if the temperature exceeds
75% of setpoint before the new parameters are found.
The following procedure explains how to autotune a loop:
1. Select the single loop display of the loop to be tuned.
2. Ensure the loop’s process variable is stable and the loop is in
MAN
control status.
3. Set the setpoint to a value as near the normal operating temperature as is safe for the system.
WARNING!
During autotuning, the controller will set the output to 100% until the process
variable rises near the setpoint. Set the setpoint within the safe operating limits of your
system.