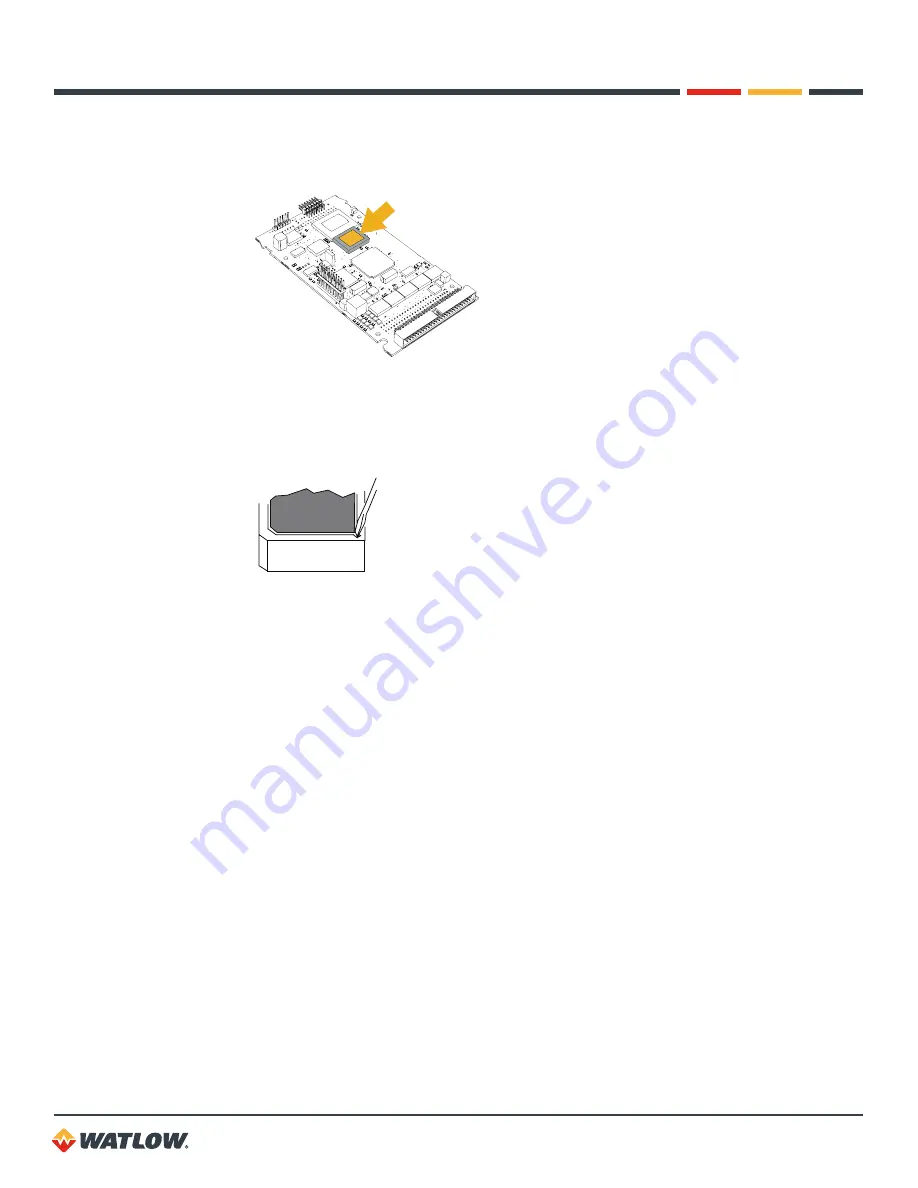
CLS200 Series User’s Guide
Chapter 8: Troubleshooting and Reconfiguring
152
8. Locate the EPROM on the processor board. The EPROM is a 32-pin socketed chip that is
labeled with the model, version and checksum.
Figure 8.5
— EPROM Location
9. Remove the existing EPROM from its socket with an IC extraction tool or a jeweler’s flathead
screwdriver.
Figure 8.6
— Remove EPROM
10. Carefully insert the new EPROM into the socket. Make sure that the chip is oriented so that its
notch fits in the corresponding corner of the socket.
11. Reverse steps 3 through 7 to reassemble the unit. However, at step 6 insert the two-board
assembly straight in to the carrier making sure all four arms latch on the boards.
12. Power up the controller.
13. Re-enter the controller settings, if necessary.
Removing or Replacing the Battery
The lithium battery in the battery-backed RAM module on the processor board should be removed
and disposed of properly if decommissioning the controller. It may also be replaced, if needed during
the life of the controller.
To remove the battery:
1. Follow steps 1 to 7 of the procedure
Replacing the EPROM on page 150
to access the
processor board.
2. Locate the battery backed RAM module. See
Figure 8.10 — Single-Ended Input Circuit in
Sixteen-Loop Controllers on page 157
.
3. Insert a small flat blade screwdriver vertically into the slot on one side of the RMA module.
4. Angle the screwdriver handle toward the center of the RAM chip gently until the side with the